Dec 13, 2023
Products
Rotary Bearings for Multi-Axis Multitasking Machine Tools
- Product Introduction
- Machine Tools
- Transfer Robot
- Articulated Robot
- THK Online Services
- High Rigidity
- Rotary Bearing
- High Accuracy
- High Speed
Machine tools are indispensable in the manufacture of industrial products. Because of this, the performance of machine tools is being pushed ever further as industry evolves and technology advances. This article will focus on the theme of rotary bearings for multi-axis multitasking machine tools.
Machine Tool Trends
The field of machine tools has, in recent years, seen progress made in multitasking machine tools with an increasing number of axes. Initially there were only three linear axes (X, Y, and Z), but now there are 5-axis machines on the market that have an additional two axes—a workpiece rotating axis and a diagonal axis—as well as multitasking machining centers that also include a lathing function. The processes performed by multiple machine tools are now being consolidated into single machining centers.
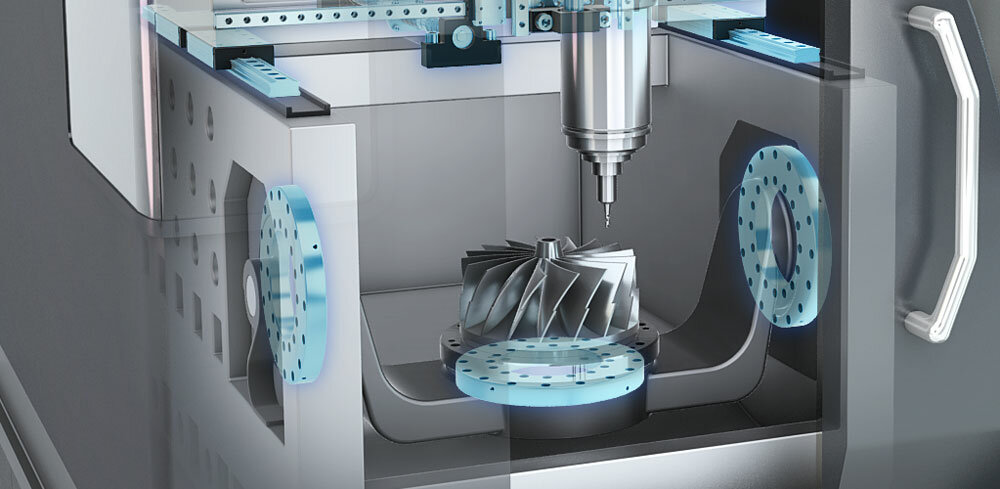
Multi-axis multitasking machines offer improved machining accuracy and productivity, save factory floor space, and reduce management and labor costs.
Performance Required of Rotary Components
Rigidity and accuracy are the most important performance requirements for a machining center’s rotary components, as they directly impact workpiece machining accuracy. Multi-axis machine tools like 5-axis machining centers have even more axes, and the displacement and error of the rotary components are cumulative, meaning that the rigidity and accuracy of each have an even greater impact on machining accuracy. For this reason, each rotary component must be highly rigid and precise. Additionally, machining centers with an added lathing function spin their rotating axis at high speeds with workpieces loaded onto them, so the rotary components of these rotating axes must have excellent high-speed performance in addition to the aforementioned rigidity and accuracy. This article introduces THK's cross-roller rings and two double-row angular rings, the Double-Row Angular Contact Roller Ring Model RW and the High-Speed Double-Row Angular Contact Ring Model BWH, which are ideal for the evolving needs of machine tools.
Cross-Roller Ring Structure and Features
Cross-roller rings are highly rigid rotary bearings individually capable of tolerating radial load, axial load, and moment from all directions. With orthogonally arranged rollers set in a 45-degree contact structure as their rolling elements, cross-roller rings provide both smooth rotation and excellent rigidity. Spacer retainers set between these rollers act to reduce friction between them, creating sustained stability of motion.
