Accessories for Lubrication
We offer a full line of accessories for lubrication to maintain good lubrication.
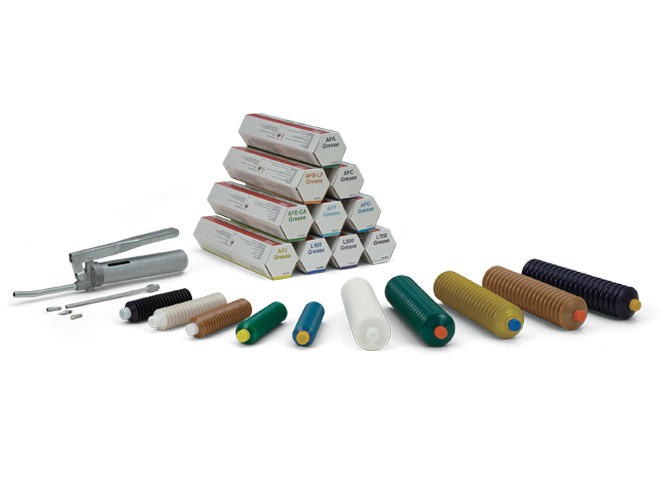
Types
Search products by various conditions
Features
Lubrication
To optimize an LM system’s functionality, it is necessary to provide lubrication according to the usage conditions. Use without lubrication may increase wear on the rolling elements and shorten the service life.
Lubrication has the following effects:
- Minimizes friction between moving elements to prevent seizure and reduce wear
- Forms an oil film on the raceway to decrease stress acting on the surface and extend rolling fatigue life
- Covers metal surfaces with an oil film to prevent the formation of rust
Even when the LM system has seals, the internal lubricant gradually seeps out during operation.Therefore, the system needs to be lubricated at an appropriate interval according to the usage conditions.
Types of Lubricants
LM systems mainly use grease or sliding surface oil for their lubricants.
The requirements that lubricants need to satisfy generally consist of the following:
- Extreme pressure resistance
- Reduce friction
- High wear resistance
- High thermal stability
- Excellent rust-proofi ng performance
- Excellent fluidity
- Consistency of grease must not vary significantly even with repeated stirring
Grease Lubrication
Greasing intervals vary depending on the usage environment and conditions. For normal use, we recommend greasing the system approximately every 100 km of travel distance (3 to 6 months).
When replenishing grease through the LM system’s grease nipple and greasing hole, use grease of the same type. Mixing different types of grease may hinder the system’s performance.
Lubricant |
Type |
Brand name |
|
Grease |
Lithium-based grease |
AFA Grease |
see Products Page |
---|---|---|---|
Shell Alvania Grease S (Showa Shell Sekiyu) |
* The recommended grease will vary according to the usage conditions and environment.
Oil Lubrication
Lubricant |
Type |
Brand name |
Oil |
Sliding surface oil or turbine oil |
Daphne Super Multi Oil (Idemitsu) |
---|
- The amount of oil to be supplied varies with stroke length. For a long stroke, increase the lubrication frequency or the amount of oil applied so that an oil film is able to form along the raceway to the end of the stroke.
- In environments where liquid coolant may spatter, the lubricant may become mixed with the coolant. This could result in the lubricant being emulsified or washed away, causing significantly decreased lubrication performance. In such settings, apply a lubricant with high viscosity (kinematic viscosity: approx. 68 mm2/s) and high emulsification resistance, and adjust the lubrication frequency or the amount of feed lubricant.
For machine tools and similar devices that are subject to heavy loads, require high rigidity, and operate at high speed, oil lubrication is recommended. - Use only after making sure that the lubrication oil discharges normally from the ends of the lubrication piping, i.e., the oiling ports that connect to your LM system.
Product Selection According to Usage Environment
When using the product in locations exposed to constant vibrations or under special circumstances such as in clean rooms, vacuums, and low/high temperatures, it may not be possible to use standard grease. In such cases, THK will recommend the optimal lubricant. Please contact THK for details.
