Message from the Chairman and CEO
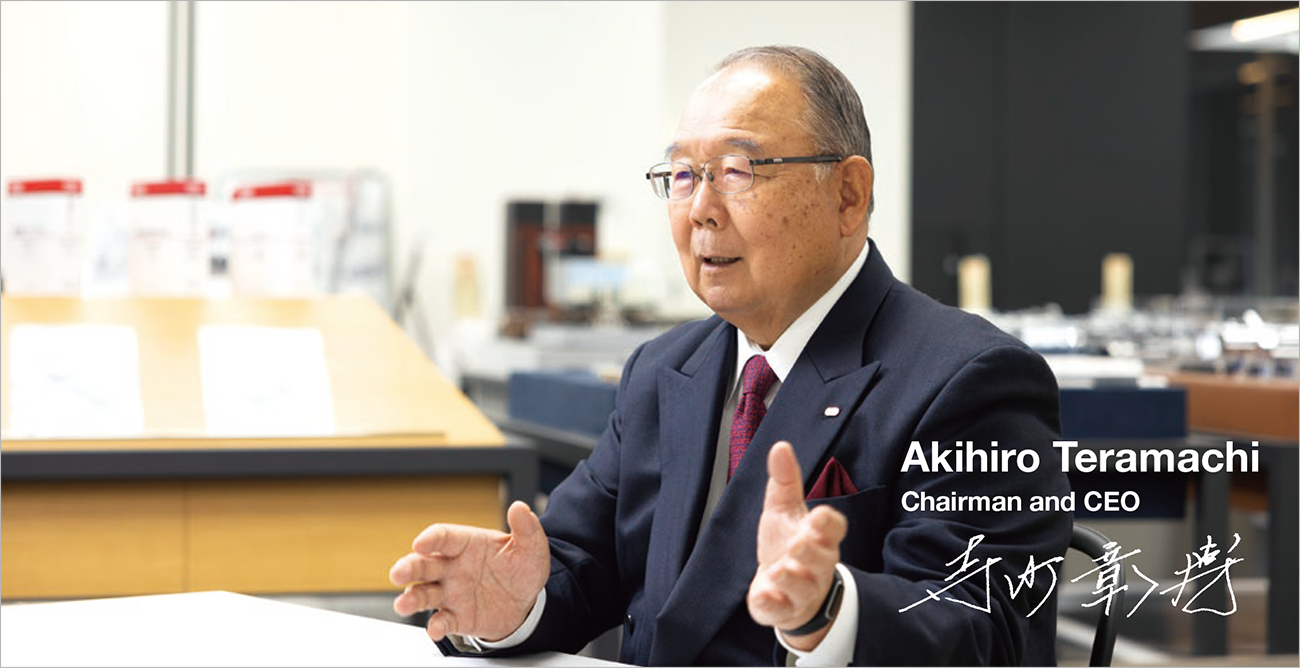
Rapidly Creating Value as a Manufacturing and Innovative
Services Company on a Global Scale under a New Structure
Introduction
I would like to express my sincere condolences for the lives that were tragically lost and to everyone in the region affected by the Noto earthquake that struck at the start of 2024.
We provided a donation to the Japanese Red Cross at the beginning of January, and we sincerely hope that it will aid the speedy recovery of the affected areas in some small way.
Selecting Our New President
At the November 2023 Board of Directors Meeting, we made the decision to have then-Director and Senior Managing Executive Officer Takashi Teramachi assume the role of Representative Director, President, and COO, while I assumed the role of Representative Director, Chairman, and
CEO. This new structure took effect on January 1, 2024.
Our new President Teramachi has been promoted to this position at the age of 45. Reflecting on my own experience, I was also 45 when I became the president, but I felt that I had been prepared for management through the previous work innovations that I had spearheaded. In addition to leading our organization while serving as the president of a subsidiary and heading the industrial machinery business, our new
President Teramachi has been responsible for promoting DX (digital transformation) and GX (green transformation), and this work has prepared him for his role in steering us into a new era. In fact, as I would discuss the future of our operations with him, it became clear what our key strategies must be, and he demonstrated a desire to drive innovation and adapt to our changing environment. That was why I decided
this was the time to pass the torch to the next generation, and after I investigated the matter and held deliberations with the Nomination Advisory Committee, our new President Teramachi was selected for this position at the Board of Directors Meeting. I will continue to support our new structure in my capacity as CEO.
My hope for this new structure is that we will continue to preserve the good things we have adopted over the years while also boldly evolutionizing to adapt to the changing times. It is especially imperative that we further our globalization efforts. I personally spend about 130 days each year abroad, and I want our young Japanese employees to turn their gaze outside of Japan to a much greater degree as well. To this point, our new President Teramachi truly feels the importance of having a global mindset from his experience traveling around to different parts of the world during his time working at a large trading firm. I hope that he will take the lead in combining the strengths of our next-generation employees to turn THK into a more global organization.
