- Workpiece
- Issue resolution
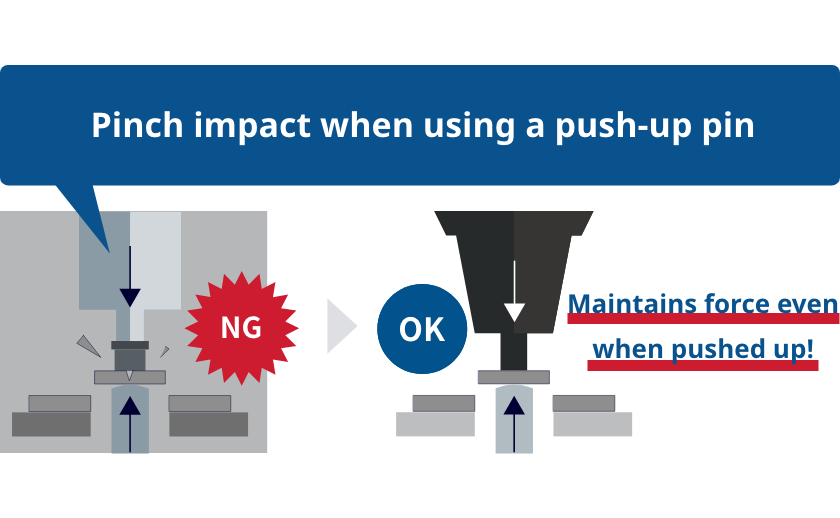
Introduction
In this article, we will introduce an inquiry we have received from a customer on the topic of how the PPR can help them solve their issues.
Here is the inquiry we received:
"We have a process where a workpiece is pushed up from below. Is it possible to synchronize the shaft with the push-up pin?"
What Is Chip Push-Up?
We receive many inquiries like this from people in the semiconductor industry. The semiconductor manufacturing process includes front-end and back-end processes. The back-end process involves dicing (cutting the wafer into chips) and retrieving the chips.
Let us explain this process in more detail.
(1) When dicing, the wafer is attached with adhesive tape.
(2) Dicing is performed.
(3) After dicing, adhesive tape is stretched to open up the space between chips.
(4) The chip to be retrieved is pushed up with the push-up pin to make it easier to remove from the tape.
(5) Using pick-up tools (like the PPR), it is sucked up and pull off.
Here, to stably pick up a chip, steps 4 and 5 are performed simultaneously, and while the suction nozzle is contacting the workpiece, the push-up is performed from below to make it easier to retrieve. This is the operation the customer would like to do.
What becomes an issue is that the push-up pin and the nozzle pinch the workpiece during push-up, which may cause an impact to the delicate workpiece, possibly damaging it.
Now, how can the PPR solve this problem?
Proposed Solution Using the PPR's Functions
Here is the answer.
The PPR has an integrated force sensor, which enables force control with feedback control of the force sensor. Force control maintains a constant load on the workpiece. For example, even when it is pushed up by a push-up pin, the PPR automatically raises the shaft to relieve the forces generated by the pinching.
Moreover, the PPR can monitor the position and force sensor values, so the distance the workpiece is actually pushed up and the change in force during the push-up can also be confirmed.
By conducting a simple experiment to see how this behaves in practice, we were able to obtain this kind of waveform data.
These are the waveforms of the Z axis present position and force sensor when the shaft is moved up and down by hand with 0.5 N maintained by the force control. It is clear that there is almost no change in the pushing force with respect to the position change.
We also have a video showing the actual experiment, which we will also share.
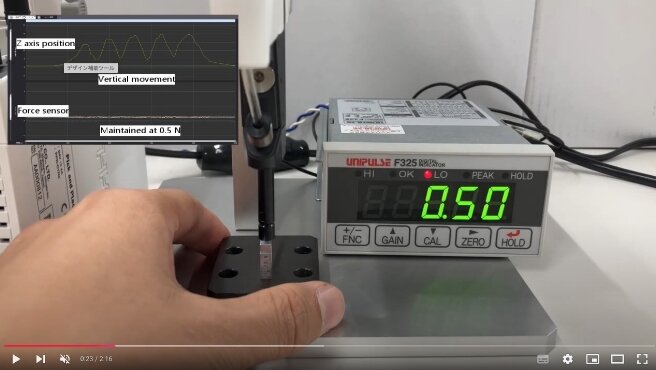
Concrete Sequence Example to Achieve Synchronization of Push-Up Operation
How should one go about assembling the PPR's sequence?
When raising a workpiece with a push-up pin, it is necessary to have force control status active.
So, as one example, we can propose the following:
Sequence 1: Contact the workpiece and activate force control status. Open the vacuum valve and carry workpiece up to the suction judgment.
* If force control status is still active at the completion of the sequence, the status will be maintained until the next instruction.
2. Push-up by a push-up pin.
3. Sequence 2: Ascend.
For detailed sequence settings and ideas for operation, please feel free to contact us, and we will be happy to create a sample sequence for you.
We hope that this article will be of some help for your process improvements.