Usage environment/ |
Lubrication |
THK product |
---|---|---|
Environments with spattering coolant |
To stop the coolant from causing emulsification, use grease that does not easily wash away. Use grease with extreme pressure and rust-proofing performance. * In environments where water-soluble coolants may spatter, there are occasions where certain types of coolant may cause emulsification or cause the grease to wash away, even if using medium-viscosity lubricant.This, in turn, may then reduce lubricity and prevent a proper oil film from forming. Check the compatibility between the lubricant and coolant. ● Daphne Super Multi Oil (Idemitsu) ● Mobil Vactra Oil No. 2 SLC (Exxon Mobil) |
- Please note that applying coolant directly to THK products may have an adverse effect on components/parts made of resin, rubber, etc. - Consider using designs where coolant cannot come into direct contact with THK products (consider using covers or bellows). - Consider using some of the various dust-proofing options available in order to prevent coolant from getting inside THK products. |
High-temperature |
- Please note that the higher the temperature, the greater the risk of the grease separating and the lubrication performance dropping. |
- Contact THK for a range of high-temperature specification products. |
Clean room |
- THK also offers a range of clean room-compatible grease products. ● AFE-CA Grease (THK) ● AFF Grease (THK) ● L100 Grease (THK) |
- Two reasons for the generation of dust are metal-to-metal contact and mutual friction between rolling elements. THK offers a range of products with a cage for minimizing metal-to-metal contact and mutual friction between the rolling elements. Furthermore, the cage is also structured in a way that maintains the lubricity, making it suitable for use in clean rooms. - Anti-rust oil is applied as standard, so please specify if it is not required. |
Vacuum |
- Use fluorinated lubricants for vacuums (vapor pressure varies by brand). - Using vacuum grease will make it more likely that the oil film will break due to its low extreme pressure resistance compared to general industrial grease. Be sure that there is a reliable feeding of oil to the raceways (by increasing the number of relubrications, etc.) in order to ensure that the oil film does not break. * If using vacuum greases, please note that some brands have starting resistances several times greater than general-purpose grease. |
- Please note that under vacuum environments, there is a risk that gas given off by resin and rubber materials may cause the vacuum level to decrease. - Please consider using stainless steel or surfacetreated products as a rust-proofing measure. |
High-speed |
- Use a lubricant with a low base oil kinematic viscosity to prevent heat generated by resistance from the lubricant. - THK offers a range of grease products with excellent high-speed specifications. ● AFA Grease (THK) ● AFG Grease (THK) ● AFJ Grease (THK) |
- Metal-to-metal contact and mutual friction between the rolling elements inside products may produce noise and quickly lead to damage. - THK offers a range of caged products with excellent high-speed and noise-dampening properties. |
Environments |
- Use grease with high water-proofing properties. - Use a lubricant with high extreme pressure resistance that does not easily wash away. ● L700 Grease (THK) - Contact THK for instructions regarding lubricating in and around water. |
- Consider using designs where water cannot come into contact with THK products. (Consider using bellows or covers.) - Consider using stainless steel or surface-treated products as a rust-proofing measure. - Consider using some of the various dust-proofing options available in order to prevent water from getting inside the product. |
Food machinery |
- Consider using grease that is made for food processing and that is safe for people. ● L700 Grease (THK) (NSF H1 standard accredited) |
- Consider using covers if there is the possibility of lubricant spattering. |
Micro-vibration |
- THK offers a range of grease products that work particularly well under micro-vibrations. ● AFC Grease (THK) ● AFJ Grease (THK) |
- Oil films formed at the points of contact between the rolling elements and raceway are likely to break in environments with micro-vibrations. - By periodically overstroking, the lubricant will form an oil film at the points of contact between the rolling elements and raceway. |
Lubrication Methods
There are three methods of lubricating LM systems: manual greasing using a grease gun or manual pump, forced greasing with the aid of an automatic pump, and oil-bath lubrication.
To achieve efficient lubrication, it is necessary to mount the grease nipple or the plumbing fixture according to the mounting orientation.
