Link Ball
With the link ball, a highly accurate bearing steel ball used in the spherical area is first encased in the holder by die cast molding and then is specially welded with the shank. This unique process enables the mirror surface of the steel ball to be transferred or duplicated on the spherical surface inside the holder to ensure full contact between the ball and the holder. As a result, smooth motion is achieved with the smallest possible clearance.
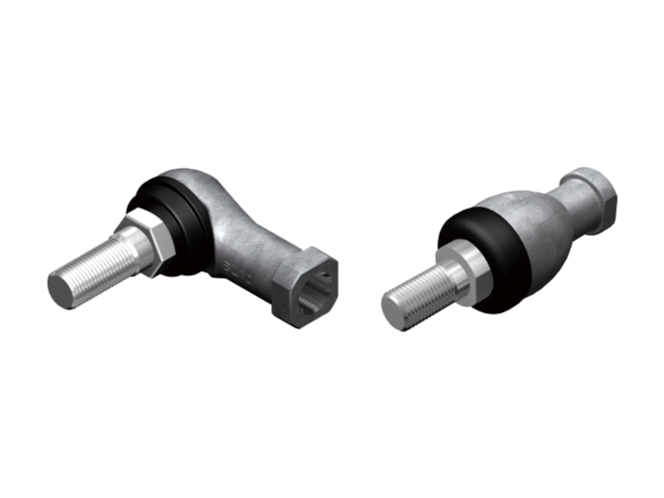
Types
Highlight feature tags
- Compact
- Wear resistance
- Axial direction
- Radial direction
- With boot attached
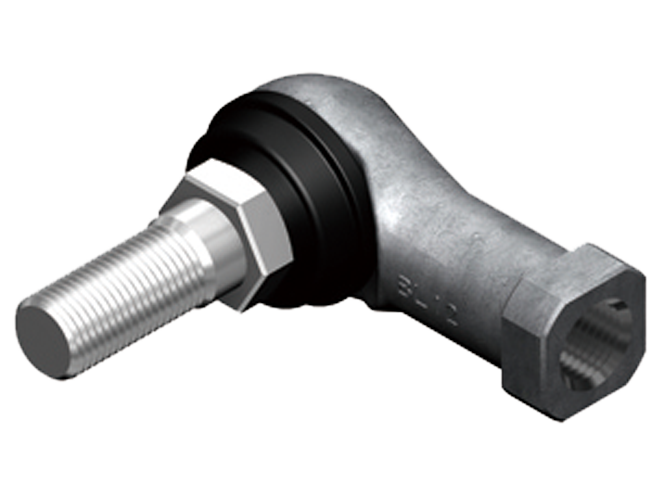
- Radial direction
- Compact
- With boot attached
- Wear resistance
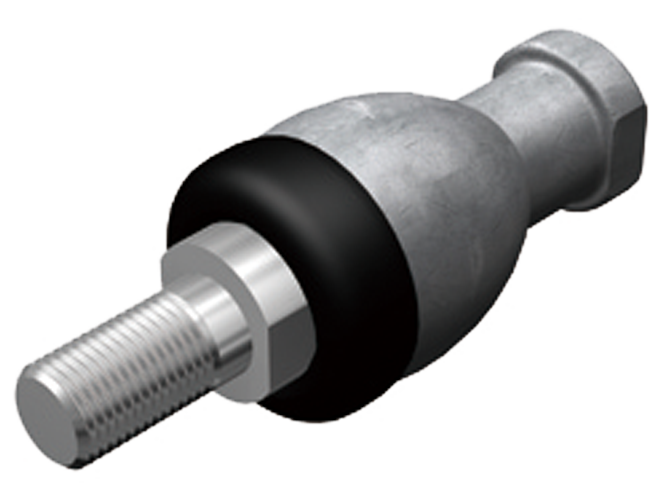
- Axial direction
- Compact
- Wear resistance
- With boot attached
Search products by various conditions
Features
Structure and Features
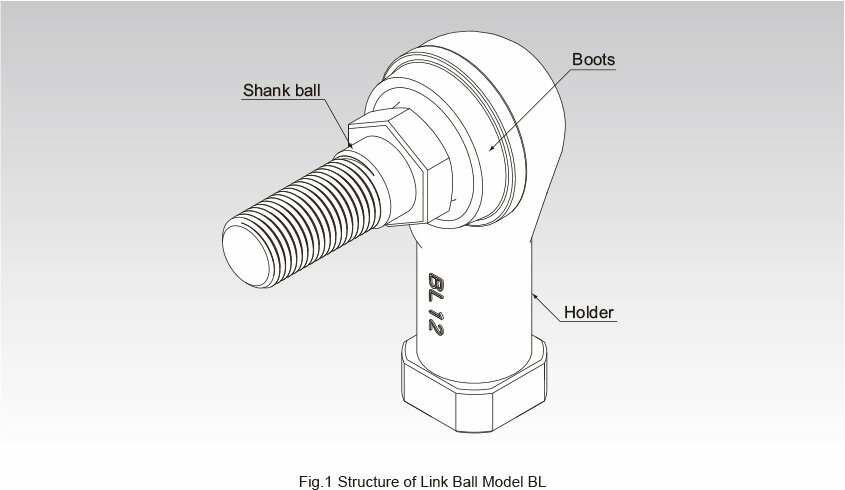
With the Link Ball, a highly accurate bearing steel ball used in the spherical area is first encased in the holder by die cast molding, and then is specially welded with the shank. This unique process enables the mirror surface of the steel ball to be transferred or duplicated on the spherical surface inside the holder to ensure full contact between the ball and the holder. As a result, smooth motion is achieved with a minimum clearance.
