Conserving Energy and Preventing Global Warming
Working toward Carbon Neutrality
As exemplified by sustainability, society and corporations generate common value through corporate activities that minimize the negative impacts and strengthen the positive. With this mindset of working for the benefit of all in addition to our individual interests, THK is promoting various initiatives to achieve the creation of a sustainable society. In response to risks posed to the world by climate change from global warming in particular, we established medium- and long-term targets for lowering our emissions of greenhouse gases in August 2021.
First, to minimize our negative impact, we have established the Carbon Neutrality Promotion Project, which is working to further reduce the CO2 emitted through our business activities. Meanwhile, to strengthen our positive impact, we are expanding our offerings of linear motion and other products and services that contribute to energy conservation. We will accelerate our various initiatives in order to achieve these goals.
Medium-Term Target
- By 2030, reduce CO2 emissions to 50% of 2018 levels.
- Scope: THK Japan and Group companies in Japan
Long-Term Target
- By 2050, achieve net-zero CO2 emissions.
- Scope: Entire THK Group
2024 Results
One of our initiatives is the installation of solar power generation systems. In 2024, these generated 16,237 MWh, a 49% increase compared to 2023. In addition to that, production equipment was updated to more efficient types.
As a result, THK Japan and Group companies in Japan saw CO2 emissions drop to 80,406 tons, which was a 25% reduction from the baseline year of 2018.
Solar Power Generated
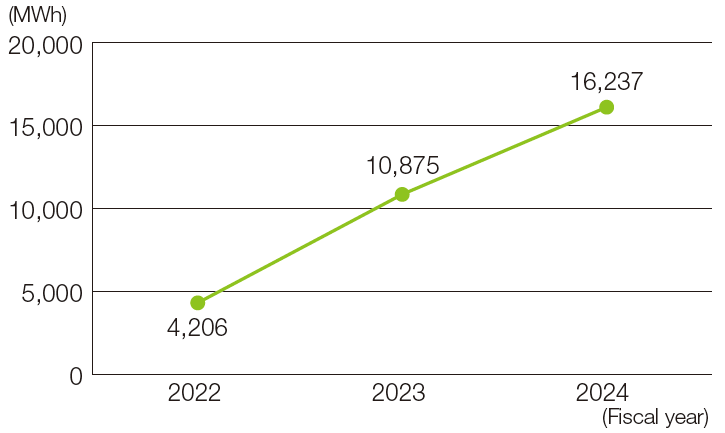
CO2 Emissions
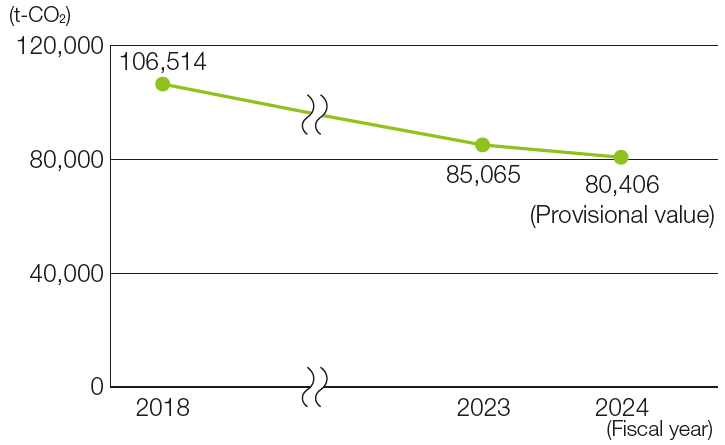
J-Credit Purchases
THK Japan purchased Matsusaka City Forest Management for the Future J-Credits sold by Matsusaka, Mie Prefecture.
J-Credit is a system in which the Japanese government certifies carbon credits in proportion to the reduction of CO2 emissions due to installation of energy saving equipment, utilization of renewable energy, or absorption of CO2 through responsible forest management.
The city of Matsusaka decided to sell the J-Credits that it acquired to local businesses, and as the Mie plant is located in Matsusaka, THK Japan purchased credits equaling 300 tons of CO2.
These credits account for approximately 5% of the Mie plant’s total 2023 emissions (Scope 1 and 2) and will be used to achieve our GHG reduction goals.
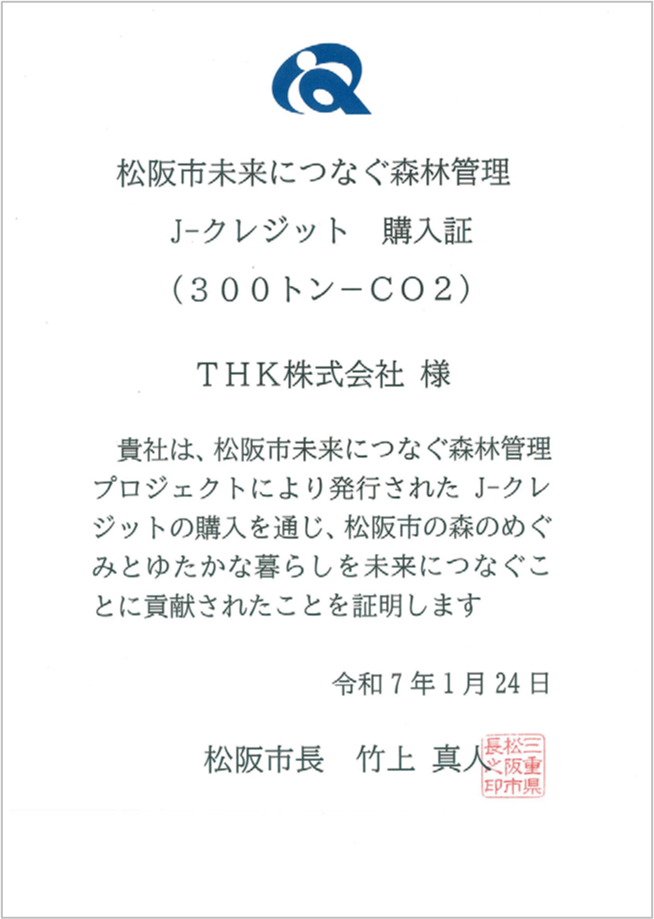
External Verification
ISO14064 Third-Party Verification
The calculations for Scope 1 and Scope 2 emissions generated by energy consumption at THK Japan and Japanese Group company production facilities in the 2024 fiscal year (January 1 to December 31, 2024) received third-party verification (limited level of assurance) based on ISO 14064-3 by the Japan Quality Assurance Organization.
