DX Promotion and Planning
Omni THK
We are continuously developing and promoting Omni THK as a core tool that enables employees to devote more time to work with high added value by deepening our relationships with customers (restructuring the user experience) and utilizing automation to reduce the amount of time spent on routine tasks.
We are merging member profiles previously spread across multiple services, developing applications that improve customer convenience and help digitalize customer movement, and promoting the fusion of in-person and digital methods.
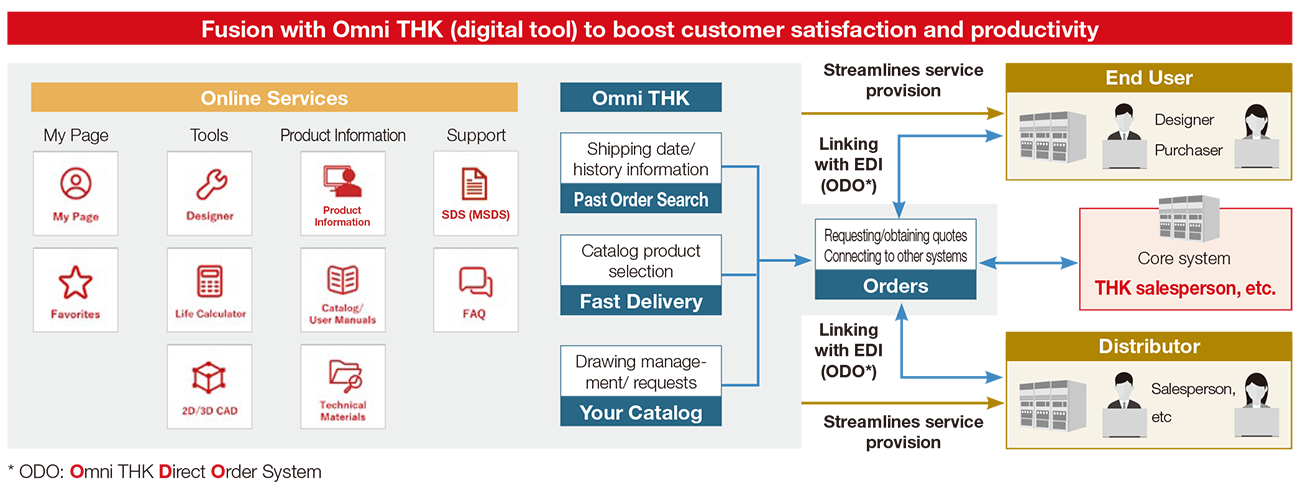
OMNIedge
Realizing early on that the IoT was an effective technology for solving social challenges such as labor shortages and the need to boost productivity in the manufacturing industry, THK has been developing solutions to advance the adoption of the IoT worldwide. can be retrofit onto equipment in use for quick IoT integration. Since its launch in 2020, we have developed four versions of this service and a connected tool. In order to actively promote new business in concurrence with the first release phase, we established our new IOT Innovation Division to replace our previous framework of conducting interdepartmental projects. We will continue to introduce solutions—not only for our own peripheral equipment, but for the greater market as well—that will minimize and reduce various types of efficiency loss on the production
floor and improve overall equipment effectiveness (OEE).
