Jan 24, 2024
Products
Optimize Overall Equipment Effectiveness (OEE)! New AI Diagnostic Service ADV
- Machine Tools
- Industrial Robots
- Precision Machinery / Instrument
- Electricity / Electronics
- Semiconductor Manufacturing Equipment
- Automotive and Transportation Equipment
- Automotive / Automotive Component
- Conveyance
- Other Machinery
- OMNIedge
- AI Diagnostic Service ADV
- Overall Equipment Effectiveness (OEE)
The last few years have seen an acceleration in the evolution of AI (artificial intelligence) and the IoT (Internet of Things) for the manufacturing industry. Whereas veteran technicians applied years of experience and intuition to machine maintenance in the past, the quantification of running conditions for various machines has now made it so that AI can analyze that data and enhance the efficiency of maintenance operations.
In this article, we’ll be introducing THK’s IoT solution for improving the efficiency of maintenance operations and the newly added AI diagnostic service ADV.
* OEE (overall equipment effectiveness): A methodology proposed by the Japan Institute of Plant Maintenance.
THK has now launched the AI Diagnostic Service ADV for linear motion components in its OMNIedge OEE optimization system.
OEE Optimization System OMNIedge
As a machine component manufacturer, THK has been using its digital capabilities to offer an IoT solution for reducing various types of loss on the production floor since 2020. That solution is the OEE optimization system OMNIedge.
The first version of OMNIedge launched the service for linear motion components such as the LM Guide and ball screws. Version 2 expanded the range of the service to include rotary components like pumps, fans, and gear boxes, and saw the release of predictive failure detection for components. And AI tool monitoring to reduce losses from tool replacement and machining defects was developed in Version 3 for customers that use processing machines.
In order to improve OEE, losses on the production floor related to equipment, personnel, and energy use must be reduced. THK will thus continue to present solutions to these three types of loss going forward.
Visualizing Equipment Status with OMNIedge
THK has been selling machine components like its mainstay LM Guide for the last 50 years, and these have been used by a vast array of customers. Owing to the special features of these linear motion components, they are often used in hard-to-reach places inside equipment or underneath covers. Machine users talk about various maintenance methods like regular lubrication and regular part replacement based on travel distance, but even the LM Guide, which rarely breaks down, can be damaged under extreme loads, causing unplanned downtime. Precisely because the LM Guide breaks down so rarely, many customers have asked for a way to visualize (quantify) part status on a daily basis.
In response, starting January 2020, THK started offering a solution that could visualize part status using sensors retrofitted onto all types of existing equipment and support more efficient maintenance activities.
Retrofit onto Equipment Parts and Use Immediately
If a machine user is new to IoT construction, they have to follow steps like those shown in the diagram. They could purchase general purpose sensors and construct it themselves, but the reality is that they are often too busy to be able to get around to it. To remedy this, THK’s OMNIedge offers a single package that customers can use right away because it eliminates the time it takes to select sensors and edge computers, and it includes scoring for collected data, network construction, and a web application for display monitors.
Because the LM Guide and other linear motion components are built into countless machines currently in operation around the world, this system was made retrofittable onto existing equipment. The one-touch detachable type and adhesive type are offered as attachments that customers can set up themselves.
On the network side, it takes a lot of work to set up internal network connections and clear network security, so one highlight of the OMNIedge service is that is you can get started easily with a secure 4G LTE environment during the proof-of-concept stage.
In addition to offering OMNIedge as a single package, THK also has multiple pricing plans that it can propose to match customer needs. Plans that reduce initial costs using an ongoing subscription model or involve purchasing hardware first are among those available for customers to select depending on their project and the scope of the installation.
Development Details and Benefits of the Simple-Setup AI Diagnostic Service ADV
While the methods mentioned above make it possible to visualize (quantify) the status of machine components, we heard from customers that operational patterns vary by each piece of equipment, so it’s difficult to set thresholds, and OMNIedge is easy to use, so they’ve expanded its implementation to many pieces of equipment, but now there are so many pieces of equipment registered that they can’t manage them all. In response, we developed the AI Diagnostic Service ADV for OMNIedge. Utilizing AI, it eliminates the need to set thresholds and automatically issues data analysis and monitoring reports while sending automated notifications of changes and abnormalities. The ADV* system uses THK’s proprietary AI algorithm to analyze data in the cloud and automatically sends an alert if it detects an irregularity.
The system calculates an AI score rating the degree of abnormality that captures factors such as damage and lubrication conditions. This vastly improves the efficiency of maintenance operations by removing the need for customers to manage each piece of equipment individually and by making it possible to perform maintenance activities that consist of no more than checking a device and the area of the components and performing replacements when an alert is received. Another thing we often hear is that even regular maintenance is sometimes performed too late as the number of machines that maintenance personnel are responsible for has been increasing recently. Under such conditions, OMNIedge is also useful as a way to expand the range of machine statuses that can be kept track of. Because this service is already included in the OMNIedge contract, no additional contract is required.
* ADV is a term that combines the meanings of phrases like “AI advisor,” “AI-driven,” and “Advanced solution.”
AI Diagnostic Service ADV
- No threshold setting required
- Automatic change and abnormality notifications
- Data scientists who are familiar with linear motion parts analyze and monitor data and report on it
Even when using predictive detection, many users are concerned about threshold settings because the status and conditions of each machine are different. That's where the AI Diagnostic Service ADV comes in.
With ADV, there is no need to set thresholds. An AI algorithm calculates the abnormality (damage/lubrication condition) score, and experts analyze the data and provide a monitoring report.
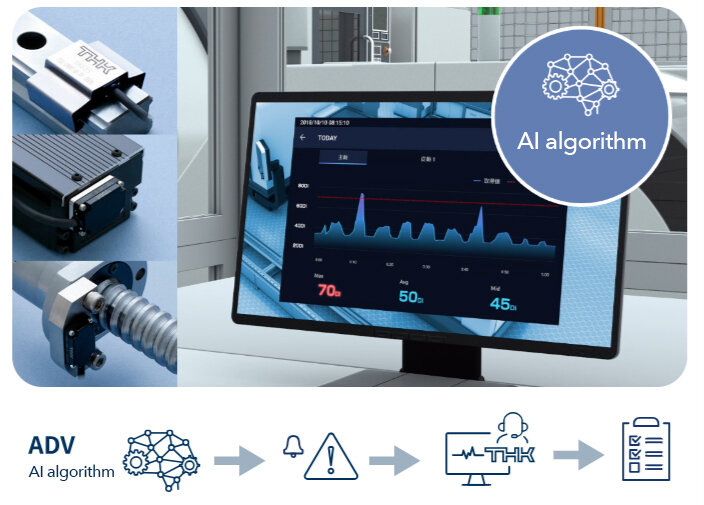
Customers Who Should Consider Implementation
This service is designed for customers who use machines with built-in linear components and linear guides such as the LM Guide, ball screws, and actuators. It is particularly suited to customers who struggle with existing maintenance methods and those who have experienced extended downtime with high-load applications such as machine tools and high-repetition, high-utilization applications like transfer devices. Digital technology is used to quantify what was previously decided using experience and intuition in addition to eliminating situations where only certain individuals possess relevant knowledge. Additionally, in light of recent labor shortages caused in party by the retirement of veteran employees, this solution also functions to eliminate the common pitfall of gaps in knowledge transmission.
If you've struggled with linear components or had a problem occur in the past, please reach out to us.
Now Offering OMNIedge AI Diagnostic Service (ADV) for Linear Motion Components (News release)
* This content is based on information that was released in Japanese on January 24, 2024.