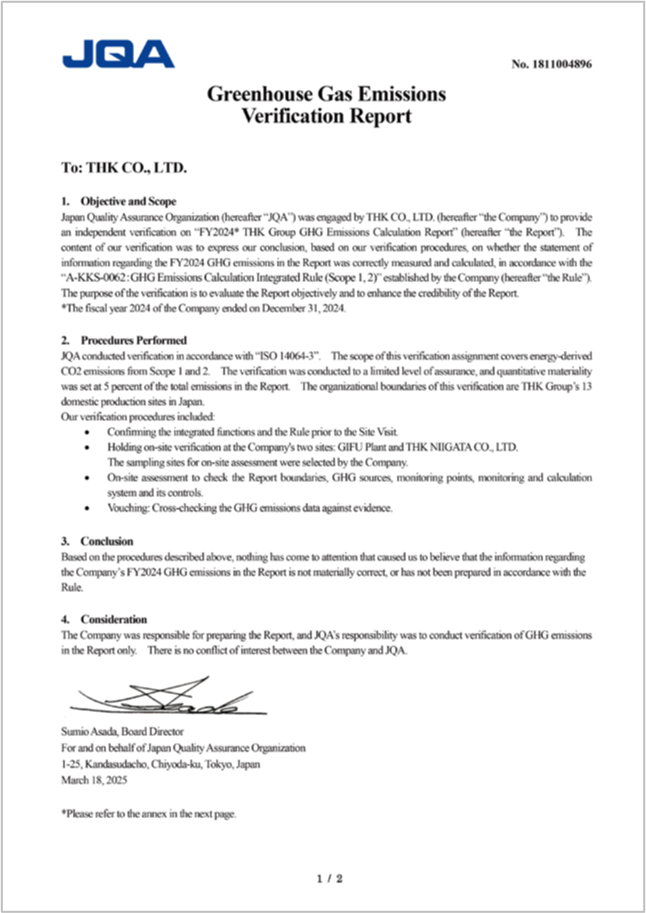
Activities and Results
Efforts at Each Facility
Kofu Plant
Replaced Extra-High Voltage Distribution Substation
The work begun in 2022 to upgrade from an aging extra-high voltage substation was completed in August 2024. As a result, CO2 emissions were reduced by about 5.15 tons per year, and energy consumption decreased by the equivalent of about 2.8 kL of crude oil.
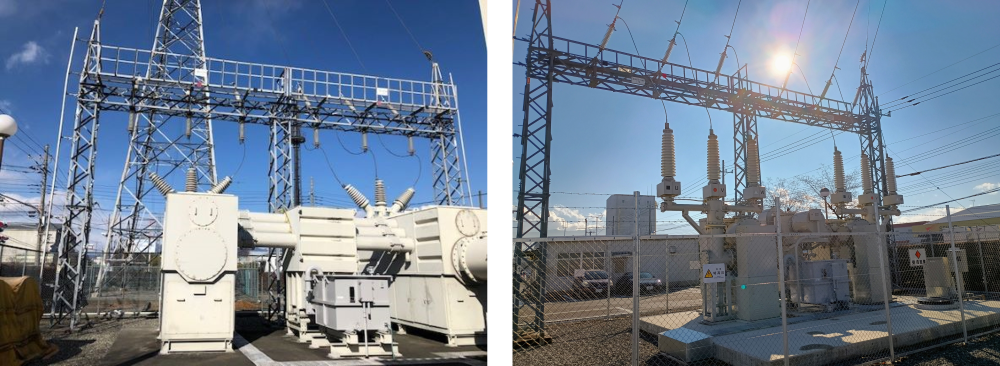
Installed Mist Cooling System for an Outdoor Air Conditioning Unit
This system was installed in August to see if cooling the outdoor air conditioning units on the south side of Factory 3 would make heat exchange more efficient. Because CO2 emissions were reduced by about 0.23 tons per year and energy consumption decreased by the equivalent of about 0.13 kL of crude oil, it was decided to install an additional 12 such systems in 2025.
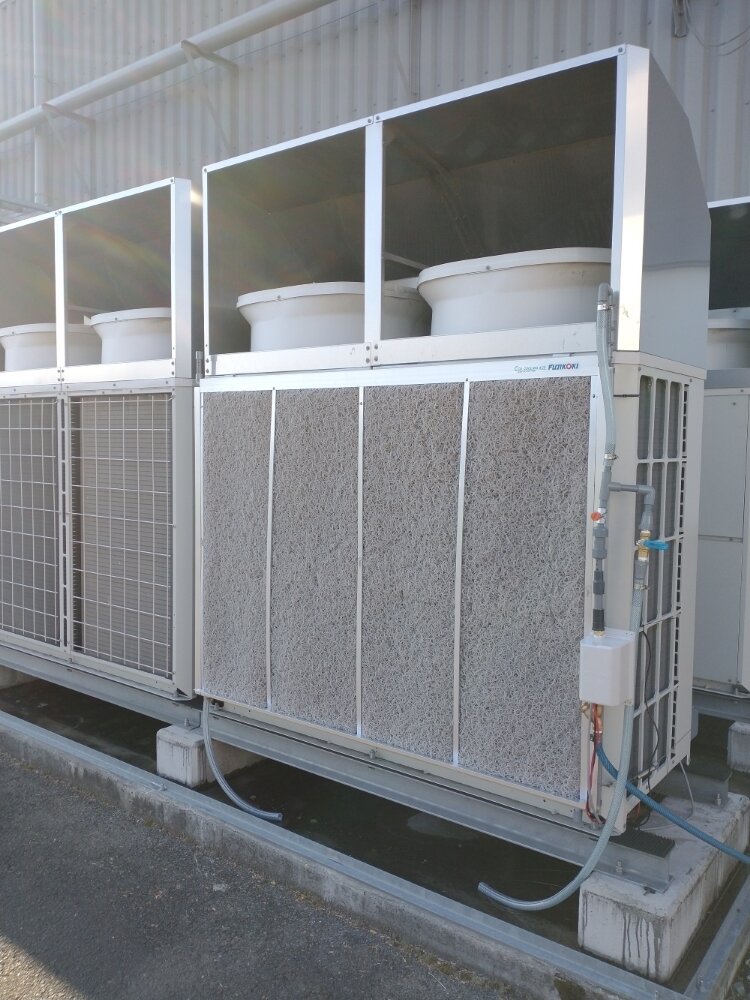
Gifu Plant
Purchasing Green Energy
In November 2023, the plant entered into a contract to purchase 20% of the energy it uses as green energy to help reduce CO2 emissions. As a result, CO2 emissions were reduced by about 1000.1 tons, and energy consumption decreased by the equivalent of about 485.7 kL of crude oil in 2024.
