Mar 20, 2023
Products
THK's Robot Hand: A Behind-the-Scenes Look at Humanoid Robot Development
- Column
- Service Robot
- Robot Hand
- Humanoid Robot
We are getting closer to achieving a world straight out of a movie scene, where people work side by side with humanlike robots as their colleagues. AI is already being employed in the digital realm, while humanoid robots are active in the physical. How did these robots come to exist in the real world? Let’s take a look behind the scenes of their development.
Development of Humanoid Robots
Even from a young age, many people have been fascinated by robots and wanted to operate one. Maybe some have even had grand dreams of designing a humanoid robot.
If you break the human form down into its components, it consists of the following features:
- Bones to form a sturdy skeleton
- Muscles to exert power
- Blood to deliver energy
- A brain that acts as the control tower
- Nerves to give commands and feedback
- Sensory organs to judge aspects of one’s environment
- Organs that take in external energy and convert it into internal energy
The development of humanoid robots is basically the act of replacing the human form with machinery. However, this is easier said than done. To make this possible, you first need a deep understanding of the human form and its functions.
- How is a skeleton put together?
- How many degrees of freedom do connecting joints have?
- How are signals from the sensory organs processed?
The more you know, the more you become perplexed at the vastness of it all. How can so many functions be crammed into such a limited space?
Imitating Function, Not Form
The childhood dream of developing humanoid robots will remain only a dream if you take a regular approach. You'll suffer setbacks if you attempt to exactly replicate the human form with machinery. However, there are two approaches to mechanization. One method replaces the human form as it is, and the other method achieves the abstracted functions without regard for form.
As an example, let’s take a look at the development of the robot hand. Over time, humanity evolved hands to perform various actions such as gripping and carrying, and they feature the following:
- Extremely complex and delicate motion
- The ability to detect slight surface unevenness and temperature changes
- Fine-tuned ability to sense movement
If you consider these inputs/outputs and functions of a hand without trying to imitate its form, you can achieve a simpler structure.
Do Humanoid Robots Need Five Fingers?
The humanoid robot is modeled after humans. If the end goal is to make a robot look like a human, then it will need five fingers. But if the goal is for the robot to take the place of a human, does it need that same number? If the robot is taking over a task, does it need to have the same kind of hand as a person? Human hands have over 20 degrees of freedom, so it would be extremely difficult just to build in enough actuators to control that movement at the same size of a hand. There are even more joints, so in addition to all of those mechanisms, you also need more motors, actuators, sensors, and wiring.
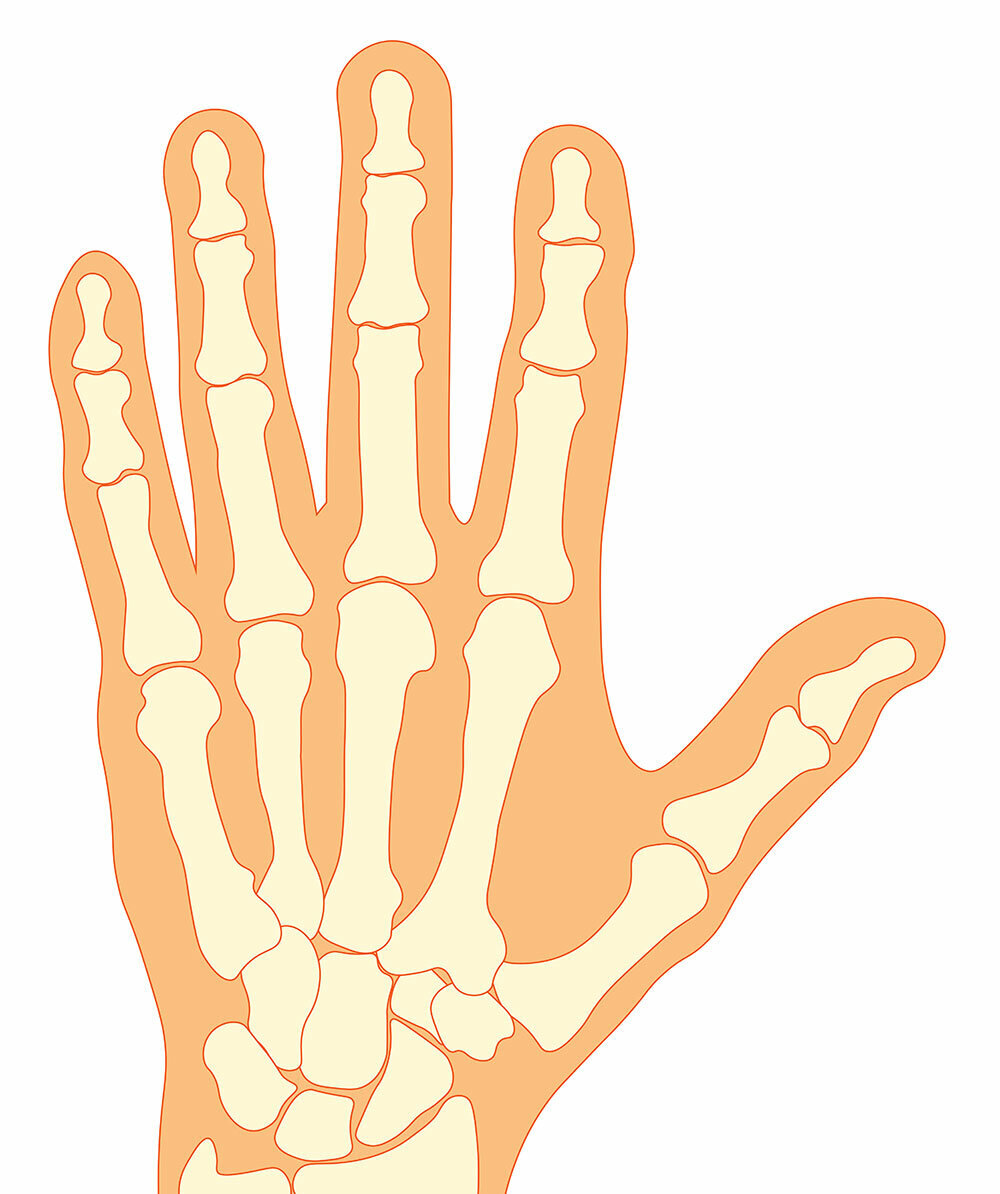
Aiming for the Smallest Structure Possible
