Selecting a Spline Nut
Dynamic Permissible Torque T
The permissible dynamic torque (T) is the torque at which the contact surface pressure on the bearing tooth surface is 9.8N/mm2. These values are used as a reference for the strength of the spline nut.
pV Value
With a sliding bearing, a pV value, which is the product of the contact surface pressure (p) and the sliding speed (V), is used as a measuring stick to judge whether the assumed model can be used. Use the corresponding pV value indicated in Fig.1 as a guide for selecting a spline nut. The pV value also varies according to the lubrication conditions.
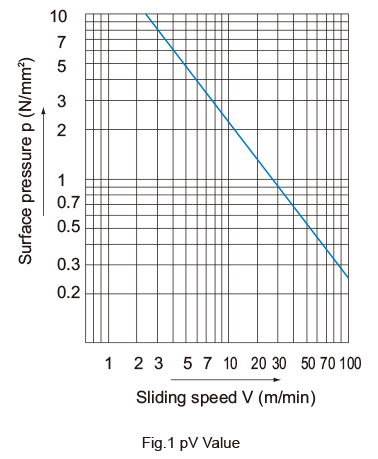
fS : Safety Factor
To calculate a load applied to the spline nut, it is necessary to accurately obtain the effect of the inertia that changes with the weight and dynamic speed of an object. In general, with reciprocating or rotating machines, it is not easy to accurately obtain all the factors such as the effect of the start and stop, which are always repeated. Therefore, if the actual load cannot be obtained, it is necessary to select a bearing while taking into account the empirically obtained safety factors (fS) shown in Table1.
Type of load | Lower limit of fS |
---|---|
For a static load less frequently used | 1 to 2 |
For an ordinary single-directional load | 2 to 3 |
For a load accompanied by vibrations/impact | 4 or greater |
fT:Temperature Factor
If the temperature of the spline nut exceeds the normal temperature range, the seizure resistance of the nut and the strength of the material will decrease. Therefore, it is necessary to multiply the dynamic permissible torque (T) by the corresponding temperature factor indicated in Fig.2 .
Accordingly, when selecting a spline nut, the following equations need to be met in terms of its strength.
Dynamic permissible torque (T)

fS | Static safety factor (see Table1) |
---|---|
fT | Temperature factor (see Fig.2) |
T | Dynamic permissible torque (N・m) |
PT | Applied torque (N・m) |
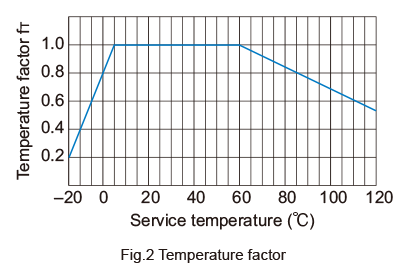
Hardness of the Surface and Wear Resistance
The hardness of the shaft significantly affects the wear resistance of the spline nut. If the hardness is equal to or less than 250 HV, the abrasion loss increases as indicated in Fig.3 .The roughness of the surface should preferably be Ra0.80 or less.
A specially rolled shaft achieves surface hardness of 250 HV or greater, through hardening as a result of rolling, and a surface roughness of Ra0.20 or less. Thus, the dedicated rolled shaft is highly wear resistant.
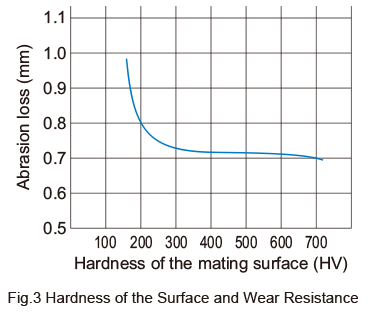
Calculating the Contact Surface Pressure p

p | Contact surface pressure on the tooth under a load torque (PT) (N/mm2) |
---|---|
T | Dynamic permissible torque (N・m) |
PT | Applied torque (N・m) |
Calculating the Sliding Speed V
With splines, the sliding speed of the tooth surface is equal to the feeding speed.
V | Sliding speed of the tooth (m/min) |
---|