Automated Control for Air Compressors
All air compressors in the plant were changed to have automatic control. Compressors that don’t need to run over the weekend or at night are shut off with timers to reduce power consumption. As a result, CO2 emissions were reduced by about 3.7 tons per year, and energy consumption decreased by the equivalent of about 1.8 kL of crude oil.
Updated to an Electric Forklift
The 3-ton forklift used by the materials section was replaced with an electric one. The four remaining forklifts are to be replaced with electric ones by 2027. As a result of updating this first forklift, CO2 emissions were reduced by about 4.5 tons per year, and energy consumption decreased by the equivalent of about 1.7 kL of crude oil.
Mie Plant
Thermal Coating for Roofs
Thermal coating was applied to the roof of Grinding Factory 2 in May and to the roofs of Grinding Factory 1, the office building, and the gatekeeper post in November. As a result, CO2 emissions were reduced by about 32.4 tons per year, and energy consumption decreased by the equivalent of about 17.4 kL of crude oil.
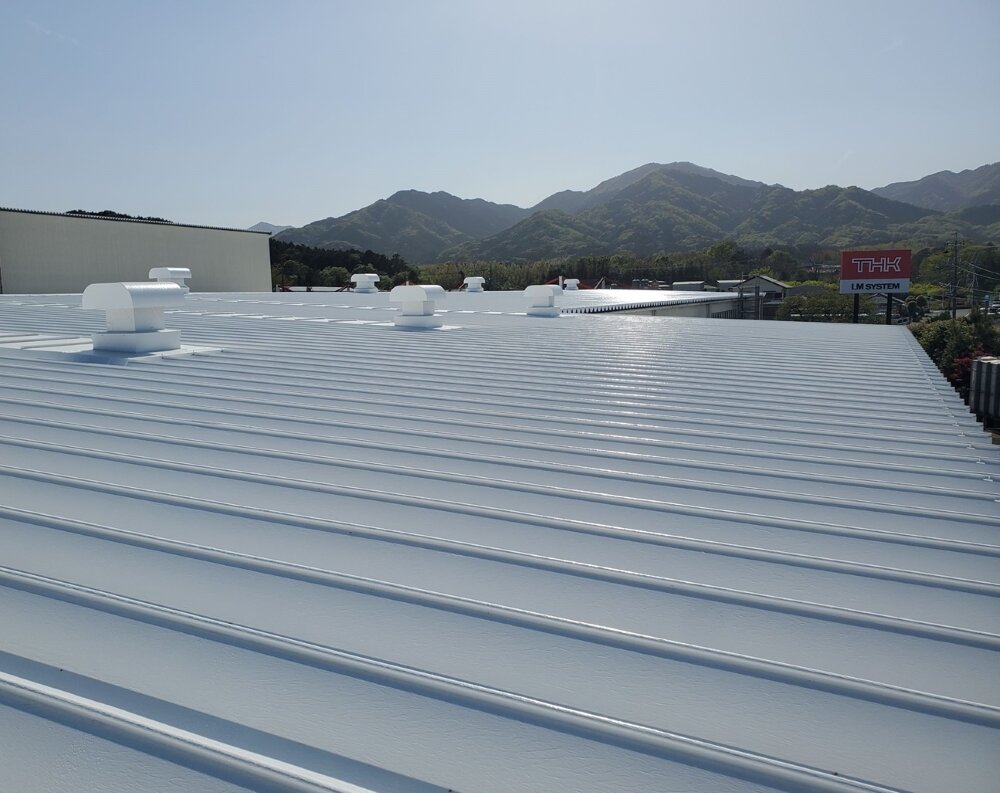
Upgraded Heater
One of two carburizing furnace heaters in the quenching process at Heat Treatment Factory 2 was upgraded in April (the other had been replaced in 2023). As a result, CO2 emissions were reduced by about 4.9 tons per year, and energy consumption decreased by the equivalent of about 2.9 kL of crude oil.
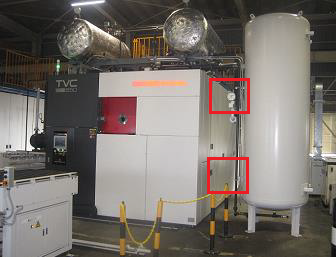
Yamaguchi Plant
Upgraded Air Dryers
Nine aging air dryers for the air compressors around the plant were upgraded in August. As a result, CO2 emissions were reduced by about 8.004 tons per year, and energy consumption decreased by the equivalent of about 3.23 kL of crude oil.
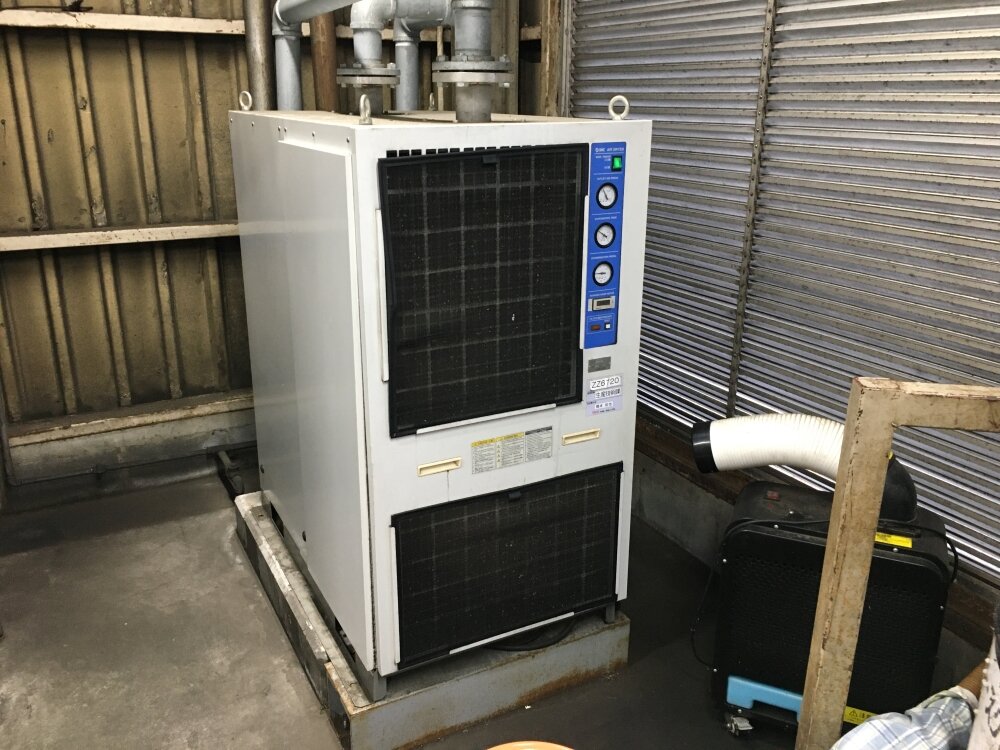
Upgraded Chiller
An aging washing machine chiller at the Technical Plant was upgraded in September. As a result, CO2 emissions were reduced by about 12.84 tons per year, and energy consumption decreased by the equivalent of about 5.18 kL of crude oil.
