- Pick and Place
- System
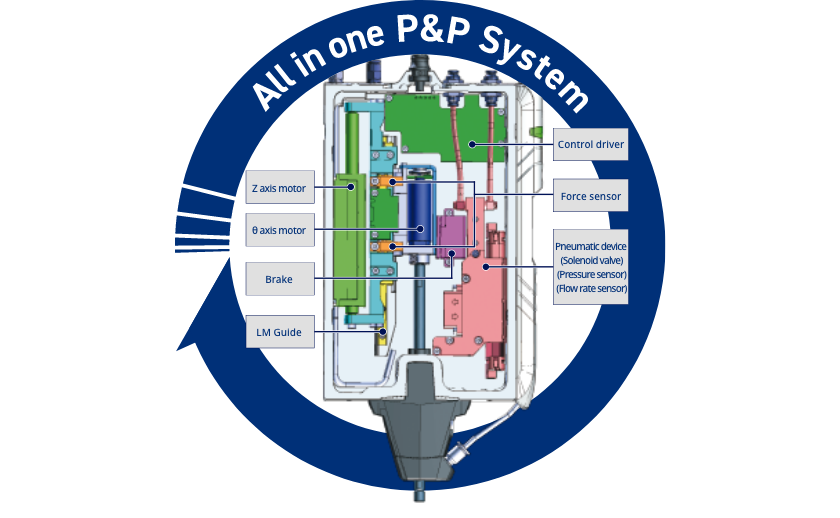
Introduction
The concept behind the Pick and Place Robot (PPR) is to put the required components for the pick and place process all in one device.
In this article, we would like to introduce a part of how we created the product called the "PPR." We hope you will see some of the benefits of the PPR that have not been shared until now.
What are the Required Components of the Pick and Place Process?
Now, what are the required components of the pick and place process?
Approach to workpieces: Lowering the Z axis. A drive source for lifting and lowering is required. Due to the precise raising and lowering, a guiding system is also required.
Contact with workpieces: Since the workpiece may be damaged by impact made upon contact, a system or device to limit the impact is required.
Workpiece suction: When picking with air, a nozzle that contacts the workpiece and a piping route for the air to the nozzle are required. A solenoid valve is required for suction and vacuum breakage. Having a pressure sensor to confirm that suction is complete would also be preferable.
Lifting the workpieces: This should be covered by the first lifting axis.
Alignment adjustments: A rotary axis is required. Depending on the degree of precision required at the time of placement, precise angular adjustment may be required.
Control: A controller to control all of the above operations is required.
Example of System Configuration for a Customer's In-house Production
As a result of our interviews at our clients' sites, we found that many sites were using pick and place tools assembled by the client on their own. For example, there are cases like the following:
- Ball screw actuator on the Z axis. Rotary motor on the θ axis.
- A control driver is required for each axis, and the operation is controlled by a PLC.
- To mitigate impact, a spring buffer or similar material is used in the nozzle.
- Air piping is piped either to the hollow shaft of the θ motor or directly piped to the end of the shaft.
- Pneumatic devices use external solenoid valves and pressure sensors, and they are controlled by a PLC.
Simply listing them all in this way involves a great many components.
To assemble and bring a product to completion from scratch, a great deal of time is required, including conceptual design, component selection, component management, assembly, programming, and final adjustments.
System Components That Are Integrated in the PPR
The PPR is....
- Linear motor on the Z axis. Rotary motor on the θ axis.
- Control of each axis is performed by an integrated control board.
- Integrated force sensor enables feedback control of the force sensor to mitigate impact.
- Integrated solenoid valve, pressure sensor, and flow rate sensor. Air piping is also integrated and runs through to a hollow hole in the output shaft.
- Control of the pneumatic devices is also performed by an integrated control board, enabling autonomous pick and place operations.
As an all-in-one system, the PPR greatly reduces the time and effort required to perform these tasks, making it very easy for both the device manufacturer and the user of the device.
Details of the PPR's internal structure are explained in the "Product Journal" section of our website. Please check that out as well.