Compact Design
Model BL has an adequately firm and yet extremely compact shape because of a highly balanced design. This model is optimal for use in an automobile height sensor or transmission control.
Achieves Sphericity of 0.001 mm
The spherical surface of the shank ball is transferred on the inner surface of the holder while maintaining the sphericity of the bearing steel ball. This allows smooth motion to be achieved with a minimum clearance and provides favorable operability and feel to the link motion.
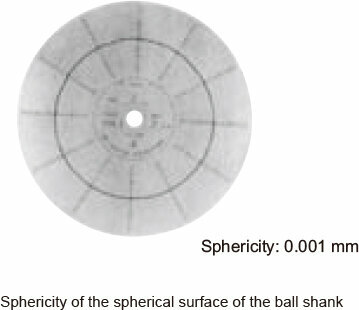
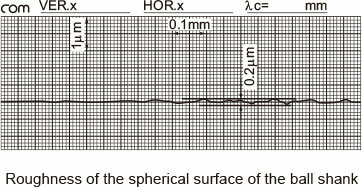
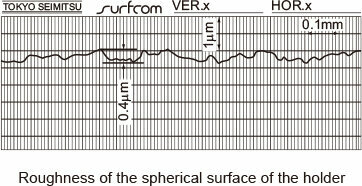
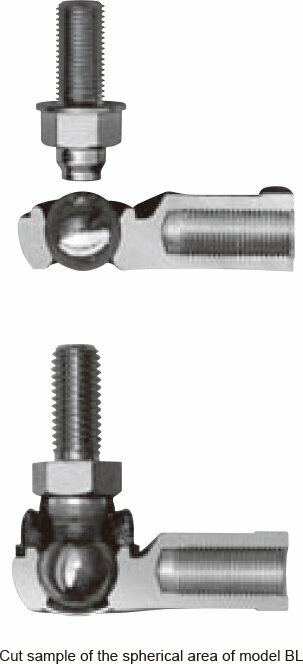
Two Types of Holder Material
Model BL-A uses the newly developed high-strength aluminum alloy "A-1 Alloy" (see Alloy ), which is light and highly resistant to wear.
Models BL6 and above and model RBI uses the proven high strength zinc alloy (see High Strength Zinc Alloy ).
High Lubricity
The boot contains grease for high lubricity and increased wear resistance.
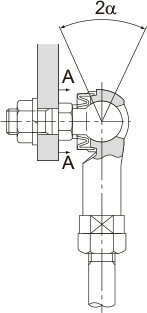
Large Hexagonal Bolt Seat
The hexagonal bolt seat of the shank has the same dimensions as the seating surface for small hexagon head bolts in accordance with automotive specifications. This prevents the seating surface from sinking and ensures a stable link motion mechanism.