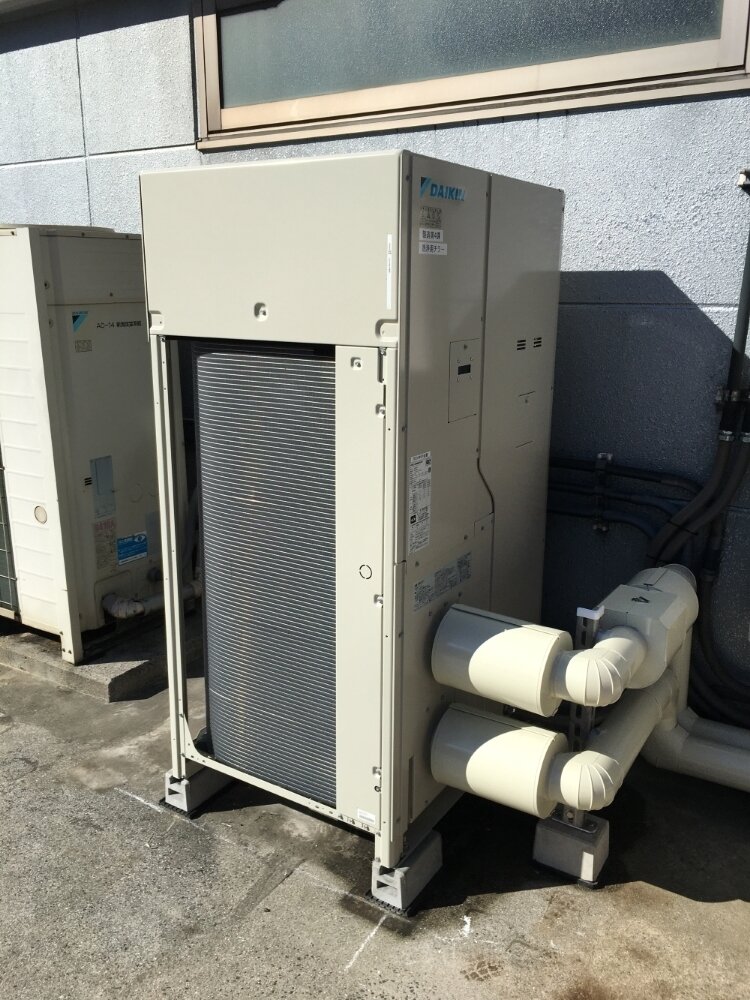
Upgraded Air Conditioner Inverter
An air conditioner inverter at Factory 1 that had broken down was replaced in August. As a result, CO2 emissions were reduced by about 16.8 tons per year, and energy consumption decreased by the equivalent of about 6.80 kL of crude oil.
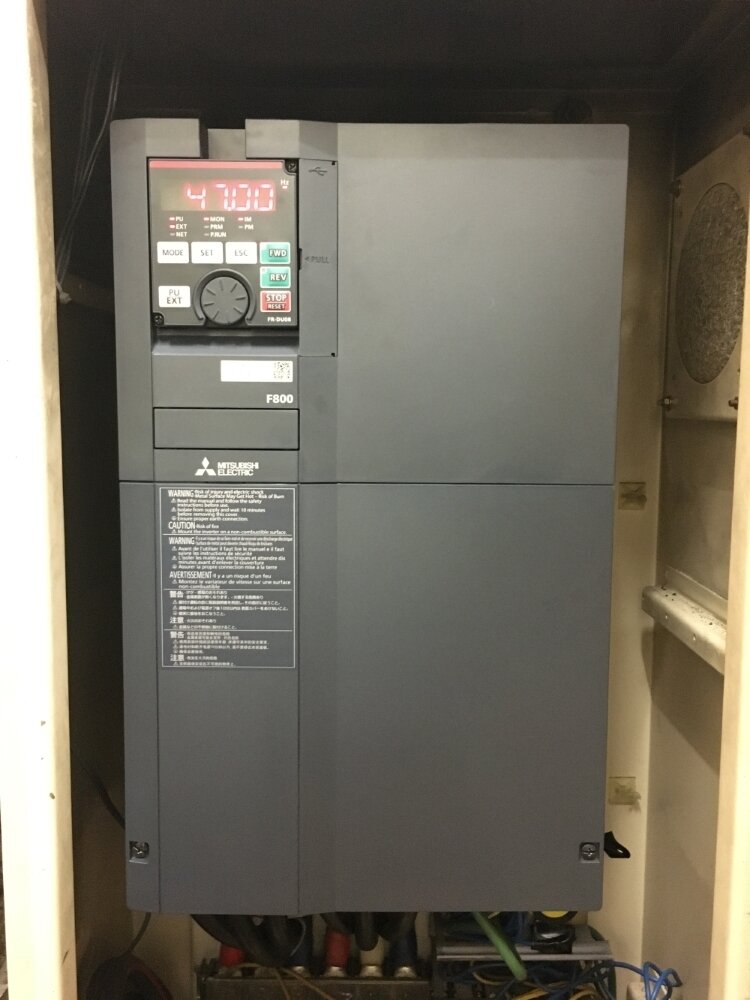
THK NIIGATA
Installation of Fluid Agitators
In May, fluid agitators were installed on two package air conditioners used by the wire electrical discharge machining process at Factory 1 to reduce transfer loss, improve thermal conductivity, and lighten the burden on the compressors. As a result, CO2 emissions were reduced by about 6.7 tons per year, and energy consumption decreased by the equivalent of about 3.2 kL of crude oil.
