Conserving Energy and Preventing Global Warming
Working toward Carbon Neutrality
As exemplified by sustainability, society and corporations generate common value through corporate activities that minimize the negative impacts and strengthen the positive. With this mindset of working for the benefit of all in addition to our individual interests, THK is promoting various initiatives to achieve the creation of a sustainable society. In response to risks posed to the world by climate change from global warming in particular, we established medium- and long-term targets for lowering our emissions of greenhouse gases in August 2021.
First, to minimize our negative impact, we have established the Carbon Neutrality Promotion Project, which is working to further reduce the CO2 emitted through our business activities. Meanwhile, to strengthen our positive impact, we are expanding our offerings of linear motion and other products and services that contribute to energy conservation. We will accelerate our various initiatives in order to achieve these goals.
Medium-Term Target
- By 2030, reduce CO2 emissions to 50% of 2018 levels.
- Scope: THK Japan and Group companies in Japan
Long-Term Target
- By 2050, achieve net-zero CO2 emissions.
- Scope: Entire THK Group
Reflecting on the 2023 Fiscal Year
In 2023, we promoted activities to achieve carbon neutrality centered on the production facilities of THK Japan and Group companies in and outside of Japan. As a result, THK Japan and Group companies in Japan saw CO2 emissions drop to 85,103 tons, which was a 20% reduction from the baseline year of 2018 and a 17% reduction compared to 2022.
One example of the activities that yielded this result is the installation of new solar power generation equipment at four production facilities (the Yamagata plant, THK NIIGATA, THK Liaoning, and THK RHYTHM Thailand). As of the end of December, there were a total of 10 facilities making use of renewable energy. These facilities generate a total of 10,875 MWh, an increase of 159% over 2022 (see the renewable energy section of the environmental impact
overview). In addition, THK actively pursued the installation of new high-efficiency production machines and
other equipment as well as the transition to LED lighting. Please see our homepage for details about our activities at each facility.
The results of each facility’s environmental activities are shared through various committees, and THK is building a structure for expanding the implementation of effective methods to other locations.
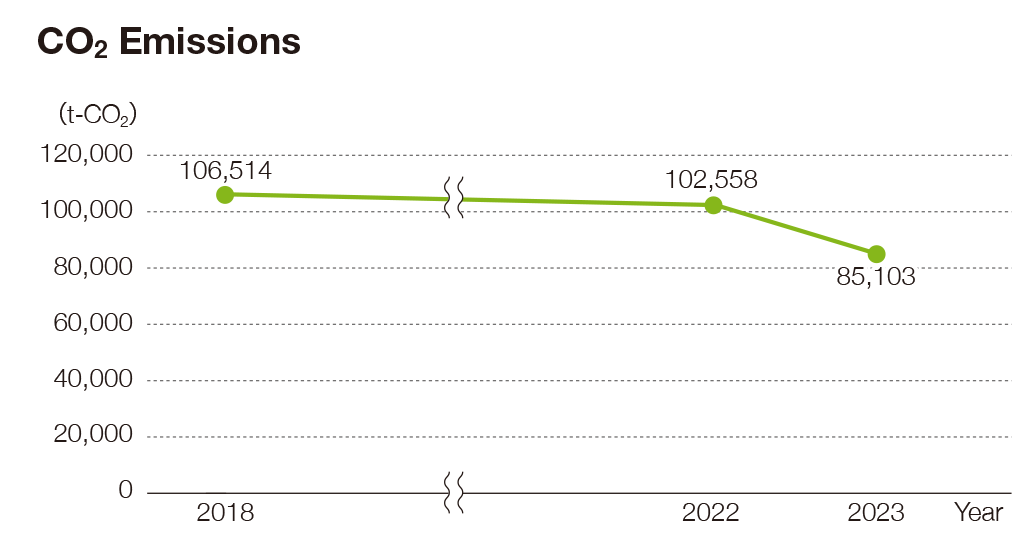
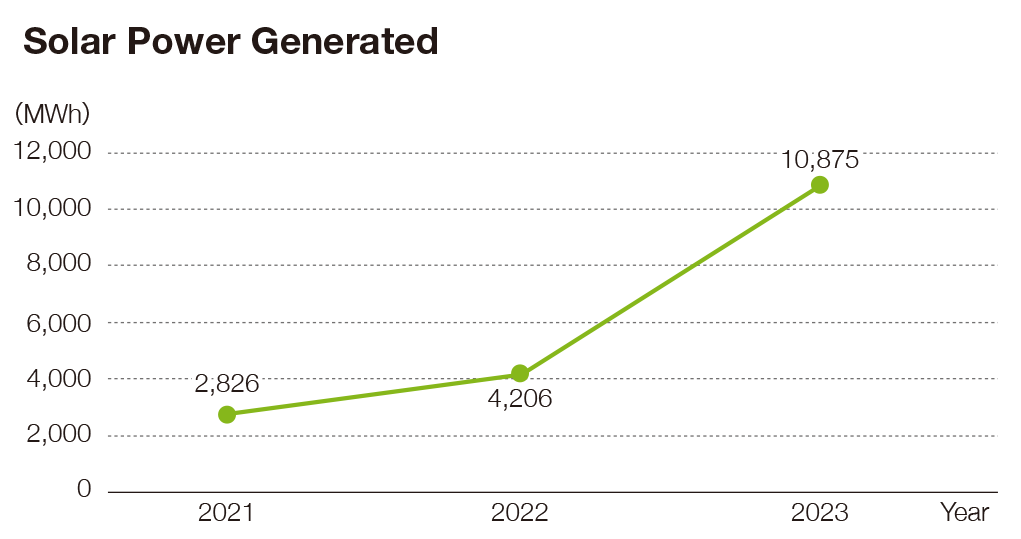
Main Environmental Committees
Annual plan | Details | Result |
---|---|---|
Environmental Committee | Decides on the THK Group’s environmental goals, policies, and promotion plans and reports on the implementation status of said plans. | Convened four times during the year (in February, May, August, and November) |
General Meeting for Environmental Measures | Reports on the environmental initiatives of THK Japan (administrative departments and production facilities) and related Group production facilities. | Convened twice during the year (in February and September) |
Carbon Neutrality Promotion Project Meeting | Reports on the carbon neutrality initiatives of THK Japan’s production facilities and THK NIIGATA. | Convened four times during the year (in January, May, July, and November) |
External Certifications
Third-Party Certification (ISO 14064)
We have received third-party verification that our Scope 11 and Scope 22 GHG emissions calculations during the 2023 fiscal year (January 1 to December 31, 2023) are in accordance with the ISO 14064-3 calculation rules stipulated by the Japan Quality Assurance Organization (at a limited level of assurance for the ISO 14064-3 verification standard).
