Health and Safety
The Whole Company Policy
- Prevent health hazards and promote healthy practices
- Create a safe and comfortable working environment
Goals
- Perform 100% of legally mandated health checks
- Prevent new cases of extended leave caused by injury and illness
- Reduce rate of health findings
- Zero workplace accidents
Five THK Production Facilities (Yamagata, Kofu, Gifu, Mie, and Yamaguchi)
Policy
- We consider the improvement of occupational health and safety to be one of the most important issues for the Production Division, and as we conduct our business activities at each factory, we promote the creation of a safe, healthy, and comfortable workplace by eliminating harmful work environments that may lead to injury or illness.
- We continuously improve our health and safety management system by setting appropriate occupational health and safety goals at each factory and reviewing them annually.
- We strive to improve occupational health and safety by complying with laws such as the Industrial Safety and Health Act and rules relating to occupational health and safety established by the company and workplace.
- Each facility eliminates hazards and causes of harm in the workplace through risk assessments and promotes activities with the goal of completely eliminating all potential hazards.
- Each facility promotes the occupational health and safety management system with the active participation and consultation of all employees.
- We acknowledge that the occurrence of accidents and injuries is a direct reflection of the nature and culture of the workplace, and we promote activities to develop correct habits through the use of the occupational health and safety management system.
- This occupational health and safety policy is disseminated to all employees at each plant through education, training, and awareness campaigns, and we facilitate the timely release of information relating to occupational health and safety within and outside the Production Division.
Health and Safety Management Structure
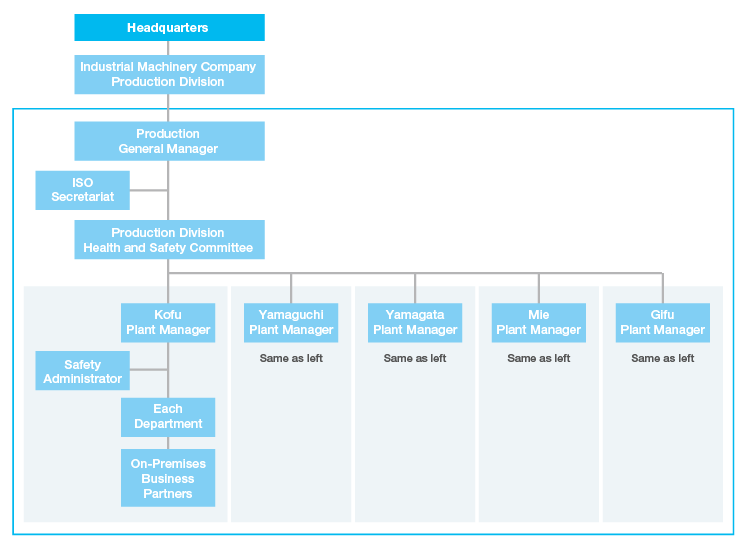
Activities and Results (Including Goals)
2023 Activities Report (Headquaters)
Annual plan |
Details |
Result |
Convening the Health Committee |
Committee members selected from each department perform audits,give reports, and deliberate on health-related issues. |
Meetings were held each month, a total of 12 times. |
---|---|---|
Workplace patrols (once a week by health supervisor and on even-numbered months by industrial physician) |
Performed in each workplace at the headquarters to check for health and safety issues. |
45 health supervisor patrols |
Performing work environment measurements |
Measured air quality in each workplace. |
Performed during even-numbered months, a total of 6 times. |
Performing stress checks and responding with countermeasures |
Conducted a simple new online survey of work-related stress. |
The survey was conducted in August and had a 99.9% participation rate. |
Performing health checks and responding with countermeasures |
Physician visited to perform internal health checks. Consulted with the industrial physician and insurance staff about high-risk individuals and implemented work restrictions for these individuals. |
100% of employees received health checks. |
Administering influenza vaccines |
Offered an opportunity internally for employees to be vaccinated. |
Over three days in October, 61% of employees received vaccinations. |
Health education |
Posted advice from the industrial physician and a health office newsletter on bulletin boards. |
Posted each month company-wide, a total of 12 times. |
Holding health promotion events |
Planned around a theme selected from the results of the health checks (including questionnaires). |
A walking event was held using an app in December, in which 174 people participated. |
Preparing traffic safety measures and holding a traffic safety event |
Held a training conference for safe driving supervisors at THK Japan and Group companies in Japan. |
The conference was held online in February for 46 participants. |
2023 Activities Report (Five THK Production Facilities)
Annual plan |
Details |
Result |
Prevent work-related injuries and illnesses |
1.Performing risk assessments |
Conducted for each department at each production facility. |
---|---|---|
2.Conducting workplace health and safety training |
Conducted training at each production facility based on training rules. |
|