Reflecting on the 2023 Fiscal Year Results
2023 was the second year we spent in pursuit of our 2026 management targets. As a result of a business environment that included global turmoil, demand recovered at a rate that lagged behind our expectations. It appears that demand struggled to expand as capital investment that was expected to kick off in the automotive industry was delayed, and investment in ICT (information and communication technology) arising from stay-at-home demand during the coronavirus pandemic had already progressed.
As this environment led to shrinking demand in our industrial machinery business, which constitutes approximately 60% of our revenue, we were able to secure revenue during the first half of the year due to our backlog of orders, but our demand failed to recover in the second half. As for our automotive and transportation business, which represents the remaining 40% of our revenue, we saw recovery in demand as the pandemic ended and component shortages were mitigated.
In terms of profit, although we continue to work on various improvements to increase productivity, decreased revenue primarily in our industrial machinery business resulted in a higher cost-to-sales ratio. Furthermore, as we emerged from the pandemic and implemented growth measures at full force, our SG&A ratio also increased.
As a result, our consolidated revenue in 2023 decreased 10.6% year on year to ¥351.9 billion, and our operating income decreased 31.2% year on year to ¥23.7 billion. Although the aforementioned delay in demand recovery forced us to make a downward adjustment to our earnings forecast in August, we were able to achieve those adjusted targets.
In terms of the outlook for 2024, if the level of geopolitical risk settles down, we expect to see the recovery in demand that we had anticipated. The main theme will be shifting from “global” to “glocal.” As the supply chain in the semiconductor and other industries becomes more fragmented, there is an emerging need to make capital investments within each economic bloc. While investment was focused on the construction of buildings in 2023, investment in the equipment that goes inside those buildings will ramp up in 2024 and beyond, becoming a driver of growth in our earnings.
Growth Strategies
The pillars of our growth strategy are full-scale globalization, the development of new business areas, and a change in business style. In accordance with these themes, we pursue our vision of a revolutionary transformation into a manufacturing and innovative services company. We have always provided customers with the means to manufacture goods through our linear motion and other products, but we are
now expanding our service offerings to include everything from before to after the sale. In this way, we are developing an all-inclusive business package that fuses hardware and software. This will allow us to expand our points of contact with customers to include both machine builders and actual machine users so that we can bolster our ability to contribute to their businesses.
In 2024 and beyond, we will focus on accelerating our efforts related to our growth strategies more than ever before. By taking the initiative in responding to and proposing solutions for our customers’ needs, we hope to deepen their trust in us and form closer partnerships with them based on higher levels of expectation.
The key focus of our industrial machinery business is achieving true automation and building systems that allow production equipment to operate independently. True automation means there won’t be any people around to make minor adjustments, so it carries the risk of sudden machine stops causing significant losses. That is why we will propose solutions that can detect malfunctions before they happen through sensors installed inside equipment. In addition to enabling predictive maintenance, such IoT services help customers reduce loss that occurs on the production floor, curb energy consumption, and decrease CO2 emissions. The combination of these services with an expansion of our linear motion products, which reduce the use of electricity and lubricant, will heighten our ability to contribute to sustainability. At the same time, we are pouring effort into developing products that meet the cutting-edge needs of various industries, such as providing nanometer-level precision for semiconductors and compact, highly rigid offerings for machine tools.
Propelled by CASE in our automotive and transportation business, we will accelerate the development of linear motion products for automobiles and strengthen our efforts related to electric vehicles, which are a major trend around the world. Having experienced the comfort and joy of electric vehicles myself, I don’t think I’ll ever go back to a gasoline-powered vehicle. As we demonstrated with the unveiling of our original EV prototype, the LSR-05, at Japan Mobility Show 2023, we hope to support the efforts of automotive manufacturers around the world to transition to electric vehicles by proposing technology and products that will increase their value. This includes providing lightweight, compact components to make car interiors more comfortable and revolutionizing charging systems to shorten charging times and increase
driving distances.
Furthermore, we will strengthen the synergy of our industrial machinery and automotive and transportation businesses through increased collaboration. Even in 2023, we increased our profits via structural collaboration by redistributing industrial machinery-related work to some of our automotive-related production lines. In addition to further expanding such efforts, we will also strengthen collaboration among our engineering and development groups.