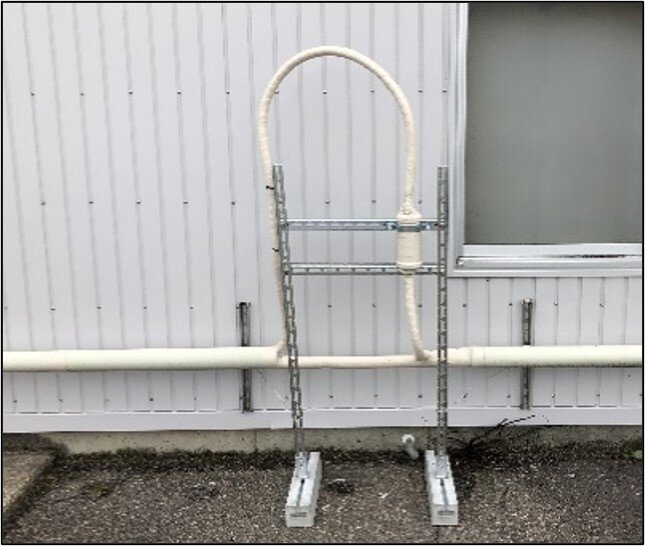
THK INTECHS Mishima Plant
Air Conditioner Upgrade
The oil furnace for the Factory 1 assembly process was replaced with an inverter air conditioning unit in June. As a result, CO2 emissions were reduced by about 1.72 tons per year, and energy consumption decreased by the equivalent of about 1.32 kL of crude oil.
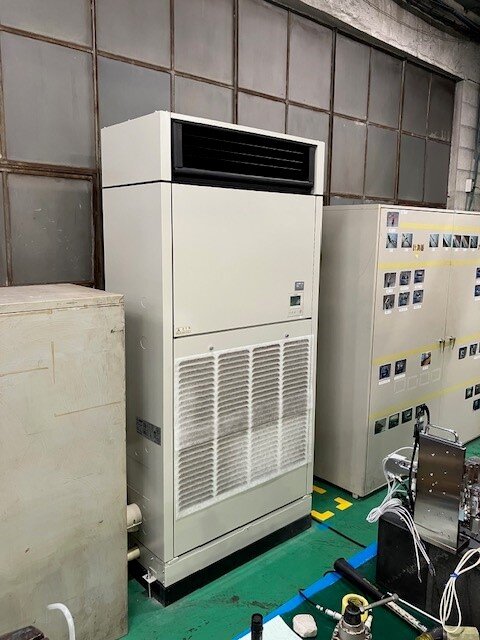
THK RHYTHM Hamamatsu Plant
Upgraded HVAC Equipment
Two aging HVAC units for the second floor of the welfare building were replaced in January. As a result, CO2 emissions were reduced by about 2.6 tons per year, and energy consumption decreased by the equivalent of about 1.4 kL of crude oil.
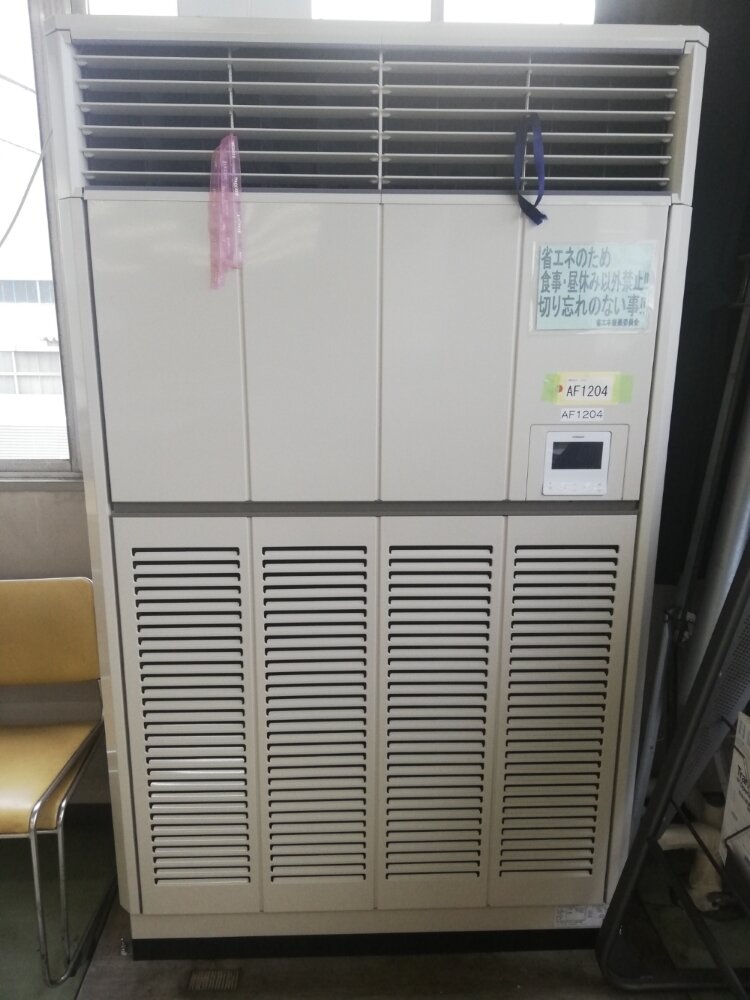
Installed Insulation
In February, insulation panels were installed on Aluminum Melting Furnace 2 at the Heat Treatment Factory to reduce fuel consumption. As a result, CO2 emissions were reduced by about 25.5 tons per year, and energy consumption decreased by the equivalent of about 11.1 kL of crude oil.