While angular contact ball bearings and tapered roller bearings are also capable of handling moment loads, you generally have to use two or more of them together. A major feature of cross-roller rings is that only one is required to achieve the same end, making for a thinner, lighter structure overall. Thanks to these advantages, cross-roller rings have seen widespread use in applications that require high rigidity in small spaces, such as the rotating and joint axes of robots and the rotating and diagonal axes of machining centers, and they have won the confidence of customers for many years.
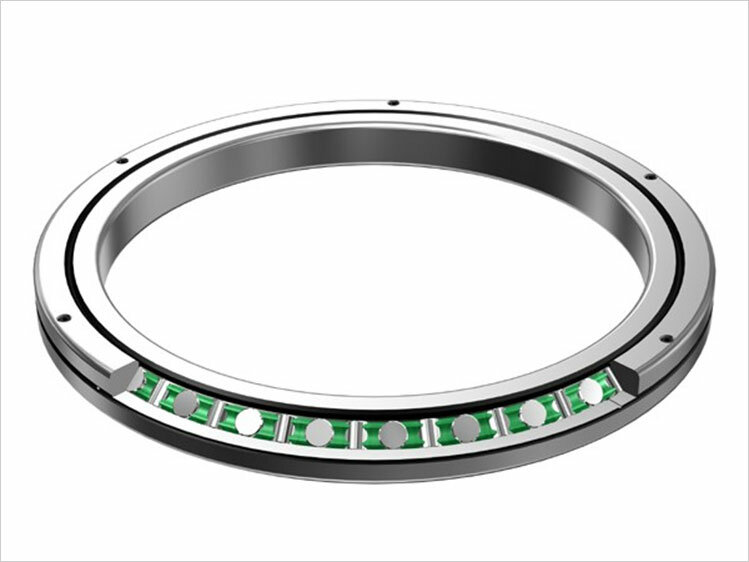
The Structure and Features of the Double-Row Angular Contact Roller Ring Model RW Contribute to High Rigidity and Precision
The Double-Row Angular Contact Roller Ring Model RW was developed to be a rotary bearing as compact as the cross-roller ring with even greater rigidity and accuracy to meet the aforementioned rigidity and accuracy requirements for all rotary components.
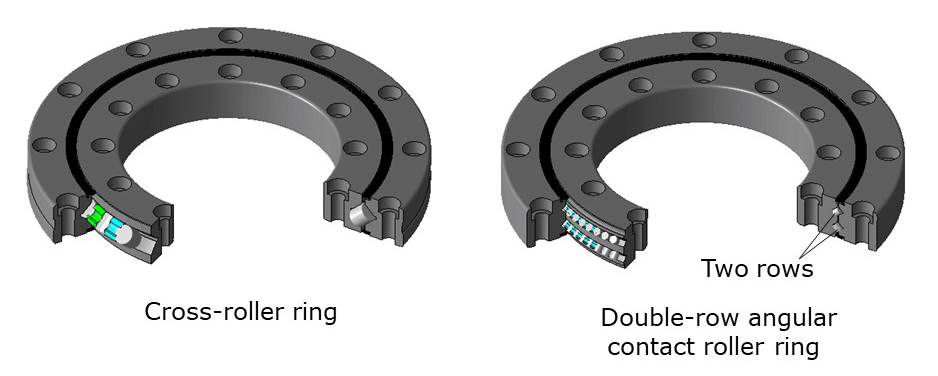
The Double-Row Angular Contact Roller Ring Model RW has two raceway grooves compared to the cross-roller ring's one, and it utilizes a DB structure. It also uses rollers with a smaller diameter, which results in a greater number of rollers and increases the contact surface between the rollers and the raceway. This reduces displacement in relation to the applied load, which decreases the surface pressure between the raceway and rollers. And unlike with cross-roller rings, where either the outer or the inner ring of the raceway ring would come apart in the axial direction, the Model RW features inner and outer rings that are both single pieces with no split. This integrated structure increases rigidity and leads to reduced displacement, even under high loads. It is thanks to this structure that the Double-Row Angular Contact Roller Ring Model RW achieves twice the rigidity of a cross-roller ring with the same dimensions.