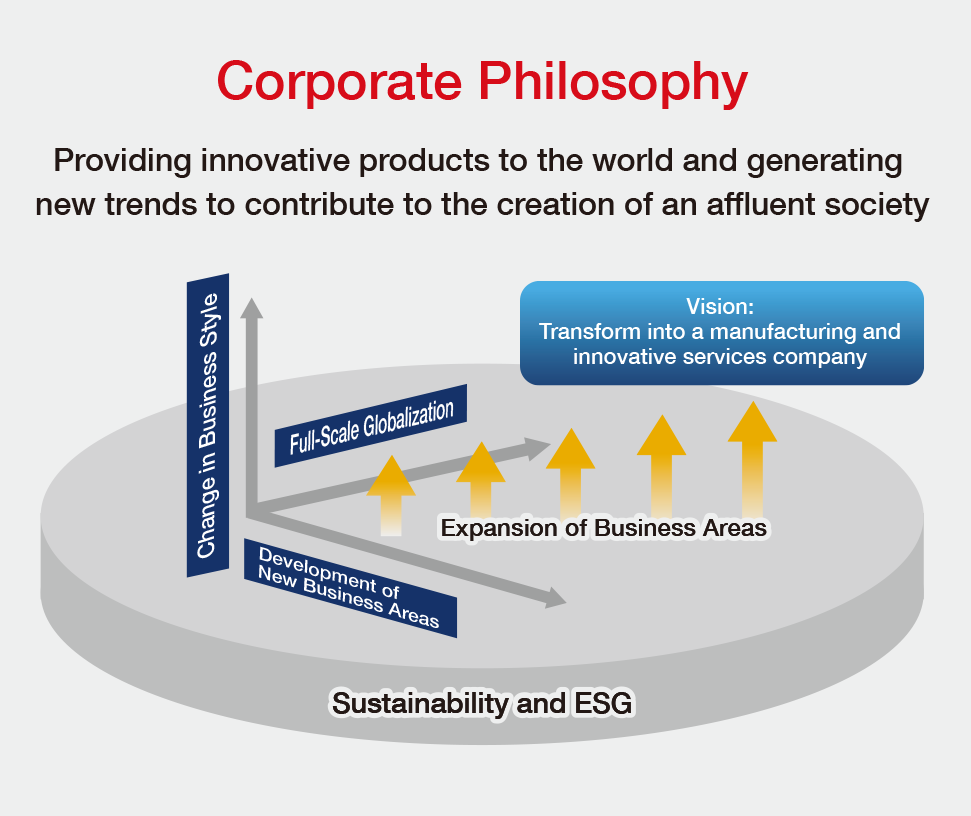
Talent Development
Digital talent will be the key to our transformation into a manufacturing and services company. In this era where digital technology is permeating every aspect of society, even as we work to provide products and services that support the DX activities of our customers, we are also promoting DX within our business practices and putting effort into developing digital talent that will drive such initiatives.
For our corporate and other support departments in particular, we need to develop the knowledge and capability to use data at a more advanced level, which includes identifying how to use what kinds of data and distinguishing tasks that humans should do from tasks that can be left to AI and other digital tools.
At the same time, we can’t say that digital talent is needed in every position. For instance, when it comes to our employees involved in production at our factories, I believe there are three paths forward. The first is to hone their skills and expertise, to thoroughly pursue artisan-level technique regardless of cost. The second is the path of looking into how we manufacture things, of taking the skills honed by people in that first category and incorporating them into the recipe that will deliver products at a market-friendly price to customers around the world. Finally, the third path involves achieving production lines that can flexibly mass-produce that recipe within a limited timeframe. People who choose this path will require knowledge similar to that of data scientists in order to achieve fully automated production lines that can operate
steadily even with low staffing levels.
Similarly, even as we work to make our sales operations more effective by utilizing virtual meetings and digital tools such as chatbots, there are occasions where we must value face-to-face communication, such as when generating ideas for new business. It will be critical to determine the needs of the other party and combine both digital and in-person methods.
In this way, even as we recognize the importance of digital tools, we intend to develop a workforce of diverse individuals who have a flexible perspective and won’t rely too heavily on digital tools. By promoting the utilization of the right people in the right positions, we aim to eighten the entire organization’s ability to generate value.
A Message to Our Stakeholders
We deeply appreciate the daily support and guidance we receive from our shareholders, investors, and other stakeholders, and we always consider how to maximize everyone’s returns from the success of our business.
As part of our efforts, we have emphasized PBR in recent years as a metric that the public is concerned with. Out of our belief that increasing ROE is an effective way to improve our corporate value, we have set one of our 2026 management targets as an ROE of 17%. To achieve this milestone, it is critical for each of our business segments to increase their ROIC, particularly by bolstering their returns (profit levels), which
form the numerator of that equation. Therefore, to accelerate the efforts of each division, we must invest in future growth by applying funds to capital investments, research and development, and human investments. Taking this capital demand into consideration, we consider it appropriate to maintain a payout ratio of 30% for the present time. In the event that we have surplus capital as we move forward in this direction, we will strive to give more back to our stakeholders by actively considering stock buybacks.
Many prototypes are developed in the process of making our products ready for mass production and adoption, and it inevitably takes time before our labor comes to fruition in the form of profit. However, the product that we deliver to the customer will continue to work and generate value for a long time. Due to the nature of our business, we have naturally developed a long-term perspective that looks 10 to 20
years in the future rather than chasing after short-term profit. I am confident that this strength will also carry us through this uncertain and unpredictable time. In anticipation of the future state of society, we have been transforming into a manufacturing and innovative services company and working on other initiatives to lay a groundwork that is showing sound indications of future growth. I hope that all of our stakeholders will continue to support us with a long-term perspective in mind.