Studying the Positioning Accuracy
Causes of Error in the Positioning Accuracy
The causes of error in the positioning accuracy include the lead angle accuracy, the axial clearance and the axial rigidity of the feed screw system. Other important factors include the thermal displacement from heat and the orientation change of the guide system during traveling.
Studying the Lead Angle Accuracy
It is necessary to select the correct accuracy grade of the Ball Screw that satisfies the required positioning accuracy from the Ball Screw accuracies (Table1 on Lead Angle Accuracy ). Table20 shows examples of selecting the accuracy grades by the application.
Studying the Axial Clearance
The axial clearance is not a factor of positioning accuracy in single-directional feed. However, it will cause a backlash when the feed direction is inversed or the axial load is inversed. Select an axial clearance that meets the required backlash from Table10 and Table12 on the Axial Clearance .
Applications | Shaft | Accuracy grades | ||||||||
---|---|---|---|---|---|---|---|---|---|---|
C0 | C1 | C2 | C3 | C5 | C7 | C8 | C10 | |||
NC | Lathe | X | ● | ● | ● | ● | ||||
Z | ● | ● | ||||||||
Machining center | XY | ● | ● | ● | ||||||
Z | ● | ● | ● | |||||||
Drilling machine | XY | ● | ● | |||||||
Z | ● | ● | ||||||||
Jig borer | XY | ● | ● | |||||||
Z | ● | ● | ||||||||
Surface grinder | X | ● | ● | |||||||
Y | ● | ● | ● | ● | ||||||
Z | ● | ● | ● | ● | ||||||
Cylindrical grinder | X | ● | ● | ● | ||||||
Z | ● | ● | ● | |||||||
Electric discharge machine |
XY | ● | ● | ● | ||||||
Z | ● | ● | ● | ● | ||||||
Electric discharge machine Wire cutting machine |
XY | ● | ● | ● | ||||||
Z | ● | ● | ● | ● | ||||||
UV | ● | ● | ● | |||||||
Punching press | XY | ● | ● | ● | ||||||
Laser beam machine | X | ● | ● | ● | ||||||
Z | ● | ● | ● | |||||||
Woodworking machine | ● | ● | ● | ● | ||||||
General-purpose machine;dedicated machie | ● | ● | ● | ● | ● | |||||
Industrial robot | Cartesian coordinate | Assembly | ● | ● | ● | ● | ||||
Other | ● | ● | ● | ● | ||||||
Vertical articulated type | Assembly | ● | ● | ● | ||||||
Other | ● | ● | ||||||||
Cylindrical coordinate | ● | ● | ● | |||||||
Semiconductor manufacturing machine |
Photolithography machine | ● | ● | |||||||
Chemical treatment machine | ● | ● | ● | ● | ● | ● | ||||
Wire bonding machine | ● | ● | ||||||||
Prober | ● | ● | ● | ● | ||||||
Printed circuit board drilling machine | ● | ● | ● | ● | ● | |||||
Electronic component inserter | ● | ● | ● | ● | ||||||
3D measuring instrument | ● | ● | ● | |||||||
Image processing machine | ● | ● | ● | |||||||
Injection molding machine | ● | ● | ● | |||||||
Office equipment | ● | ● | ● | ● |
Studying the Axial Clearance of the Feed Screw System
Of the axial rigidities of the feed screw system, the axial rigidity of the screw shaft fluctuates according to the stroke position. When the axial rigidity is large, such change in the axial rigidity of the screw shaft will affect the positioning accuracy. Therefore, it is necessary to take into account the rigidity of the feed screw system ( Studying the Rigidity ).
Example: Positioning error due to the axial rigidity of the feed screw system during a vertical transfer
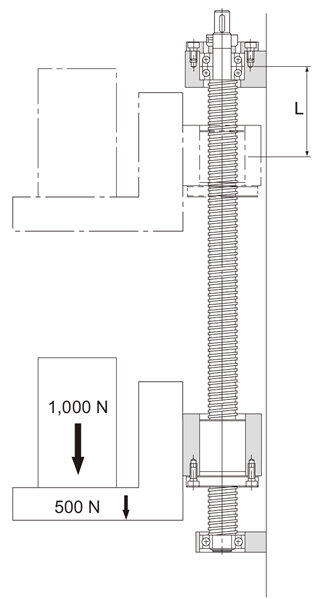
[Conditions]
Transferred weight: 1,000 N; table weight: 500 N
Ball Screw used: model BNF2512-2.5 (screw-shaft thread minor diameter d 1 = 21.9 mm)
Stroke length: 600 mm (L=100 mm to 700 mm)
Screw shaft mounting type: fixed-supported
Consideration
The difference in axial rigidity between L = 100 mm and L = 700 mm applied only to the axial rigidity of the screw shaft.
Therefore, positioning error due to the axial rigidity of the feed screw system equals to the difference in the axial displacement of the screw shaft between L = 100 mm and L = 700 mm.
Axial Rigidity of the Screw Shaft (see Axial rigidity of the screw shaft)
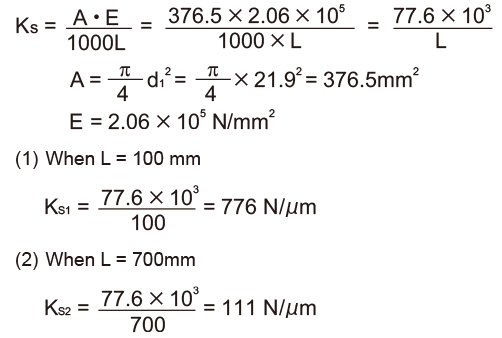
Axial Displacement due to Axial Rigidity of the Screw Shaft
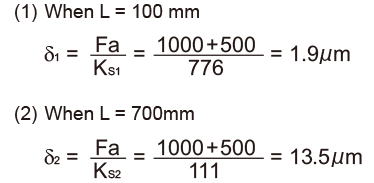
Positioning Error due to Axial Rigidity of the Feed Screw System