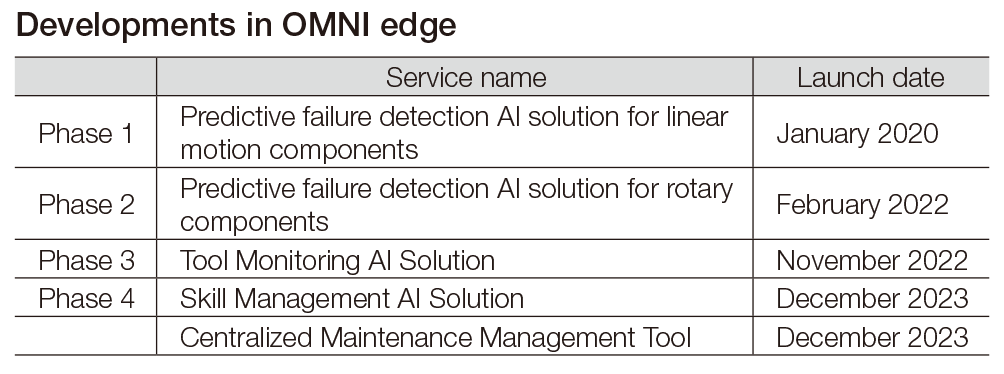
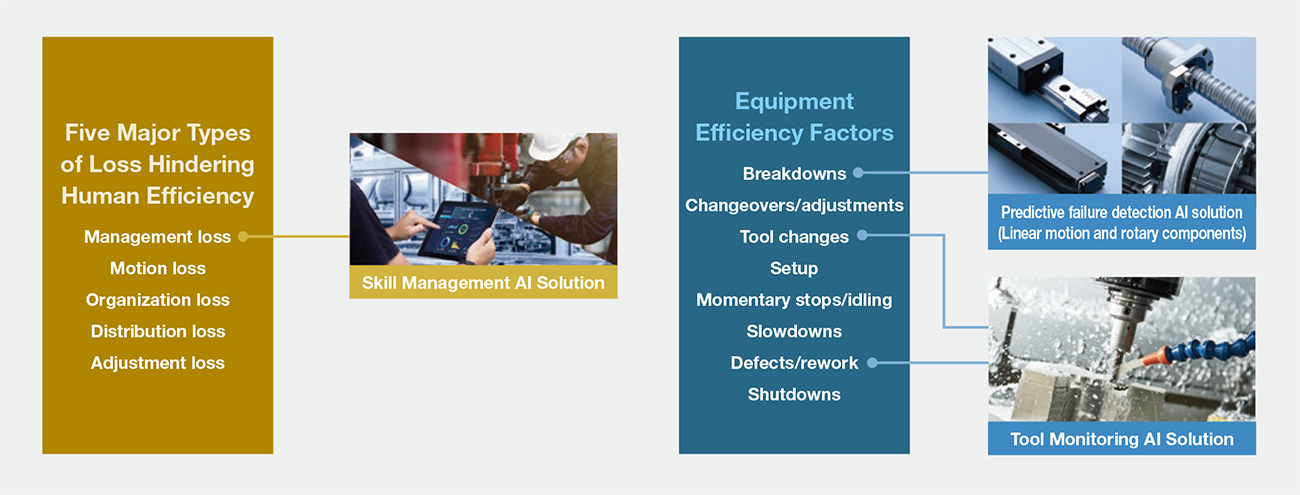
Developing Digital Talent and DX Tools
THK is also putting effort into the development of the “DX talent” that constitutes the driving force behind our DX activities. At the same time, we are promoting digital tools and performing data maintenance so that the production floor can utilize that data more independently. Our robotic process automation (RPA) has even won awards from outside competitions.
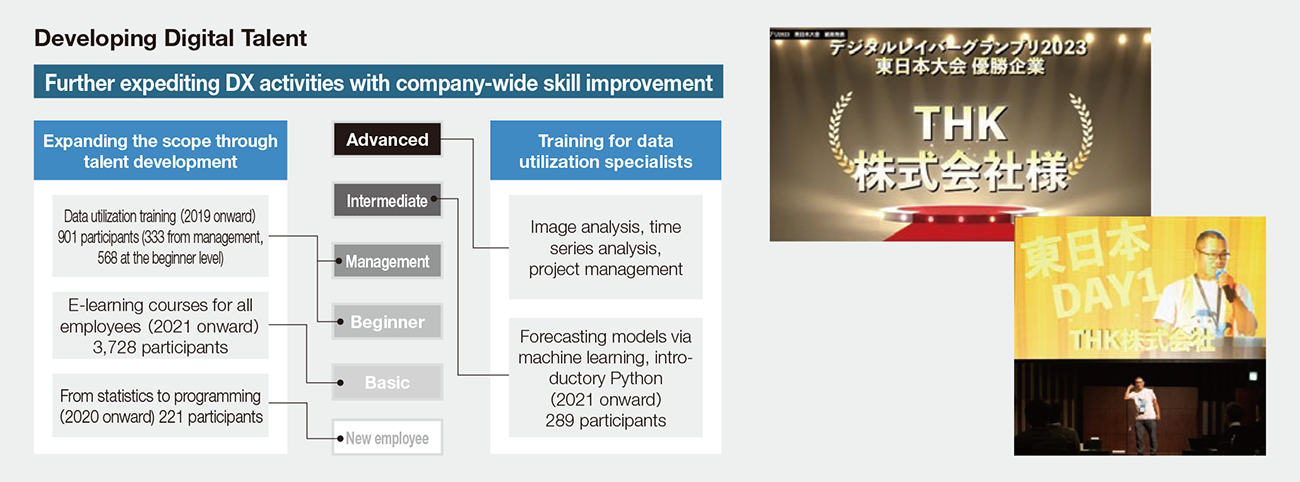
Production Division
The Production Division embarked on its Smart Factory project in 2023, and it has developed a variety of digital solutions since then. Through this initiative, they continue to promote innovations to the 5M production process and ongoing quality and productivity improvements.
