Built-in force sensor facilitates easy quality stabilization
The World's First* Process-Optimizing Robot
Linear rotary actuators with high precision force control
Pick and Place Robot
PPR
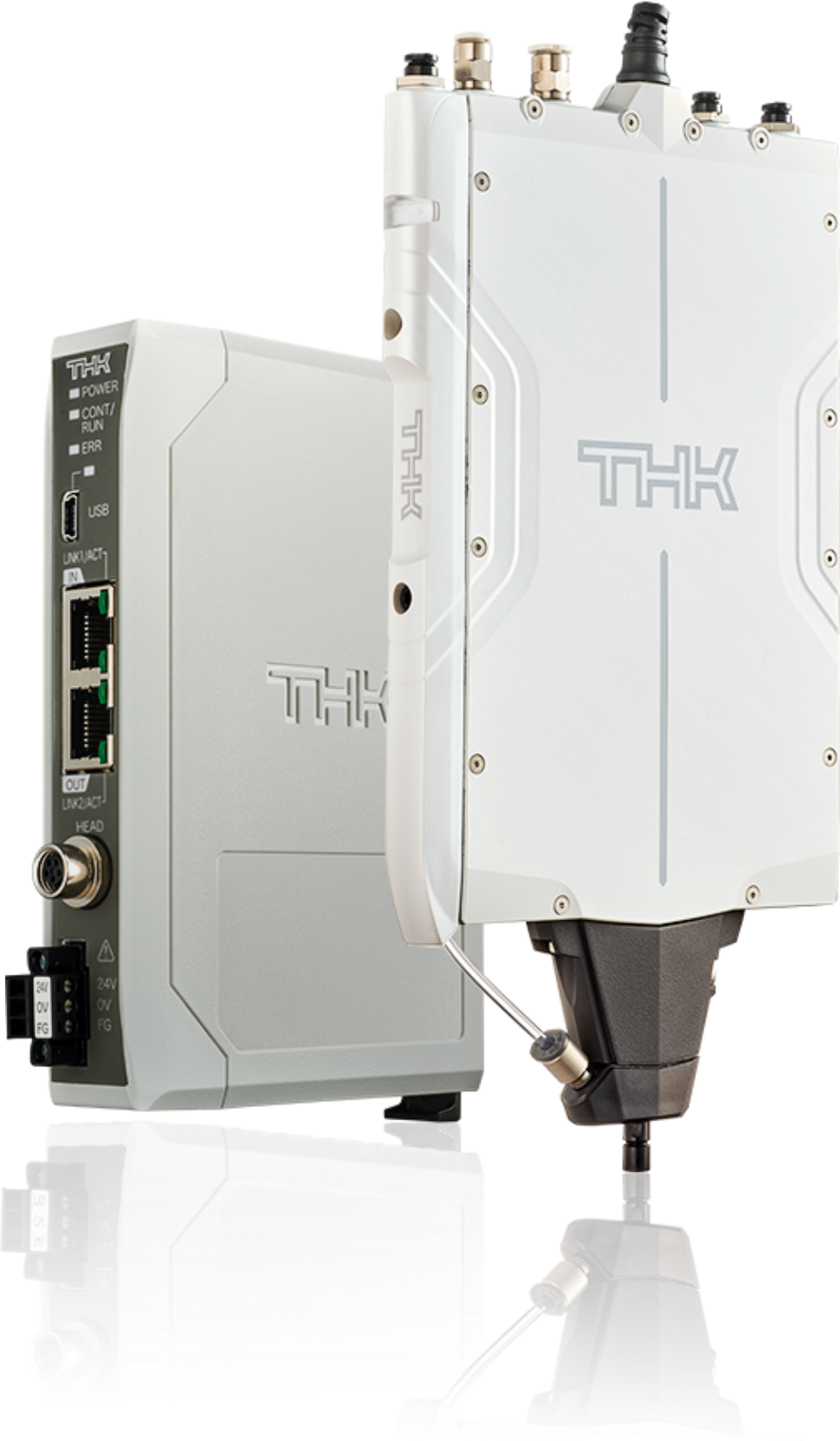
- First in the world as a process-optimizing robot specialized for pick and place processes with an integrated force sensor, motor, pneumatic device, and control circuit board.
All in One P&P System
Equipment becomes too large to maintain cycle time due to many devices being mounted.