Equipped with a Boot for Protection against Muddy Water
Use of a boot with high trackability in the ball shank prevents muddy water from entering the spherical area even in a muddy environment. Accordingly, types equipped with boots are used also in outdoor applications and automobile parts under the chassis. For details, see the muddy water test data (Durability Tests with Link Ball Model BL
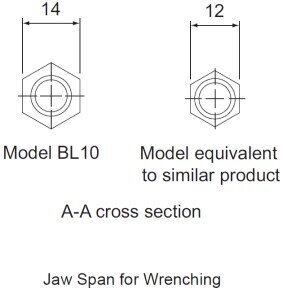
Alloy
High Strength Aluminum Alloy "A-1 Alloy"
"A-1 Alloy," a newly developed high strength aluminum alloy, is an alloy with Al-Zn-Si3 being the main components, is used in the holder of model BL-A. Information on the mechanical properties, physical properties, and wear resistance of materials is presented below.
*The figures shown are target values—these figures are not guaranteed.
● Features of the A-1 Alloy
・ Achieves one of the highest strengths among the existing aluminum die cast alloys.
・ Has yield strength approximately twice that of the commonly used aluminum die cast alloy (ADC 12).
・ Has hardness equal to the high strength zinc alloy and achieves high wear resistance.
・ Achieves specific gravity less than a half of the high strength zinc alloy to allow significant weight saving.
・ Highly corrosion resistance and can be used as an automotive part related to wheel control.
● Mechanical Properties
Tensile strength |
343 to 392 N/mm2 |
Tensile yield strength (0.2%) |
245 to 294 N/mm2 |
Compressive strength |
490 to 637 N/mm2 |
Compressive yield strength (0.2%) |
294 to 343 N/mm2 |
Charpy impact |
0.098 to 0.196 N・m/mm2 |
Elongation |
2 to 3 % |
Hardness |
140 to 160 HV |
● Physical Properties
Specific gravity |
3 |
Melting point |
570℃ |
Specific heat |
793 J/(kg・k) |
Linear expansion rate |
22×10-6 |
High Strength Zinc Alloy
The high strength zinc alloy used in the holders of models BL and RBI has been developed as a bearing alloy by mixing Al, Cu, Mg, Be and Ti as well as zinc as the base component. It is excellent in mechanical properties, seizure resistance and wear resistance. Information on mechanical properties, physical properties, and wear resistance is presented below.
*The figures shown are target values—these figures are not guaranteed.
● Mechanical Properties
Tensile strength |
275 to 314 N/mm2 |
Tensile yield strength (0.2%) |
216 to 245 N/mm2 |
Compressive strength |
539 to 686 N/mm2 |
Compressive yield strength (0.2%) |
294 to 343 N/mm2 |
Fatigue strength |
132 N/mm2×107(Schenk bending test) |
Charpy impact |
0.098 to 0.49N・m/mm2 |
Elongation |
1 to 5 % |
Hardness |
120 to 145 HV |
● Physical Properties
Specific gravity |
6.8 |
Melting point |
390℃ |
Specific heat |
460 J/(kg・k) |
Linear expansion rate |
24×10-6 |
● Wear Resistance
The wear resistance of the high strength zinc alloy is superior to that of class-3 brass and class-3 bronze, almost equal to that of class-2 phosphor bronze.
Amsler wear-tester |
|
Test piece rotation speed |
185 min-1 |
Load |
392 N |
Lubricant |
Dynamo oil |
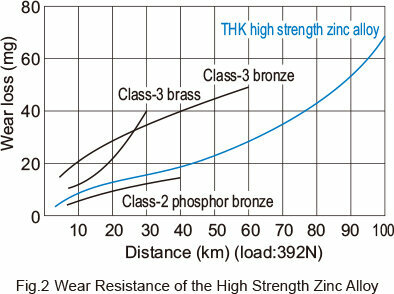
How Load Directions Are Called
Regardless of the shape, the direction of the load applied to the Link Ball is called "axial direction" if it is parallel to the axis of the ball shank, and "radial direction" if it is perpendicular to the axis.
