LM Roller Precautions on Use
Handling
- Do not disassemble the parts. This will result in loss of functionality.
- Take care not to drop or strike the LM Roller. Doing so may cause injury or damage. Giving an impact to it could also cause damage to its function even if the product looks intact.
- When handling the product, wear protective gloves, safety shoes, etc., as necessary to ensure safety.
Precautions on Use
- Prevent foreign material, such as cutting chips or coolant, from entering the product. Failure to do so may cause damage.
- If the product is used in an environment where cutting chips, coolant, corrosive solvents, water, etc., may enter the product, use bellows, covers, etc., to prevent them from entering the product.
- If foreign material such as cutting chips adheres to the product, replenish the lubricant after cleaning the product.
- Do not use the product at temperature of 80℃ or higher.
- Do not use undue force when fitting parts (pin, key, etc.) to the product. This may generate permanent deformation on the raceway, leading to loss of functionality.
Dust-proofing and Lubrication
- Foreign matter that gets inside the LM Roller due to inadequate dust-proofi ng is very difficult to remove and is apt to cause damage to the raceway and the LM Roller. Please take extra care to ensure that the unit is protected from dust and other contaminants.
- The model SE and SEB Fixtures for the LM Roller are equipped with a special rubber wiper that helps provide effective protection against dust and other contaminants. When attaching either Fixture, apply grease between the double lips, as shown in Fig.1 , for additional protection.
-
If the unit is in a location exposed to cutting chips or welding spatter, it must be protected with an accordion-type or telescoping dust cover or the like, or equipped with a wiper reinforced with a metal plate, as shown in Fig.2 .
-
Two strategies for laterally oriented protection against contaminants are illustrated in Fig.3
- This unit needs much less lubricant than a sliding guide, making lubrication easier to manage.The same type of grease or lubricant used on ordinary bearings will suffice, but for optimal lubricant retention the best options are lithium grease no. 1 or 2, or a moderately viscous oil designed for sliding surfaces, or turbine oil.
When necessary, lubricate the LM Roller by adding drops of lubricant through the oil hole on the back of the retainer, or dribble or smear lubricant directly on the raceway. If the LM Roller is used only infrequently, grease can be smeared directly on the roller. - Do not mix different lubricants. Mixing greases using the same type of thickening agent may still cause adverse interaction between the two greases if they use different additives, etc.
- Micro-strokes tend to obstruct oil film to form on the raceway in contact with the rolling element, and may lead to fretting corrosion. Take consideration using grease offering excellent fretting prevention. It is also recommended that a stroke movement corresponding to the length of the LM Roller be made on a regular basis to make sure oil film is formed between the raceway and rolling element.
- When using the product in locations exposed to constant vibrations or in special environments such as clean rooms, vacuum and low/high temperature, use the grease appropriate for the specification/environment.
- The consistency of grease changes according to the temperature. Take note that the slide resistance of the LM Roller also changes as the consistency of grease changes.
- After lubrication, the slide resistance of the LM Roller may increase due to the agitation resistance of grease. Be sure to perform a break-in to let the grease spread fully, before operating the machine.
- Excess grease may scatter immediately after lubrication, so wipe off scattered grease as necessary.
- The properties of grease deteriorate and its lubrication performance drops over time, so grease must be checked and added properly according to the use frequency of the machine.
- The greasing interval varies depending on the use condition and service environment. Set the final lubrication interval/amount based on the actual machine.
Mounting Reference Surface
To help correctly mount the LM Roller in the traveling direction, it has a mounting reference surface on the side face of the raceway base. The reference surface is on the opposite side of the THK logo.
Mounting Precision
To maximize the performance of the LM Roller, it is necessary to distribute the load as evenly as possible when mounting the product. Fig.4 For the parallelism between the roller and the raceway indicated in , we recommend 0.015 mm or less against 100 mm. For the allowable tilt of the roller in the longitudinal direction, 0.01 mm or less against 100 mm is recommended.
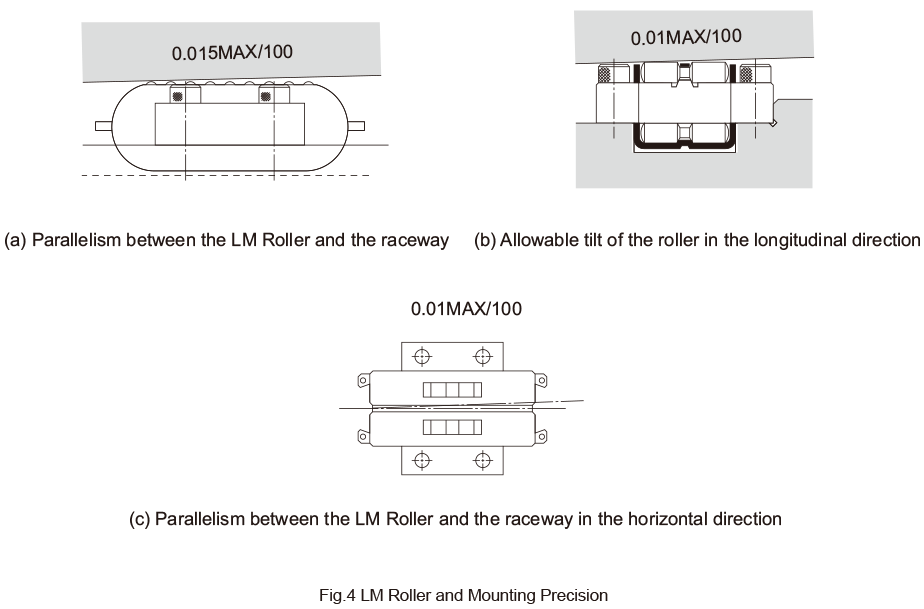
Storage
When storing the LM Roller, enclose it in a package designated by THK and store it in a room in a horizontal orientation while avoiding high temperature, low temperature and high humidity.
Disposal
Dispose of the product properly as industrial waste.