Thin, lightweight all-in-one design
Achieves high-speed pick and place with easy installation and minimal wiring
Control and Visualization of Position and Force
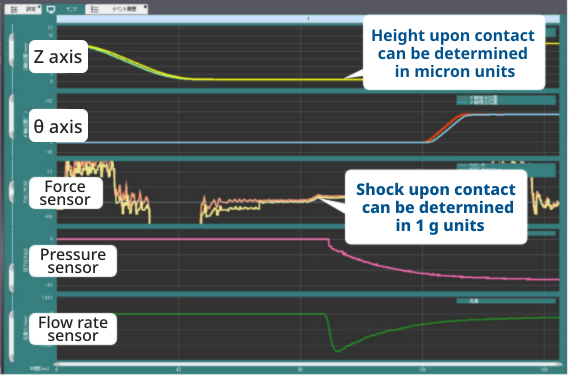
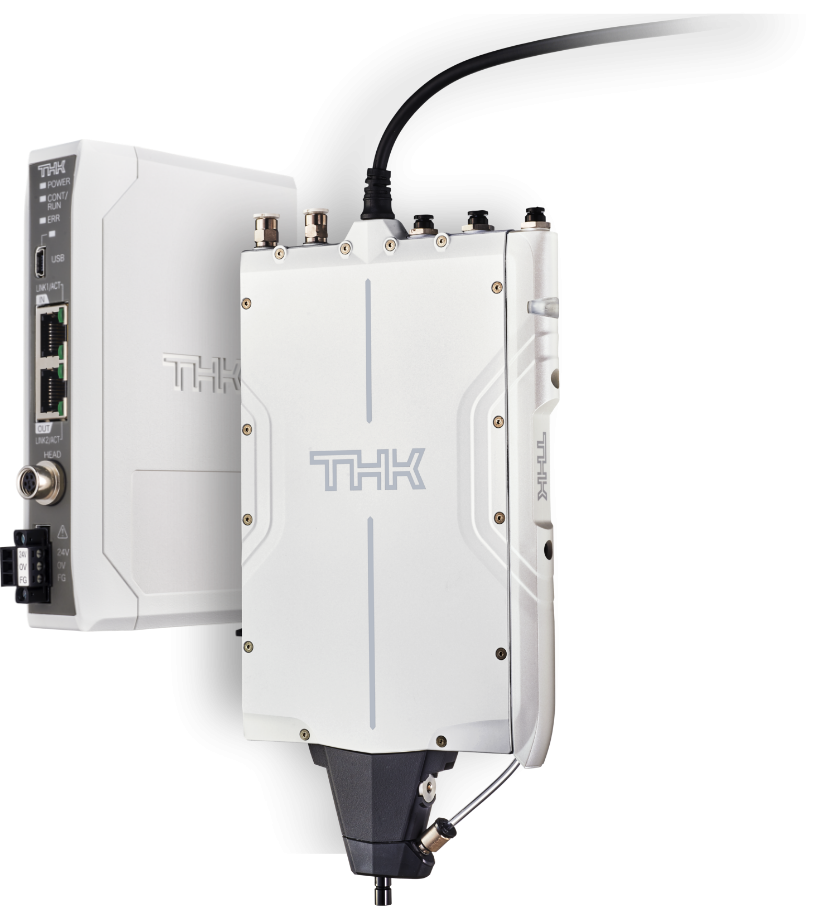
All-in-one model equipped with required components for picking and placing
Pick and Place RobotPPR
The PPR not only supports linear and rotary operation, but also has pneumatic devices and various sensors integrated.
The all-in-one robot combines all components required for optimized pick and place applications.
Features | PPR-LR3 (full spec model) |
PPR-LR3-LF1 (position control only model) |
---|---|---|
High-speed pick and place | ||
High-precision positioning | ||
Contact stop | ||
Force control | ||
Waveform monitor | ※ | |
Space-saving |
* Monitoring of force waveforms is not available.
Please feel free to
contact us regarding
technical consultation
and price/delivery.
Installation Support
Support staff who have mastered the use of the PPR will verify the implementation from many angles to ensure that there are no issues.
When considering a purchase of a product, we will interview you about your needs, starting from concepts such as "something like this" and "I want to run it like this." Please feel free to contact us.
Technical calculation
(cycle time/
transportability)
We can pre-calculate the feasibility of operation based on the mass and inertia of the conveyed object and its operation pattern.
Experiment
(workpiece pick and place trial)
We will experiment using actual workpieces, nozzles, etc. to determine whether or not the envisioned operation can be performed.
Demo machine rental
When considering a purchase, we will be happy to lend you a demo unit. Please contact us with the details you wish to confirm.
Sample program
We can provide a sample operation program that matches the actual usage concept. Please consult us about connecting to PLC.
Case Studies
Technical Information
FAQ
Is stacked installation possible?
Stacked installation is possible.
The mounting pitch is 16 mm.
*For details, please refer to the instruction manual 4-2-4 How to install the head.
Are the screw holes for mounting the body on the side only?
Screw holes for mounting are located on both sides and on the underside.
Side: M4 depth 4 screw holes x 2, φ4H7 depth 4 pin holes x 1, 4H7 depth 4 long holes
Lower holes: M3 depth 3 threaded holes x 2
*Please be careful about the length of the mounting screws to prevent damage to internal components.
*Please refer to the instruction manual 4-2-4 How to install the head.
A timeout has occurred. I would like to investigate the cause.
Confirm the waveform monitor and event history screens.
When a timeout occurs, which module is the last module in operation?
If that step operates and a timeout occurs, it is very likely that it will stop at the next step.
If you send us the waveform data, we will be able to assist you in your investigation.