We also stock grease guns, grease nipples, and plumbing fixtures.
(If using the product in any orientation other than horizontal, be sure to let THK know the mounting orientation and the exact position in each LM block where the grease nipple or the plumbing fixture should be attached. For the mounting orientation of the LM Guide, see Conditions of the LM Guide.)
Manual Lubrication
Generally, grease is replenished periodically and fed through the grease nipple provided on the LM system using a grease gun. ( Fig.1 )
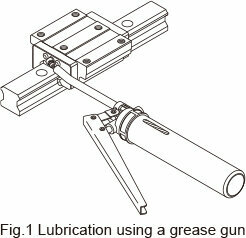
Forced Lubrication Method
With this method, a given amount of lubricant is forcibly fed at a given interval. ( Fig.2 )
Although a special lubrication system using piping or the like needs to be designed, this method reduces the likelihood of forgetting to replenish lubricant.
Use only after making sure that the lubrication oil discharges normally from the ends of the lubrication piping, i.e., the oiling ports that connect to your LM system.
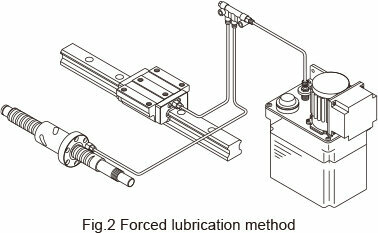
Lubrication Accessory Series for LM Systems
THK provides a wide array of lubrication accessories such as grease, grease guns, grease nipples and plumbing fixtures available for various applications.
THK Original Grease
THK provides various types of THK original grease needed for the lubrication of LM systems. They are available for various conditions and environments.
Table for Grease Selection
Name of grease |
AFA |
AFB-LF |
AFC |
AFE-CA |
AFF |
AFG |
|
---|---|---|---|---|---|---|---|
Features |
Low sliding friction |
All-purpose type |
For fretting and |
For clean |
For clean environments |
For preventing heat generation by ball screws |
|
Base oil |
High-grade synthetic oil |
Refined mineral oil |
High-grade synthetic oil |
High-grade synthetic oil |
High-grade synthetic oil |
High-grade synthetic oil |
|
Consistency enhancer |
Urea-based |
Lithium-based |
Urea-based |
Urea-based |
Lithium-based |
Urea-based |
|
Features |
Low sliding friction |
○ |
- |
- |
- |
- |
○ |
Micro-vibration |
○ |
- |
○ |
- |
○ |
○ |
|
High load |
- |
○ |
- |
- |
- |
- |
|
Low dust generation (Clean environments) |
- |
- |
- |
◎ |
○ |
- |
|
Water resistance |
○ |
○ |
- |
- |
- |
○ |
|
Machine stability |
- |
○ |
○ |
○ |
○ |
- |
|
Bellows cartridge color |
Clear |
Light green |
Clear |
White |
Dark blue |
Light green |
|
Cap color |
White |
Yellow |
Orange |
White |
White |
Orange |
|
Reference page |
Name of grease |
AFJ |
L100 |
L500 |
L700 |
|
---|---|---|---|---|---|
Features |
For a wide range of speeds |
For clean environments/ High loads |
For high-load ball screws |
For medical, pharmaceutical, and food equipment |
|
Base oil |
Refined mineral oil |
High-grade synthetic oil |
Refined mineral oil |
High-grade synthetic oil |
|
Consistency enhancer |
Urea-based |
Lithium |
Lithium |
Calcium |
|
Features |
Low sliding friction |
○ |
- |
- |
- |
Micro-vibration |
○ |
- |
- |
- |
|
High load |
○ |
◎ |
◎ |
○ |
|
Low dust generation (Clean environments) |
- |
○ |
- |
- |
|
Water resistance |
- |
- |
- |
◎ |
|
Machine stability |
○ |
○ |
○ |
○ |
|
Bellows cartridge color |
Yellow |
Blue |
Purple |
White |
|
Cap color |
Blue |
Yellow |
Yellow |
White |
|
Reference page |