2023 THK CO., LTD. GHG Emissions Calculation Report
Scope: Six factories (Yamaguchi, Yamagata, Kofu, Mie, Gifu, and THK NIIGATA)
Target items: CO2 created by Scope 1 and 2 energy consumption
Scope1 | 7,816 t-CO2 |
---|---|
Scope2 | 60,423 t-CO2 |
Total | 68,239 t-CO2 |
1 Scope 1:Direct greenhouse gas emissions that a business generates itself
2 Scope 2:Indirect emissions that accompany the use of electricity, heat, or steam supplied by other companies
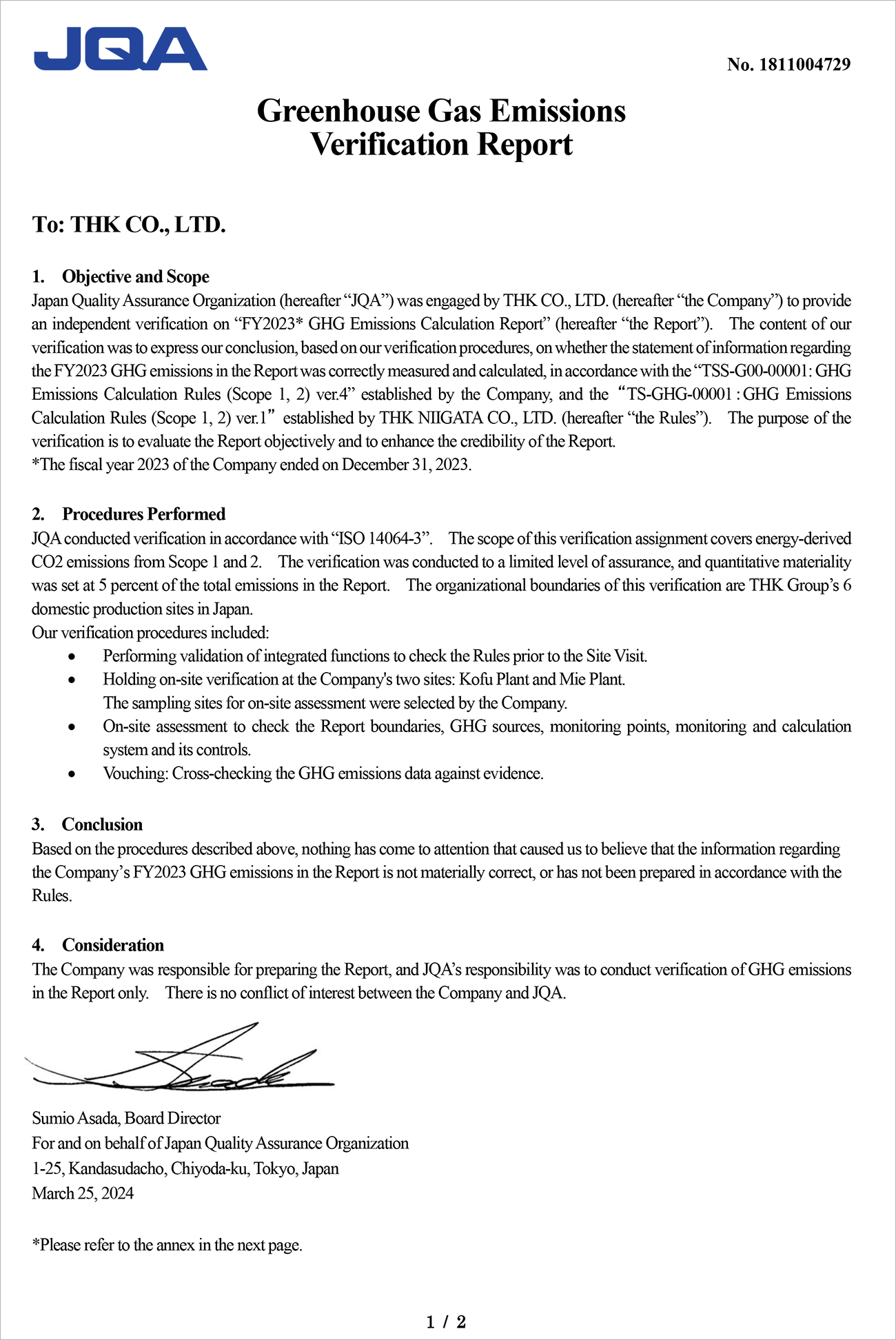
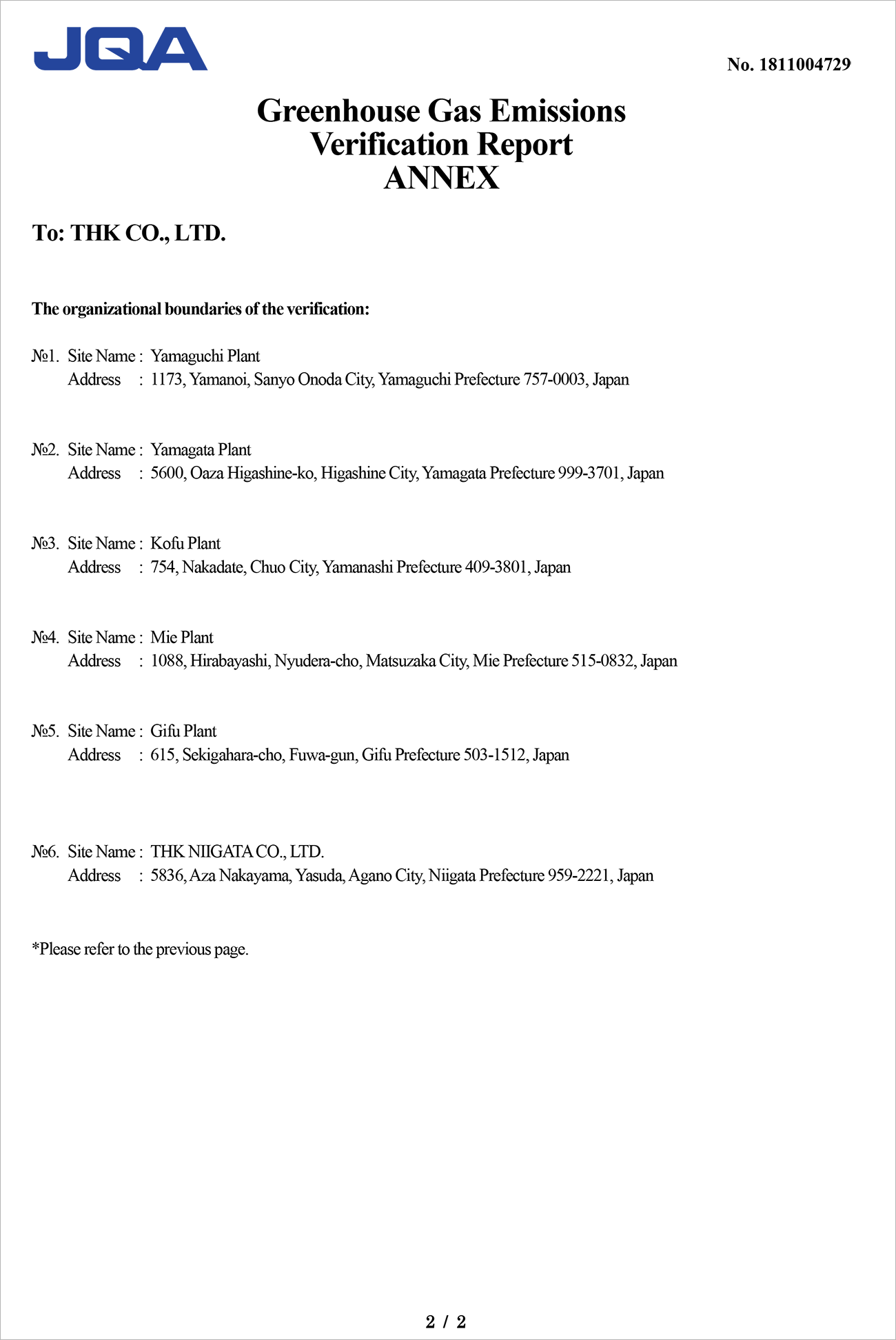
ISO 14001 Certified Facilities
Japan
Production Facility | Country | Certifying Body |
---|---|---|
Yamagata Plant, Kofu Plant, Gifu Plant, Mie Plant, Yamaguchi Plant, THK NIIGATA | Japan | JQA |
THK RHYTHM Headquarters, Hamamatsu Plant, Inasa Plant, Kyushu Plant | JIA | |
THK INTECHS Headquarters, Mishima Plant, Sendai Plant | ClassNK |
Europe
Production Facility | Country | Certifying Body |