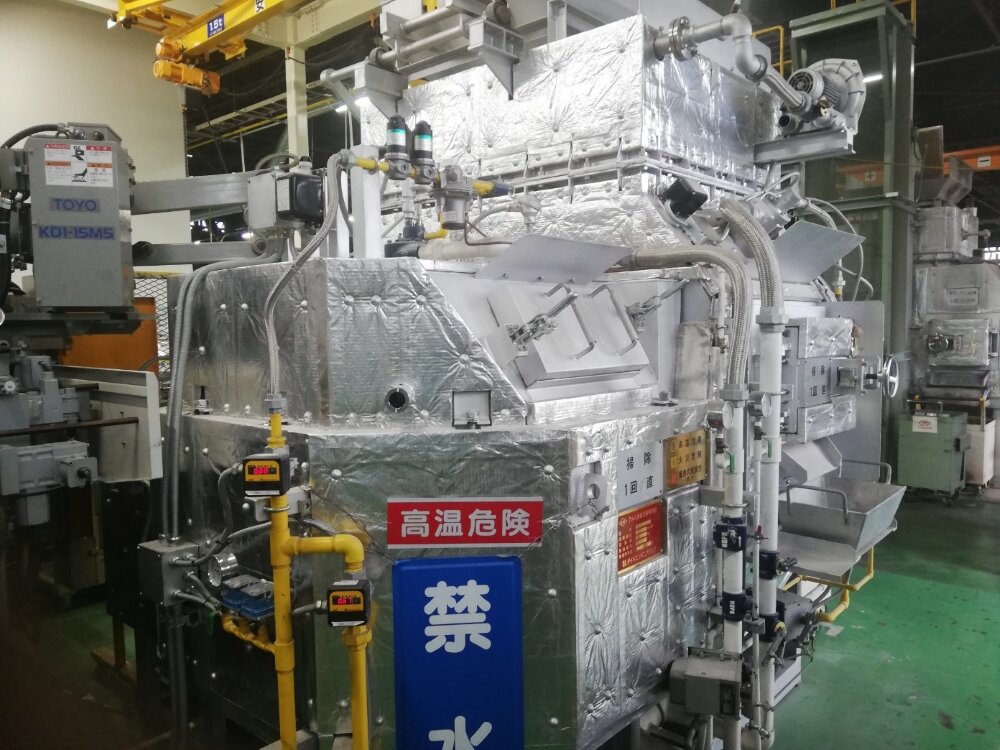
Installed Heat Exhaust Duct
A heat exhaust duct was added to the dryer for retainer material in August to reduce the load on the air conditioning system. As a result, CO2 emissions were reduced by about 43.4 tons per year, and energy consumption decreased by the equivalent of about 20.4 kL of crude oil.
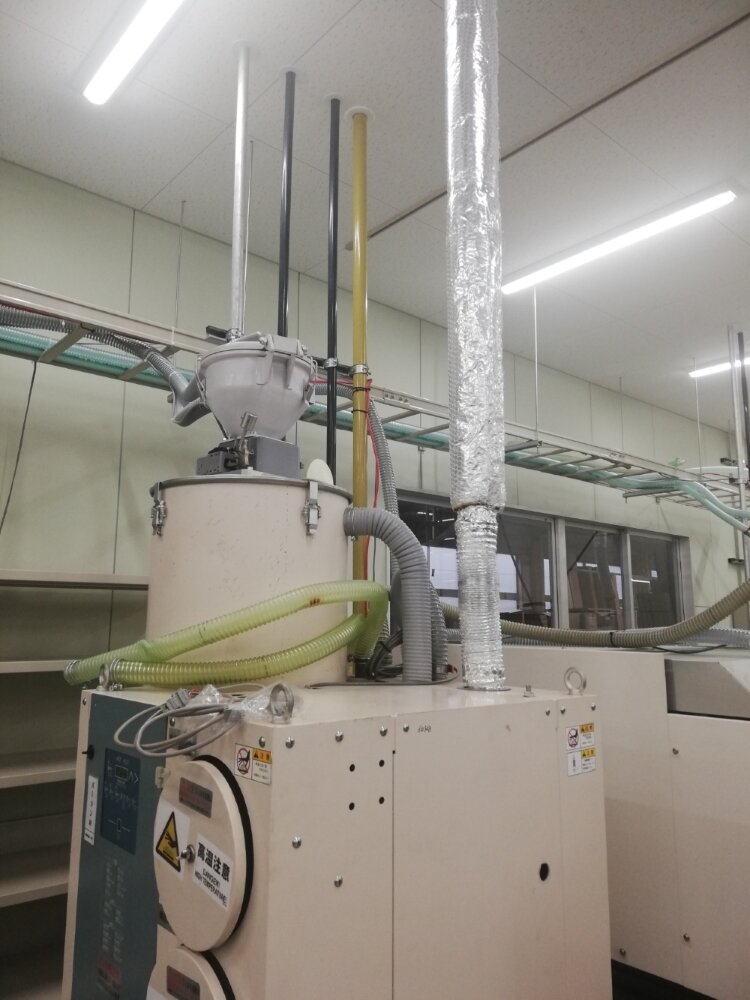
THK RHYTHM Kyushu Plant
Upgraded Compressors
An aging 75 kW unit in the compressor room was replaced in March. As a result, CO2 emissions were reduced by about 20.9 tons per year, and energy consumption decreased by the equivalent of about 9.8 kL of crude oil.
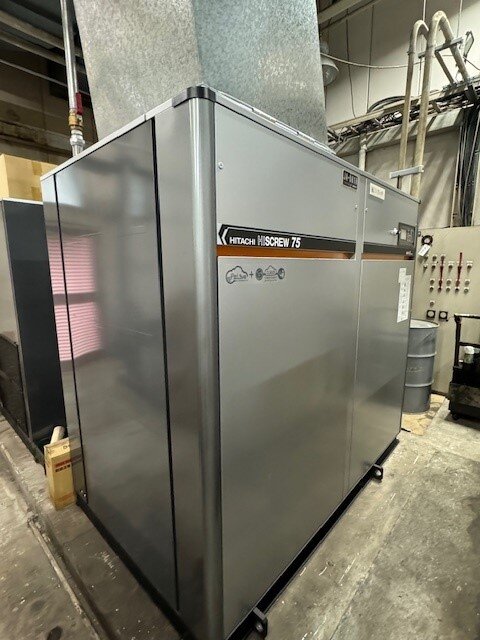
Upgraded Boiler
A small steam boiler used for heating during preprocessing for the cationic electrodeposition coating line was replaced in April due to aging. As a result, CO2 emissions were reduced by about 2.0 tons per year, and energy consumption decreased by the equivalent of about 0.9 kL of crude oil.
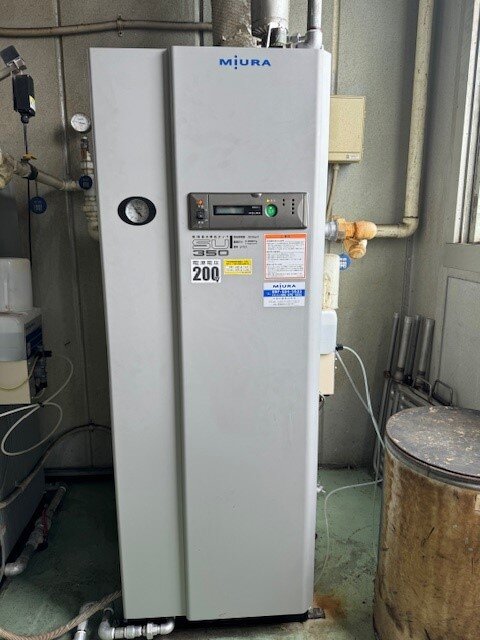
NIPPON SLIDE
Upgraded Compressors
Four aging compressors on the first and second floors of the plant were replaced with two updated models in June. As a result, CO2 emissions were reduced by about 2.28 tons per year, and energy consumption decreased by the equivalent of about 1.505 kL of crude oil.