One Motor
In trying to achieve the smallest structure possible, the challenge lies in how much you're able to simplify the human hand's functions of gripping, grasping, and pinching. To that end, it’s preferable to have one motor. Any more than that, and the size will go up. You'll also need more power and may run into problems with heat generation. That's why we aim to use one motor when trying to achieve the smallest structure possible.
Three Fingers
What is the fewest number of fingers you can have? If you consider only the act of grasping, just two fingers would be enough to do the job. However, workpieces come in many shapes, and they need to be grasped securely when being moved. To continue grasping various shapes securely, you need to have at least one additional finger. That's why there has to be three fingers even in the smallest structure.
Three Fingers per Motor
Even if there are three fingers, if those fingers are of a fixed shape like a three-jaw chuck, they cannot match their grip to the workpiece. That’s why a link mechanism is required to perform an articulated wrapping motion like human fingers. In addition, because there’s only one motor, the included link mechanism needs to cause the finger joints to bend during the stroke when power from the single motor actuates the three fingers. In order to achieve this complicated yet simple structure that converts one motor's rotation into linear motion and distributes that stroke through a link mechanism, the motor is also mounted using the trunnion structure that bears part of the link mechanism.
Adopting a SEED Actuator
Even if you are able to make the robot hand as small as possible, it means nothing if the control box is big. The SEED actuators developed by THK can be operated with SEED Driver, which is a compact modular motor driver that is only 20 mm square, so even the control system can be built into the hand unit.
Simple Controls
Ordinarily, the ability to grip and pinch various shapes would require complex controls. With SEED actuators, these functions can be achieved with a simple ON/OFF system.
- ON causes the hand to start closing.
- When the fingers touch the workpiece, the command value will deviate from the actual movement.
- When that happens, the close operation is stopped.
- After that, it automatically transitions into grip mode, where it performs a close operation at each pulse.
Regardless of the workpiece shape, both gripping and pinching operations can be completed with a simple ON/OFF command.
The Birth of the General-Purpose Gripper TRX
This is how we arrived at the General-Purpose Gripper TRX, which is a highly compact universal gripper with one motor, three fingers with a link mechanism, and an integrated controller. Thanks to control provided by the SEED Driver, it only requires a power supply to run, with no need for a separate driver.
This concludes our case study of the development of the robot hand.
In these product blogs, we will continue to share more information through the lens of our products.
Inquire about the General-Purpose Gripper TRX (THK website)
* This content is based on information that was released in Japanese on March 20, 2023.