---|---|---|
THK Manufacturing of Europe | France | AFAQ |
THK RHYTHM AUTOMOTIVE GmbH | Germany | DQS |
THK RHYTHM AUTOMOTIVE CZECH | Czech Republic | DQS |
The Americas
Production Facility | Country | Certifying Body |
---|---|---|
THK Manufacturing of America | USA | SAI GLOBAL |
THK RHYTHM NORTH AMERICA | SQA | |
THK RHYTHM AUTOMOTIVE MICHIGAN | DQS | |
THK RHYTHM AUTOMOTIVE CANADA(Tillsonburg) | Canada | DQS |
THK RHYTHM AUTOMOTIVE CANADA(St.Catharines) | DQS |
Asia
Production Facility | Country | Certifying Body |
---|---|---|
THK MANUFACTURING OF CHINA (WUXI) | China | TÜV |
DALIAN THK, THK MANUFACTURING OF CHINA (LIAONING) | TÜV | |
THK RHYTHM CHANGZHOU | BUREAU VERITAS |
|
THK RHYTHM GUANGZHOU | SGS | |
THK RHYTHM MALAYSIA | Malaysia | DQS |
THK RHYTHM(THAILAND) | Thailand | URS |
Activities and Results
LED Bulb Replacements
The details and results of our LED upgrades during 2023 are summarized below.