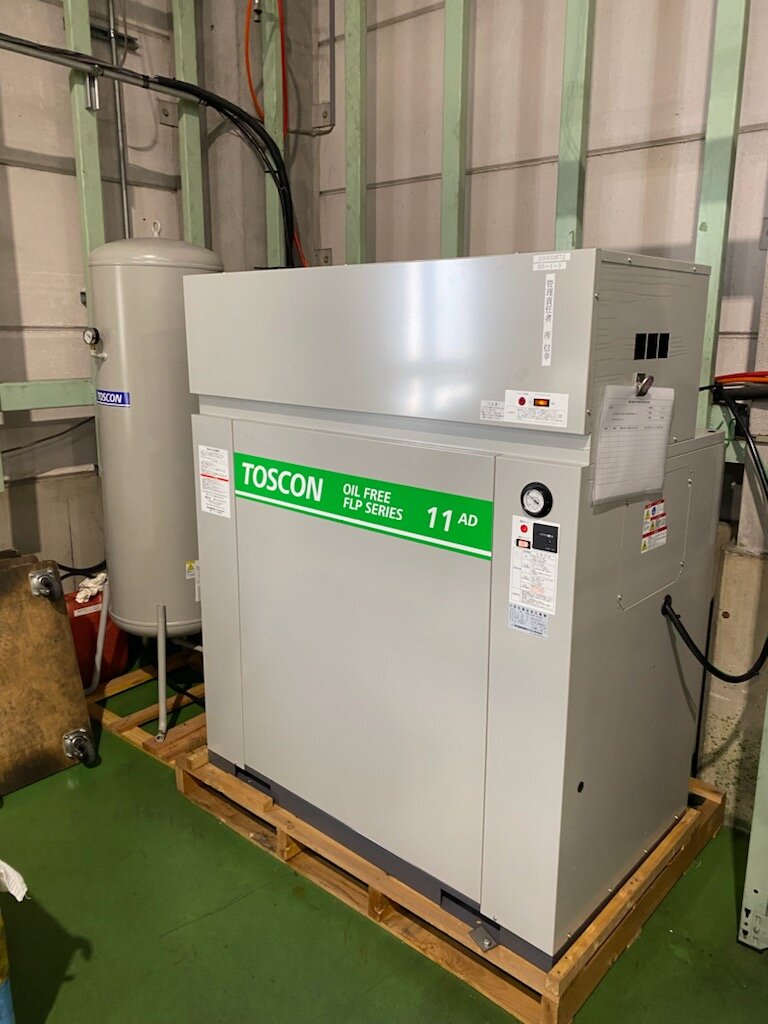
Wuxi Plant (China)
Heat Exhaust for Oil Compressors
The semi-centralized equipment for nine grinders was modified with ducts to send exhaust heat from the oil compressors to the outside of the plant during the summer months (June through August). As a result, CO2 emissions were reduced by about 2.0 tons per year, and energy consumption decreased by the equivalent of about 0.9 kL of crude oil.
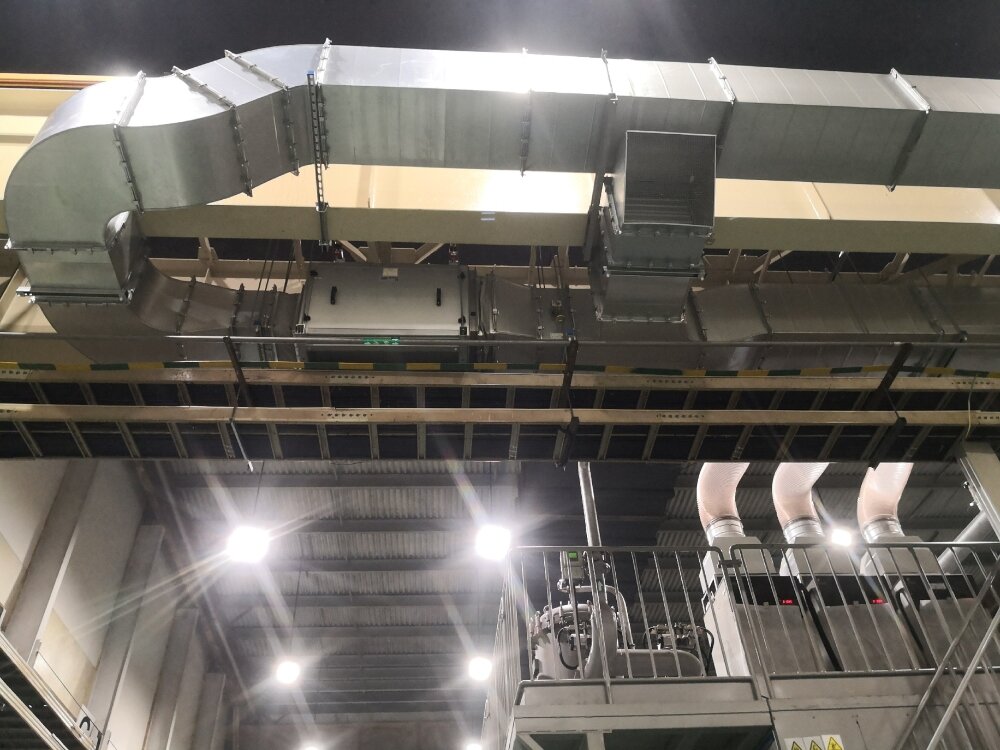
Insulated Compressor Exhaust Ducts
From May to July, insulation was added to exhaust ducts in the compressor room to control the temperature and reduce the number of irregular shutdowns. As a result, CO2 emissions were reduced by about 2.0 tons per year, and energy consumption decreased by the equivalent of about 0.9 kL of crude oil.