Pushing Load and Pulling Load
Of the loads applied in the axial direction, the load in the direction of the ball shank being pressed toward the holder is called "pushing load" and the load in the direction of the ball shank being pulled from the holder is called "pulling load."
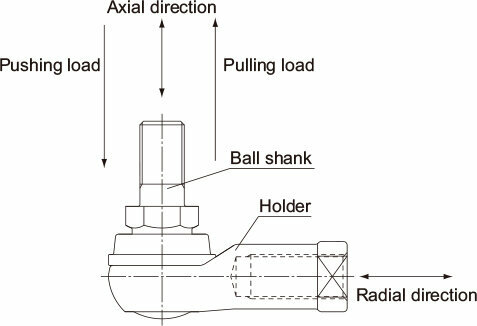
● Direction of applied load
The following table shows the load application direction of each model. Avoid using the product in a different load application direction. Failure to do so may damage the product.
Model No. | Axial direction | Radial direction |
---|---|---|
Model BL | X | ○ |
Model BL-A | X | ○ |
Model RBI | ○ | X |
Durability Tests with Link Ball Model BL
Purpose of the Tests
The tests were conducted to identify the performance difference between THK Link Ball model BL and an equivalent product of a competitor. As a result, model BL has been used in joints for transmission control units of automobiles, trucks and buses and for steering mechanisms of agricultural tractors.
Tested Product, Test Items, Test Conditions and Test Results
Test item |
Tested model No. |
Test conditions | |||||||||
---|---|---|---|---|---|---|---|---|---|---|---|
Applied load |
Rotation |
Frequency | Total num- ber of rev- olutions or time |
Service environ- ment |
Load conditions, etc. | ||||||
Rotation- |
THK |
±1760N |
Rotation angle:
θ=±20° |
40 times/min. |
1,000,000 cycles |
Normal tem- perature |
![]() |
||||
Lowtemperature |
THK |
±1225N (Radial direction) |
Rotation angle: θ=±30° |
60 times/min. | -30℃ |
Low-temperature retention time: 280 hours Motion in the rotational direction |
|||||
High |
100℃ |
High temperature retention time: 280 hours Motion in the rotational direction |
|||||||||
Muddywater rotation durability |
Normal tem- perature |
![]() |
|||||||||
Muddy- |
THK |
Rocking |
Test |
Test Result | Evaluation | |||||||||
---|---|---|---|---|---|---|---|---|---|---|---|
Sample No. |
Change in clearance(μm) | Conditions of the holder, etc. | |||||||||
Radial direction |
Axial direction |
||||||||||
Rotation and rocking durability |
THK |
(1) | 26 | 42 |
The shank was capable of smoothly rotating after the 1-million cycle test, and capable of continuously operating. |
|
|||||
(2) | 25 | 40 | |||||||||
compet- itor’s |
(1) |
Broke in the holder neck after 8,600 cycles |
Wear and damage were observed in the holder’s spherical area in approx. 150,000-cycle operation. |
|
|||||||
154 | 60 | ||||||||||
(2) |
Broke in the holder |
||||||||||
62 | 20 | ||||||||||
Lowtemperature rotation durability |
THK |
(1) | 63 | 65 |
The boot did not show a crack or the like at low tem- perature |
|
|||||
(2) | 56 | 59 | |||||||||
High |
(1) | 79 | 84 |
The boot did not show a crack or the like at low temperature |
|
||||||
(2) | 74 | 78 | |||||||||
Muddy- |
(1) | 48 | 51 |
No muddy-water penetration that may cause wear was observed. |
|
||||||
(2) | 57 | 63 | |||||||||
(1) | 32 | 38 | |||||||||
(2) | 35 | 42 | |||||||||
Muddy- |
compet- itor’s |
(1) | 240 | 105 |
Muddy water penetrated the boot, the spherical area showed chipping and the boot had cuts. |
|
|||||
(2) | 246 | 107 |
Comprehensive Evaluation
As a result of comparing THK Link Ball model BL10D and a competitor’s product in representative durability tests, it is demonstrated that model BL10D is superior in strength and wear resistance of the holder and sealability of the boot.These features are achieved through THK’s unique manufacturing process for the holder and the shank, the material used, the structure of upper and lower grease pockets on the spherical area and the development of a highly sealable boot.