Facility | Location | Time frame | Type and number of bulbs | Reductions | |
---|---|---|---|---|---|
Electricity used (kWh) | |||||
Yamagata Plant | Factories 1, 2, and 3 and their exteriors | August | Mercury and metal halide: 492 Fluorescent: 1,689 |
86,700 | |
Kofu Plant | Various locations | May | Fluorescent: 1,056 | 24,648 | |
Mie Plant | Factory 2, MIE Technology Corporation | May | Fluorescent: 92 | 7,328 | |
Yamaguchi Plant | Zones A, B, and C | November | Mercury: 356 | 592,612 | |
Fluorescent: 1,099 | 104,118 | ||||
THK RHYTHM Hamamatsu Plant | Outdoor light poles
Security lights |
October | Sodium: 3
Fluorescent: 9 |
1,118 | |
THK RHYTHM Kyushu Plant | Office | November | Fluorescent: 17 | 430 | |
TMA | Die Cast (LB) fluorescent ceiling lights | January to October | Fluorescent: 348 | 57,849 | |
Assembly (LB) | January to October | Metal halide: 12 | 28,934 | ||
Office fluorescent lights | January to October | Fluorescent: 263 | 48,761 | ||
Assembly (LM) | January to October | Fluorescent: 682 | 197,736 | ||
TRA Düsseldorf | Office building and production floor | July | Fluorescent: 964 | 73,752 | |
TRA Czech | Wrap and pack area | August | Fluorescent: 122 | 35,490 | |
Production floor | February | Fluorescent: 90 | 16,919 | ||
Locker rooms | September | Fluorescent: 100 | 18,799 | ||
January | Fluorescent: 36 | 3,514 | |||
Office | July | Fluorescent: 38 | 4,740 |
Efforts at Each Production Facility
Yamagata Plant
Outside Air Intake Method Revision
Improvements to the outside air intake method for the air conditioners used at Factory 2 were made, reducing the amount of LPG used in the winter. As a result, CO2 emissions were reduced by about 12.0 tons per year, and energy consumption decreased by approximately 52.0 kL of crude oil per year.
Kofu Plant
Updating HVAC Equipment
Five units were updated in Factory 1, two in Factory 2, and one in the hallway of Factory 4 by the end of December. As a result, CO2 emissions were reduced by about 1.3 tons per year, and energy consumption decreased by approximately 3,000 kWh per year.
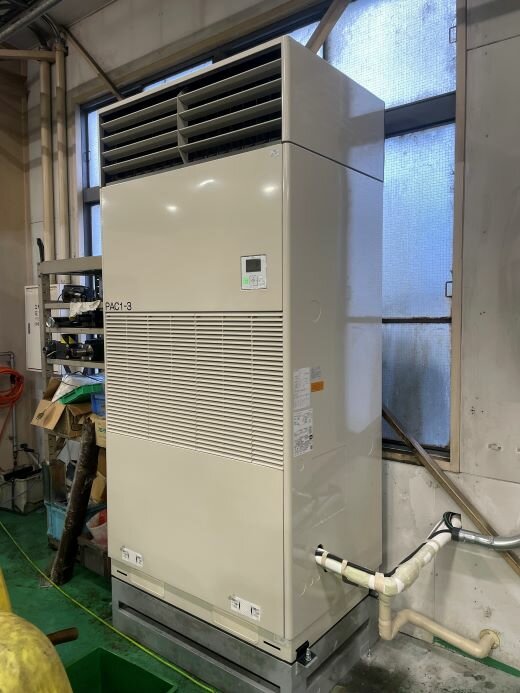
Hot Water Pump Replacement
The hot water pump used in the boiler room was replaced with a top-class type in July.
As a result, CO2 emissions were reduced by about 7.2 tons per year, and energy consumption decreased by approximately 16,118.4 kWh per year.
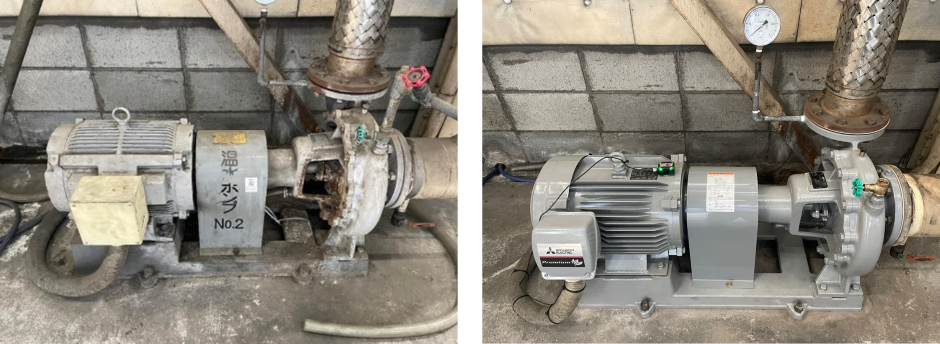
Gifu Plant
AC Unit Update
The multi-zone air conditioner units that were used in the offices, cafeteria, and meeting rooms was replaced with a high-efficiency unit in October due to age. As a result, CO2 emissions were reduced by about 21.0 tons per year, and energy consumption decreased by approximately 12.0 kL of crude oil per year.