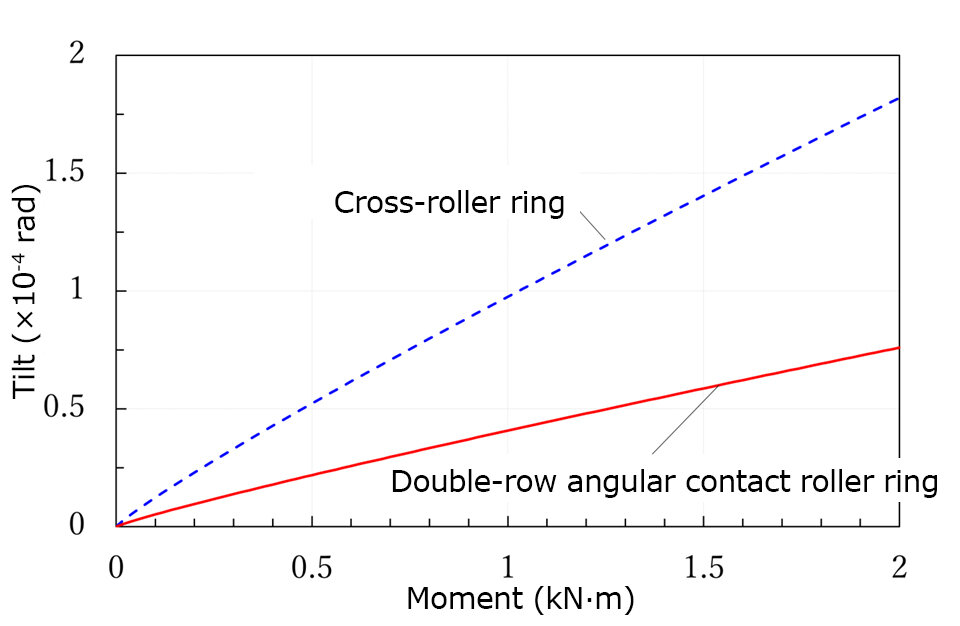
In addition to the rotational accuracy of cross-roller rings, the Double-Row Angular Contact Roller Ring Model RW also has a “wobbling accuracy” specification. This wobbling accuracy is the runout accuracy near the actual position of the workpiece, based on the predicted workpiece machining position above the rotating axis and the measurement position.
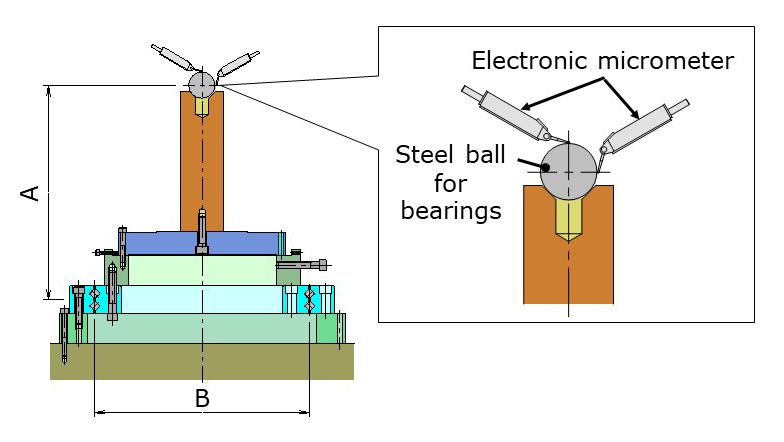
The position for measuring runout accuracy (A) is at a height equal to the roller pitch circle diameter (B). Essentially, if the inner ring of a rotary bearing is spinning while tilted, like a top in precession, positions that are lower along the height of the rotary bearing will be little affected, but the error will be magnified and become greater for those that are higher. Because the Double-Row Angular Contact Roller Ring Model RW has more rollers, the impact of the differences between them is lessened. This improves rotational accuracy and makes wobbling accuracy under 2 μm possible. One could say that the assurance of wobbling accuracy that predicts the workpiece machining position is proof of a highly accurate rotary bearing. It is said that the rotational accuracy of a 5-axis machining center’s rotating axis determines the machine’s accuracy, making rotational accuracy at the machining point a crucial factor of the rotary bearing used on that axis. Wobbling accuracy is an ideal specification for machining centers that boast high accuracy.