Current Solution Structure to Achieve a Smart Factory
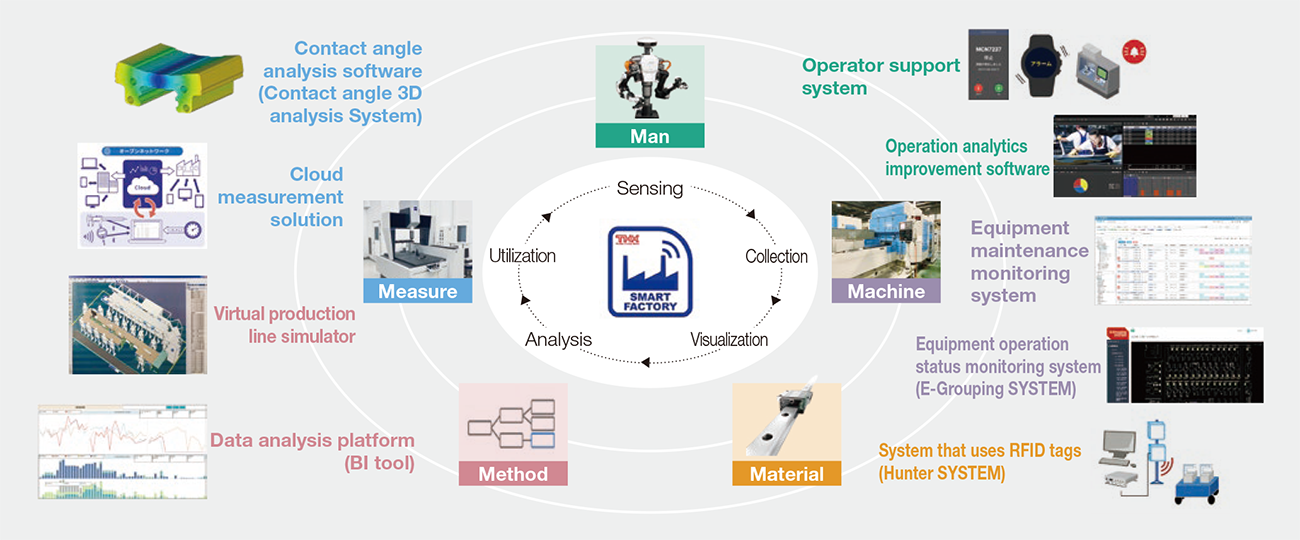
Main Digital Solutions
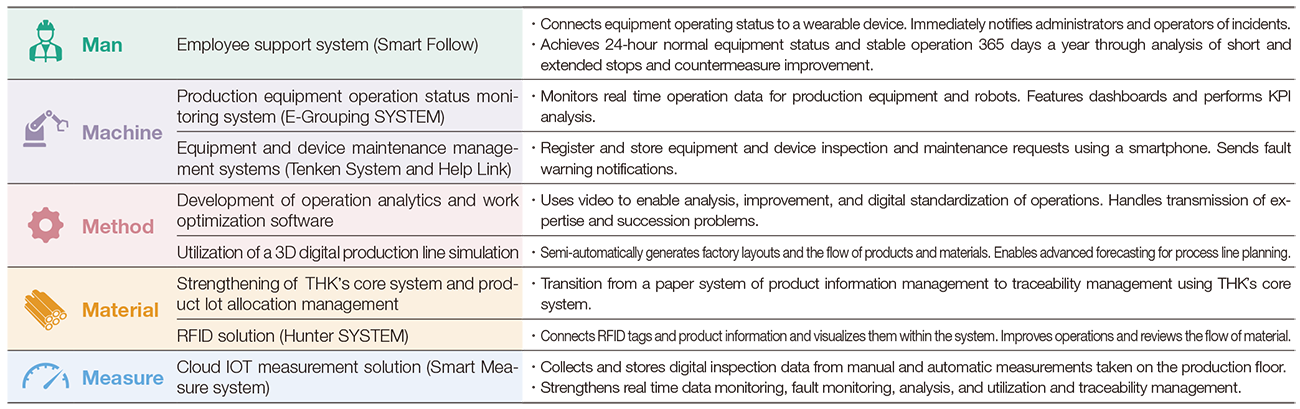