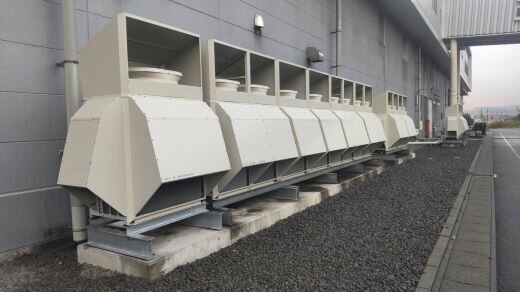
Green Energy Purchase
Starting in November, the Gifu plant entered into a contract to purchase 20% of the energy it uses as CO2-free green energy each month. As a result, annual CO2 emissions were reduced by 165.0 tons.
Mie Plant
Updating HVAC Equipment
The construction of 12 AC units for Grinding Factory 1 was completed in December. As a result, CO2 emissions were reduced by about 58.0 tons per year, and energy consumption decreased by the equivalent of about 49.7 kL of crude oil.
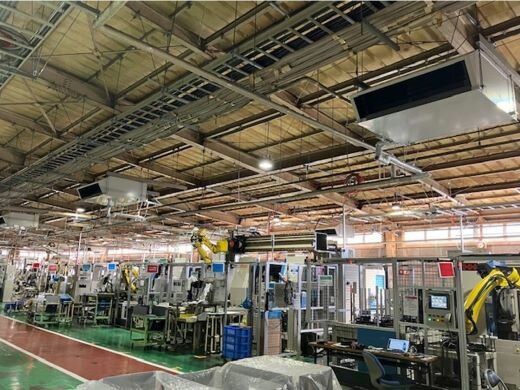
Application of Insulating Film
Insulating film was applied to the southern window of Grinding Factory 1 in August to reduce the energy cost of the AC units. As a result, CO2 emissions were reduced by about 4.5 tons per year, and energy consumption decreased by the equivalent of about 2.9 kL of crude oil.
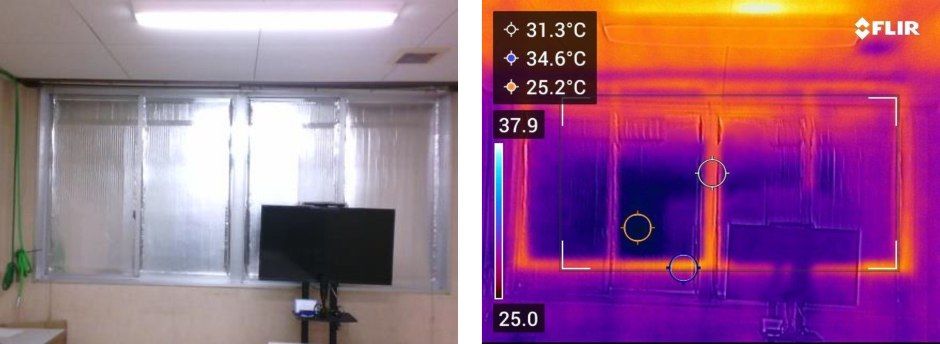
Shot Machines Upgraded
In May, two of the shot machines used in the shot process of the heat treatment plant were changed from compressor types to impeller types to reduce the energy usage from the compressors. As a result, CO2 emissions were reduced by about 12.4 tons per year, and energy consumption decreased by the equivalent of about 8.2 kL of crude oil.
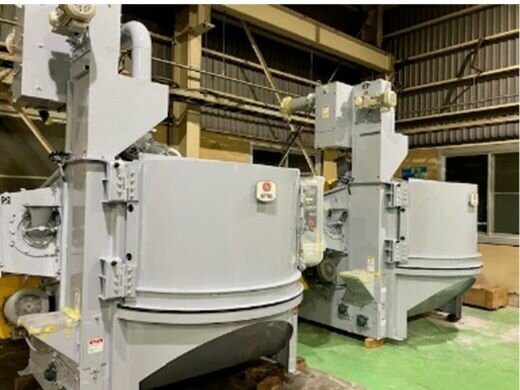
Upgraded Heater
The heater in one of two vacuum carburizer furnaces used in the heat treatment process was replaced in March. As a result, CO2 emissions were reduced by about 4.9 tons per year, and energy consumption decreased by the equivalent of about 3.2 kL of crude oil.
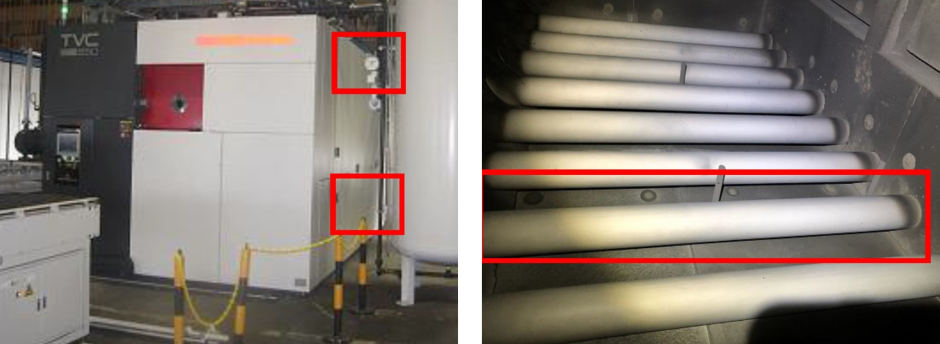
Yamaguchi Plant
Upgraded Air Conditioners
The package air conditioner used in the Production Engineering Department’s measurement room at the Technical Plant was upgraded to a high-efficiency type in May. As a result, CO2 emissions were reduced by about 0.42 tons per year, or the equivalent of about 0.2 kL of crude oil.