Therefore, the positioning error due to the axial rigidity of the feed screw system is 11.6 μm.
Studying the Thermal Displacement through Heat Generation
If the temperature of the screw shaft increases during operation, the screw shaft is elongated due to heat thereby to lower the positioning accuracy. The expansion and contraction of the screw shaft is calculated using the equation (43) below.

Δℓ | Axial expansion/contraction of the screw shaft (mm) |
---|---|
ρ | Thermal expansion coefficient (12×10-6/℃) |
Δt | Temperature change in the screw shaft (℃) |
ℓ | Effective thread length (mm) |
Thus, if the temperature of the screw shaft increases by 1℃, the screw shaft is elongated by 12 μm per meter. Therefore, as the Ball Screw travels faster, the more heat is generated. So, as the temperature increases, the positioning accuracy lowers.Accordingly, if high accuracy is required, it is necessary to take measures to cope with the temperature increase.
Measures to Cope with the Temperature Rise
Minimize the Heat Generation
- Minimize the preloads on the Ball Screw and the support bearing.
- Increase the Ball Screw lead and reduce the rotational speed.
- Select a correct lubricant. (See Accessories for Lubrication .)
- Cool the circumference of the screw shaft with a lubricant or air.
Avoid Effect of Temperature Rise through Heat Generation
- Set a negative target value for the reference travel distance of the Ball Screw.
Generally, set a negative target value for the reference travel distance assuming a temperature increase of 2℃ to 5℃ by heat.
(-0.02mm to -0.06 mm/m) - Preload the shaft screw with tension. (See Fig.10 of the structure on Method for Mounting the Ball Screw Shaft .)
Studying the Orientation Change during Traveling
The lead angle accuracy of the Ball Screw equals the positioning accuracy of the shaft center of the Ball Screw. Normally, the point where the highest positioning accuracy is required changes according to the ball screw center and the vertical or horizontal direction. Therefore, the orientation change during traveling affects the positioning accuracy.
The largest factor of orientation change affecting the positioning accuracy is pitching if the change occurs in the ball screw center and the vertical direction, and yawing if the change occurs in the horizontal direction.
Accordingly, it is necessary to study the orientation change (accuracy in pitching, yawing, etc.) during the traveling on the basis of the distance from the ball screw center to the location where positioning accuracy is required.
Positioning error due to pitching and yawing is obtained using the equation (44) below.

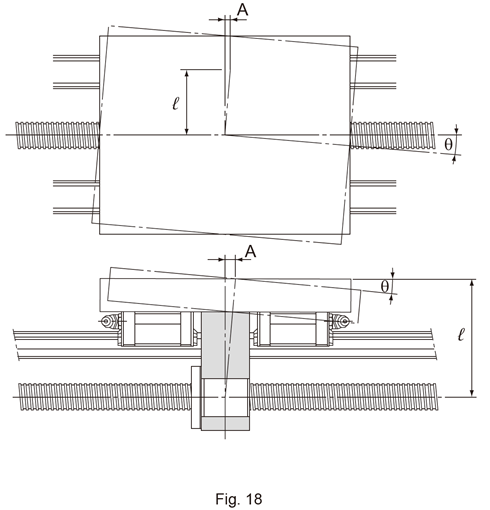
Point of Selection
- Conditions of the Ball Screw
- Conditions of the Ball Screw
- Estimating the shaft length
- Selecting lead・Selecting a shaft diameter
- Method for Mounting the Ball Screw Shaft
- Permissible Axial Load
- Permissible Rotational Speed
- Selecting a Nut
- Calculating the permissible axial load
- Considering the Service Life
- Studying the Rigidity
- Studying the Positioning Accuracy
- Studying the Rotational Torque
- Studying the Driving Motor