Contributing to Higher Speeds
As mentioned above, in the field of machine tools, multitasking machines with added lathing functions have entered the market and seen a rise in demand. Several manufacturers have exhibited multitasking machines with added lathe functions and NC rotary tables with attached lathes. It is against this backdrop of increasing demand to make these machine tools faster that THK developed the High-Speed Double-Row Angular Contact Ring Model BWH.
Structure and Features of the High-Speed Double-Row Angular Contact Ring Model BWH (Ball Type)
High-Speed Performance
The High-Speed Double-Row Angular Contact Ring Model BWH uses balls as its rolling element, which results in a drastically smaller contact surface with the raceway than is seen with the cylindrical rollers employed by cross-roller rings. This in turn makes the difference in circumference relatively smaller between the raceway and the balls. A smaller difference in circumferences makes it possible to suppress temperature increases during high-speed rotation by reducing spin slipping and creating less friction. Additionally, heat generated by friction between the balls is suppressed through the use of an integrated cage. Furthermore, the use of grease with exceptional high-speed performance and low stirring resistance suppresses heat otherwise generated by a grease's stirring resistance. This specialized low-friction structure, as well as the employment of an integrated cage and grease with exceptional high-speed performance, results in a rotary bearing that experiences a rise in temperature of less than 15°C during high-speed rotation at a Dpw·N value of 300,000 with grease lubrication. The Model BWH can also be used with oil air and oil mist systems, which are highly effective at suppressing temperature increases during high-speed rotation, making it possible to rotate continuously at a Dpw·N value of 800,000 if the optimal lubrication method is selected.
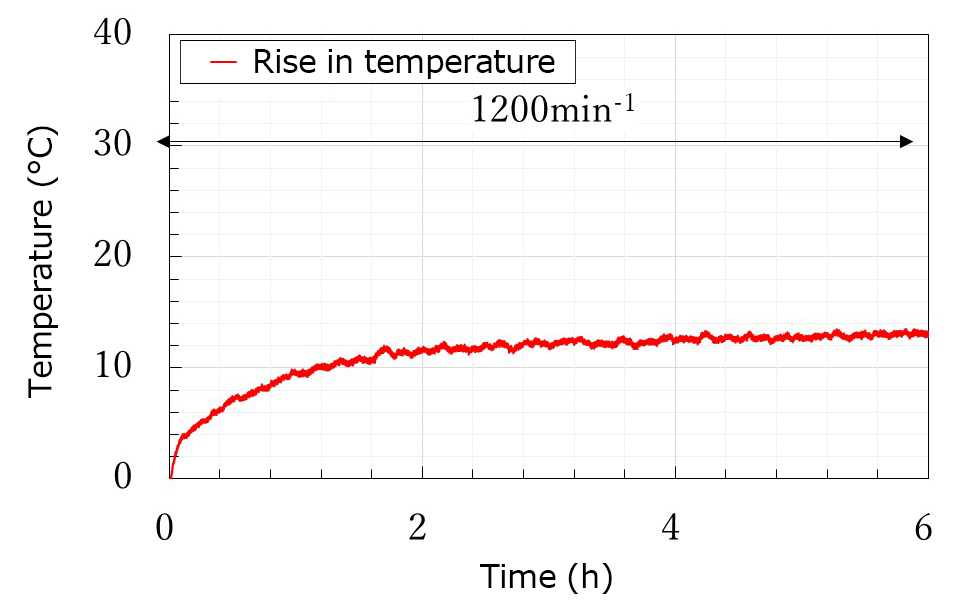
Rigidity
The High-Speed Double-Row Angular Contact Ring Model BWH has two raceway grooves and utilizes a DB structure with a contact angle of 45°. This gives it high moment rigidity and, as with the cross-roller ring, makes it possible for a single rotary bearing to tolerate a radial load, axial load, and moment from all directions. In addition, as with the Double-Row Angular Roller Ring Model RW, the structure of the raceway ring combines the inner and outer rings, increasing rigidity and making it possible to apply a high preload. Because preload is applied to rotary bearings by the insertion of oversized balls, the elastic force of the balls (inner load) will overcome the rigidity of the raceway ring if it isn't sufficiently rigid, and sufficient preload won’t be achieved. This structure and the application of preload make it possible to achieve the same rigidity that cross-roller rings have.