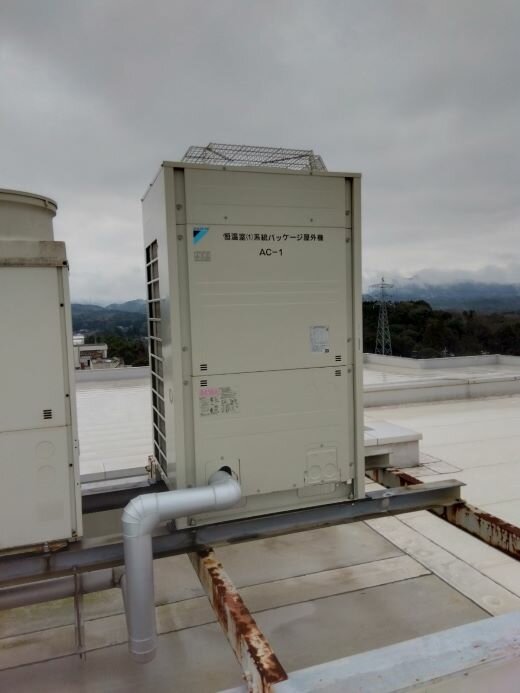
THK NIIGATA
Water Chiller Set Temperature
The water chiller temperature used for the air conditioning in the Factory 3 first floor thermostatic chamber was changed from 9°C to 12°C during the winter, when the load on it is lighter. As a result, CO2 emissions were reduced by about 6.0 tons per year, or the equivalent of about 3.4 kL of crude oil.
Insulating Coating
In May, an insulating coating was applied to two of the Factory 1 outdoor package air conditioner units to reduce energy consumption during the summer. As a result, CO2 emissions were reduced by about 0.7 tons per year, or the equivalent of about 0.4 kL of crude oil.
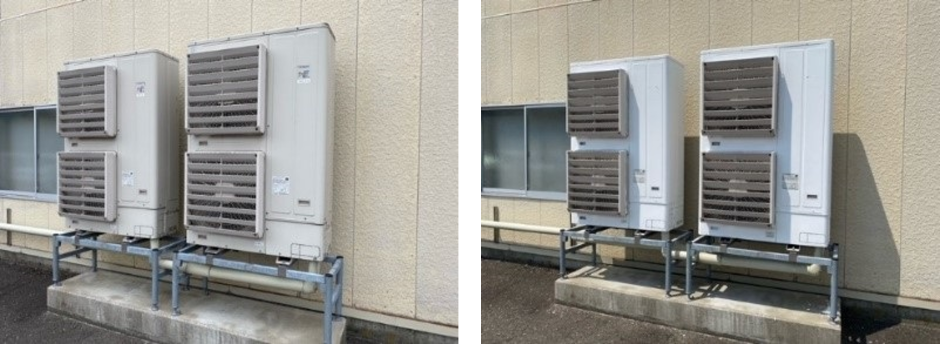
Installation of Static Electricity Removal Sheet
Static electricity removal sheets were installed onto the ceiling cassette type air conditioners on the second floor of Factory 3 to reduce energy consumption. As a result, CO2 emissions were reduced by about 4.8 tons per year, or the equivalent of about 2.5 kL of crude oil.
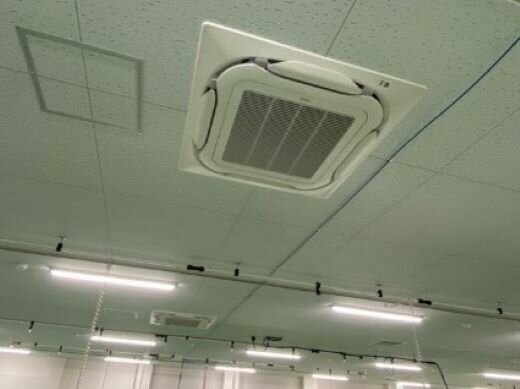
THK RHYTHM Hamamatsu Plant
Upgraded Compressors
As a result of upgrading the two 75 kW inverter compressors used in the compressor room to high-efficiency types in September, CO2 emissions were reduced by about 15.2 tons per year, or the equivalent of about 10.1 kL of crude oil.
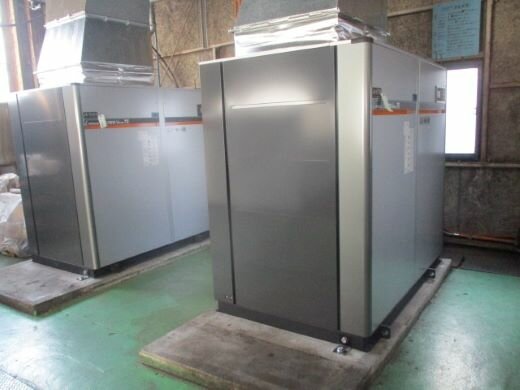
Upgraded Steam Boiler
The 1.2-ton LPG steam boiler used in the cationic coating process was upgraded to a high-efficiency type in May. As a result, CO2 emissions were reduced by about 4.2 tons per year, or the equivalent of about 1.8 kL of crude oil.