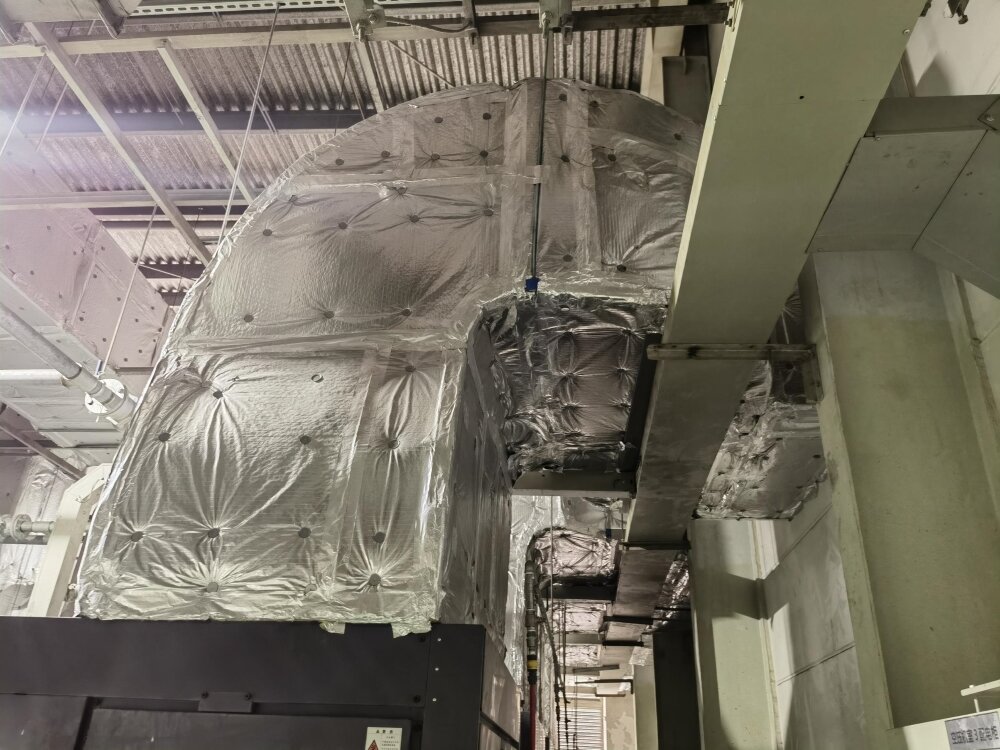
DALIAN THK (China)
Forklift Upgrade
Two gas-powered forklifts were changed to electric types in August. With this upgrade, DALIAN THK has converted all four of its forklifts to electric types. As a result, annual CO2 emissions were reduced by about 3.5 tons.
Changzhou Plant (China)
Energy Storage Equipment
This facility considered adding on to the first factory's solar power generating system, but after searching for the best solution overall, they implemented an energy storage system instead. Now, the factory can generate all the solar power it needs on sunny days and can store energy at night to make up for what solar power doesn't cover during less ideal weather.
TMV (Vietnam)
Changed LED Wattage
After determining at the start of the year that some locations were brighter than necessary, 300 LEDs were changed from 18 W to 14 W. As a result, CO2 emissions were reduced by about 1.8 tons per year, and energy consumption decreased by the equivalent of about 0.7 kL of crude oil.
Recycling of Resin Dryer Exhaust Heat
Starting in April, some of the exhaust heat from 23 resin dryers was redirected to intake ducts and reused for indoor climate control. As a result, CO2 emissions were reduced by about 32.0 tons per year, and energy consumption decreased by the equivalent of about 12.6 kL of crude oil.
Installed Insulated Covers
Insulated covers were installed on the barrels of 47 resin molding machines. These barrels are heated to 270°C, but heat is lost to the surrounding air. With the installation of these covers, the amount of heat lost has been reduced.
As a result, CO2 emissions were reduced by about 27.7 tons per year, and energy consumption decreased by the equivalent of about 7.1 kL of crude oil.
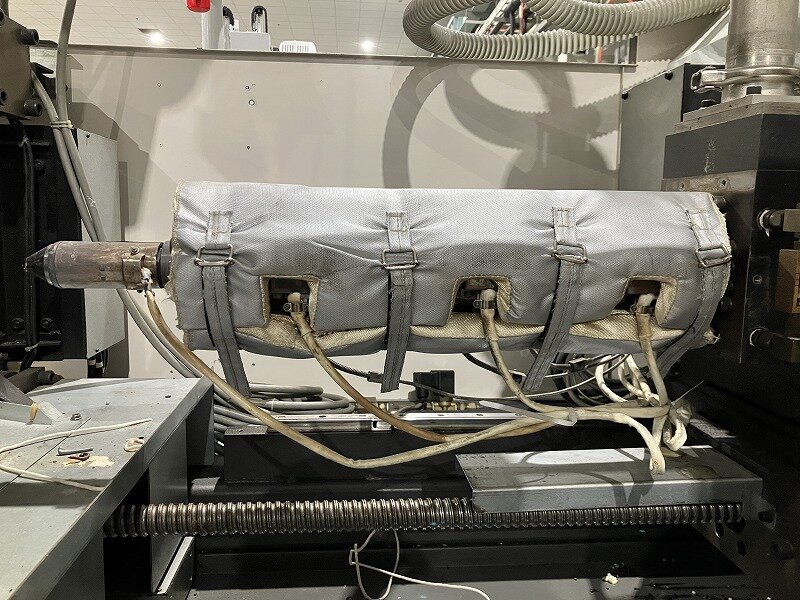
TMA (USA)
Compressor Upgrade
An aging compressor shared by the LM Guide and Link Ball departments was replaced in July. As a result, CO2 emissions were reduced by about 32.4 tons per year, and energy consumption decreased by the equivalent of about 11.0 kL of crude oil.
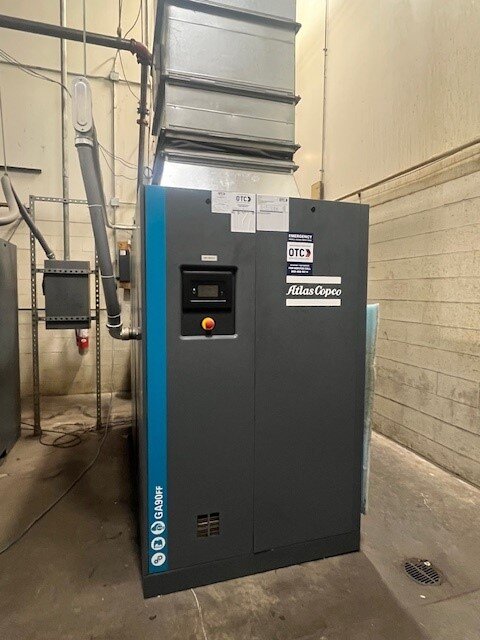
Green Distribution
THK INTECHS Sendai Plant
Modal Shifts
We’ve transitioned from shipping by truck to using JR freight for products bound for certain customers. As a result, annual CO2 emissions were reduced by about 10,200 tons.