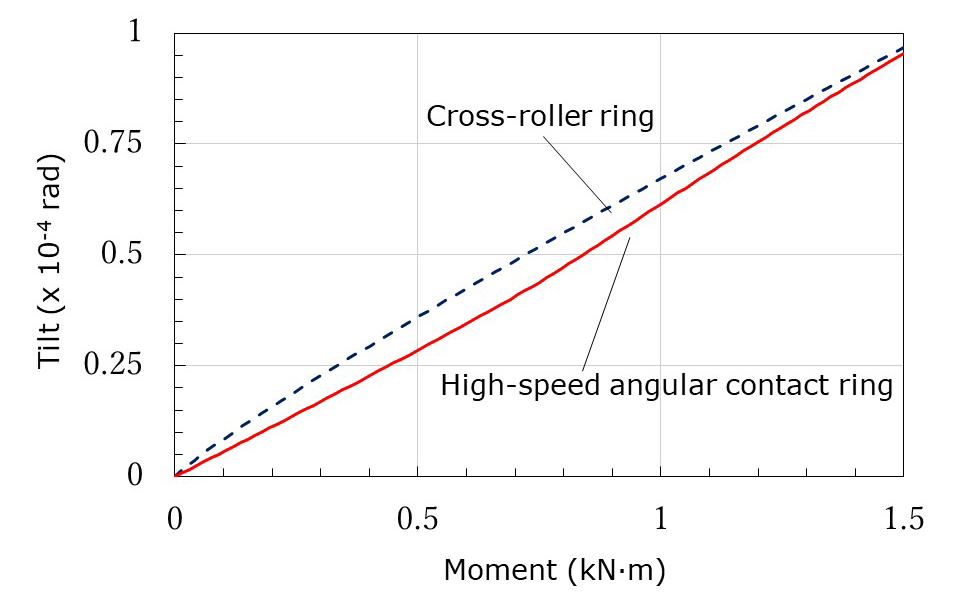
As machine tool manufacturers demand even better high-speed performance and accuracy for increasing machining efficiency and machining accuracy, we will strive to enhance the performance of our products to meet those demands.
Contributing to Higher Speed, Rigidity, and Accuracy in a Wide Range of Industries
In this article, we introduced the technological changes behind our rotary bearing products as they relate to advances in multi-axis multitasking machine tools, what they require from rotary bearings, and responses to those requirements. The High-Speed Double-Row Angular Contact Ring Model BWH, in particular, is a new product that holds the appeal of bringing new value to the market by handling the high-speed rotation sector where the cross-roller ring could not. It is a product that can contribute to greater equipment speed, rigidity, and accuracy in a wide range of industries, even beyond machine tools. We hope this article encourages you to consider the cross-roller ring and all of our rotary bearing products.
View details about double-row angular contact rings (Double-Row Angular Contact Roller Ring Model RW and High-Speed Double-Row Angular Contact Ring Model BWH) (THK website)
Introduction to THK Online Services (THK website)
THK Online Services features technical support tools for the THK product catalog and instruction manuals, CAD data, product FAQ, technical materials, product selection, and service life calculation.
* Those who do not have an ID must register for a free account before using.
* There are two types of members (full members and guest members).
* This content is based on information that was released in Japanese on December 13, 2023.