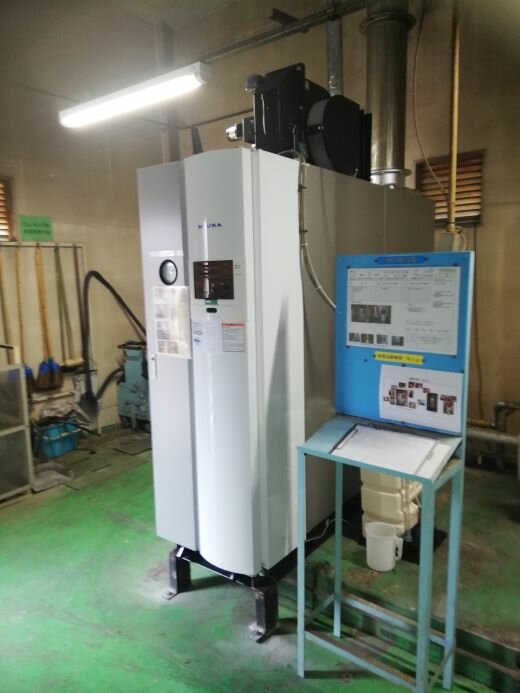
Installing Insulation
Insulation was installed in the aluminum-melting furnace used in the aluminum stabilizer shank casting process in March to reduce heat radiation. As a result, CO2 emissions were reduced by about 21.6 tons per year, or the equivalent of about 9.5 kL of crude oil.
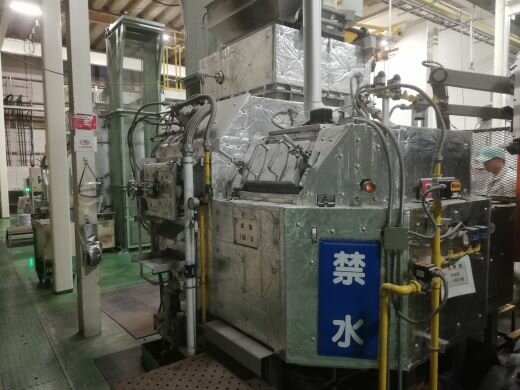
Kyushu Plant
Upgraded Cargo Elevator
Due to its age, a cargo elevator was upgraded to a high-efficiency type in July. As a result, CO2 emissions were reduced by about 0.5 tons per year, or the equivalent of about 0.2 kL of crude oil.
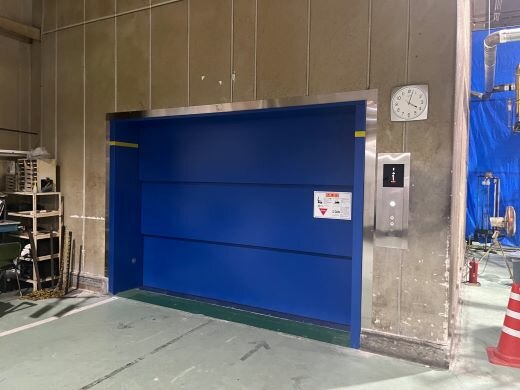
Wuxi Plant
Addition of Inverter Function
An inverter function was added to the mist collectors of over 133 machines in the grinding, block rough processing, and rail rough processing areas throughout the year, and the required air volume was set for each. As a result, CO2 emissions were reduced by about 213.0 tons per year, or the equivalent of about 80.0 kL of crude oil.
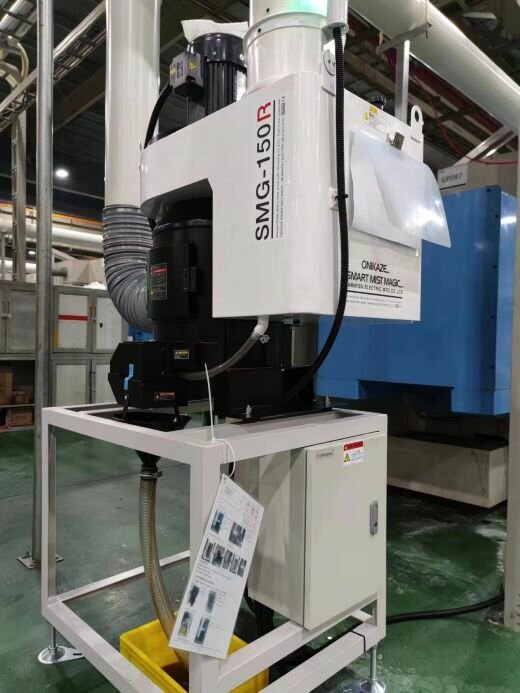
Change to Inverter Type
The hydraulic equipment on 10 machines in block rough processing was changed to an inverter type in December. As a result, CO2 emissions were reduced by about 10.6 tons per year, or the equivalent of about 4.0 kL of crude oil.
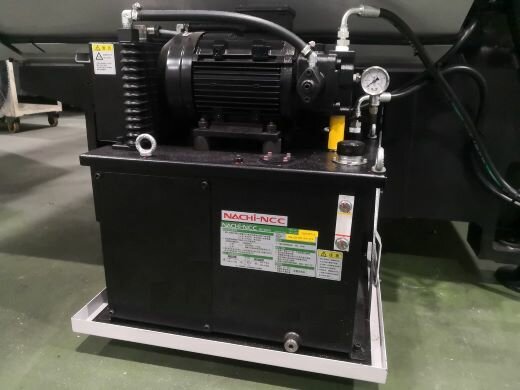
Line Automation
The first and second rail grinding production lines were automated in August. This led to a drastic reduction in the amount of time the lights were on. As a result, CO2 emissions were reduced by about 21.7 tons per year, or the equivalent of about 8.2 kL of crude oil.
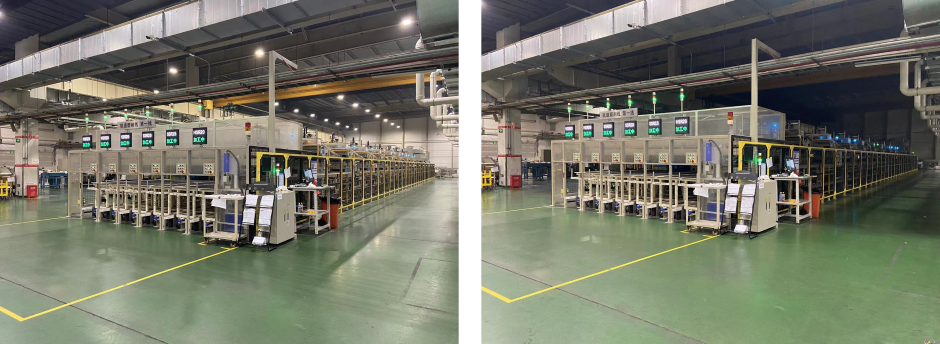
TME (France)
Installation of Variable Speed Compressors
In October, two variable speed compressors with central control were installed to supply air pressure for all manufacturing processes. The condition of the previous equipment has deteriorated, so this was done in consideration of supplying air to future planned equipment. As a result, CO2 emissions were reduced by about 88 tons per year, or the equivalent of about 43.2 kL of crude oil.
TMA (USA)
Daily Inspections
Seventy-four air leaks were repaired throughout the year, and the air compressors were shut off when not running for production. As a result, CO2 emissions were reduced by about 121.0 tons per year, or the equivalent of about 30.2 kL of crude oil.
TRA Gellep (Germany)
Change to Electric Forklifts
Ten forklifts were gradually changed to electric models beginning in January. As a result, annual CO2 emissions were reduced by 41.3 tons.
Utilization of Electric Vehicles
One company vehicle was changed to an electric vehicle in January. As a result, annual CO2 emissions were reduced by about 0.6 tons.
Daily Inspections
Compressor air leak inspections were conducted throughout the year. As a result, annual CO2 emissions were reduced by about 12.3 tons.
Green Distribution
THK RHYTHM Hamamatsu Plant
Beginning in June for products shipped to THK locations outside of Japan, the transportation method for delivery to Kitakyushu was changed from truck to mixed cargo shipping on trains. As a result, annual CO2 emissions were reduced by about 366.0 tons.
Efforts at Each Facility
THK is proactively expanding its installation of renewable energy equipment at its production facilities. In 2023, solar panels were installed at the facilities below.
Yamagata Plant
Solar panels were installed at Factory 1 in February utilizing a PPA (power purchasing agreement). As a result, they were able to reduce CO2 emissions by about 1024.6 tons per year and energy consumption by about 695.0 kL of crude oil per year.
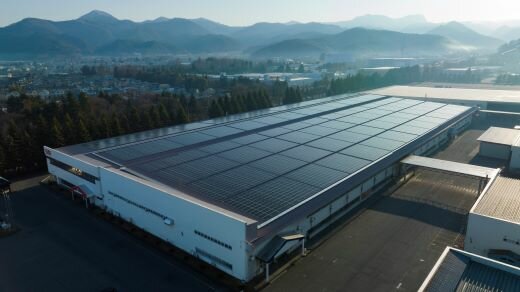
THK NIIGATA
Solar panels were installed at Factory 4 in October utilizing a PPA. The plant consumed 100% of the energy it generated, but this enabled them to reduce CO2 emissions by about 236.4 tons per year and energy consumption by about 133.0 kL of crude oil per year.
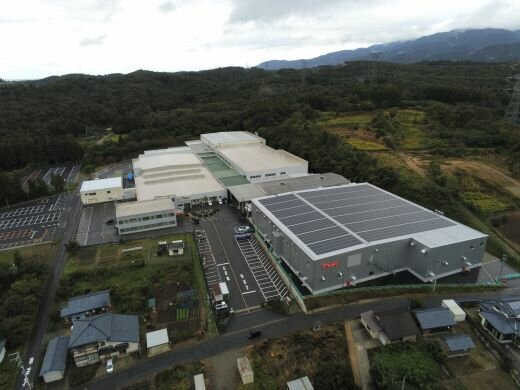
Liaoning Plant (China)
Solar panels were installed at third plant at THK LIAONING (CHINA) in April. The generated energy was about 7.9% for whole plant electric consumption and 100% consumed in the plant. As a result, they were able to reduce CO2 emissions by about 1,834.6 tons per year and energy consumption by about 236.0 kL of crude oil per year.
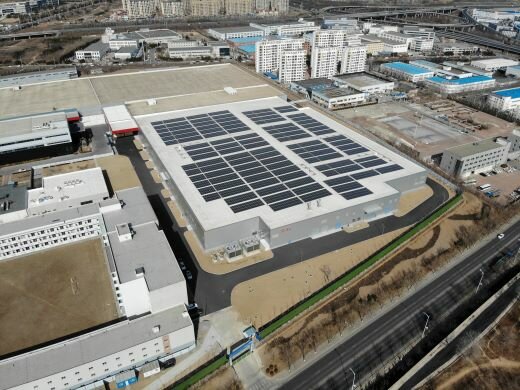
TRTC Plant (Thailand)
Solar panels were installed over the entire roof of the factory at THK RHYTHM (THAILAND) in January. The plant consumed about 87% of the energy it generated and sold the remaining approximately 13%. As a result, they were able to reduce CO2 emissions by about 420.7 tons per year and energy consumption by about 202.9 kL of crude oil per year.
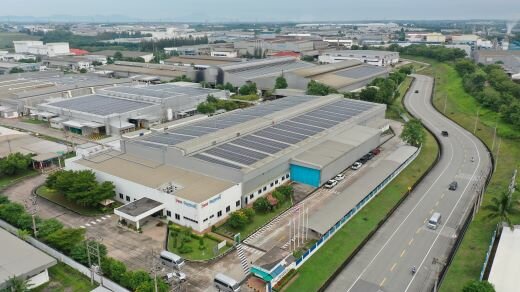