3.Implementing hazard prediction training and soliciting proposals to prevent near-miss events |
Implementation rate: 87.5% for hazard prediction trainings and 97.7% for near-miss event prevention proposals |
|
Continuously improve occupational health and safety performance |
4. Communicating and managing up-to-date regulations (Performing chemical substance risk assessments) |
An outside specialist was invited every month to hold a special meeting to go over changes to laws and regulations. This information was then distributed to each production facility. Chemical substance risk assessments are being performed according to the rules of each plant. |
5.Promoting Health and Safety Committee activities |
Committees convened monthly at each production facility, in accordance with Health and Safety Committee rules. |
|
6.Performing internal audits and management reviews |
Performed in accordance with relevant regulations. |
|
7.Implementing traffic safety activities |
Each production facility implemented activities on a voluntary basis. |
|
8.Conducting workplace safety patrols |
Patrols were conducted according to each production facility’s implementation schedule. |
|
Provide a safe and healthy workplace |
9.Addressing mental health |
Mental health was addressed following a directive from the headquarters. |
10.Receiving guidance from industrial physicians and implementing disease prevention activities |
Performed at each production facility. |
|
11.Performing regular and special health checks |
Performed at each production facility |
|
12.Managing long work hours (excessive overtime) |
Performed at each production facility. |
ISO 45001 Initiatives
Having obtained ISO 45001 occupational safety and health management system certification, THK pursues the activities listed in the preceding table while following the PDCA cycle for the annual plan. Our 2023 results included 12 labor accidents (4 that were lost-time accidents and 8 that were not), meaning that we could not reach a new accident-free record.
Chemical and Hazardous Material Handling
In the interest of strengthening our chemical handling structure in keeping with partial amendments to the Ordinance on Industrial Safety and Health and other regulations, THK conducted a review of its chemical handling rules and an overall review of its chemical risk assessment rules in accordance with the amended laws and regulations. This has resulted in even stronger chemical handling management at each production facility than existed previously.
Responding to Community Complaints (Noise, Etc.)
Mie Plant
- Heat Treating Factory 3 received a community complaint about the noise generated by running its equipment. The plant is moving forward with installing soundproof walls.
- In early November, we received complaints from members of the surrounding community that lights were shining into their entryways, living rooms, and other areas of their homes at night. In response, the plant switched 70% of its lights to energy-saving mode and set them to shut off at 8:00 p.m.
Responding to Employee Needs (Providing Protective Equipment and Ensuring Safety of Machines and Equipment)
We provide all protective equipment required for production operations (such as safety glasses, ear plugs, dust masks, and cut-resistant gloves). Furthermore, safety fences are put in place to ensure safety where automated equipment has been installed.
Incident and Severity Rates
2021 | 2022 | 2023 | |
---|---|---|---|
Incident rate | 1.43 | 0.88 | 1.49 |
Severity rate | 0.02 | 0.02 | 0.00 |
Applicable locations:
Five THK manufacturing plants (Yamagata Plant, Kofu Plant, Gifu Plant, Mie Plant, and Yamaguchi Plant)
Group company manufacturing plants (THK NIIGATA; THK INTECHS Sendai and Mishima; THK RHYTHM Hamamatsu, Inasa, and Kyushu; and NIPPON SLIDE)
Efforts at Each Facility
Yamagata Plant
Training
In September and November, members of the Higashine Fire Department were invited to conduct CPR and AED training for a total of 111 employees from positions of Group Leader and above and members of the first responder team.
Kofu Plant
Presenting Examples of Workplace Excellence
The 2023 Yamanashi Prefecture Industrial Safety and Health Conference was held in October at the Yamanashi Prefectural Museum of Literature. During the event, the Kofu plant received the 2022 Workplace Excellence Encouragement Award from the Yamanashi Labor Bureau and gave a presentation on “Risk-Aware Occupational Health and Safety Initiatives” to share examples of that workplace excellence.
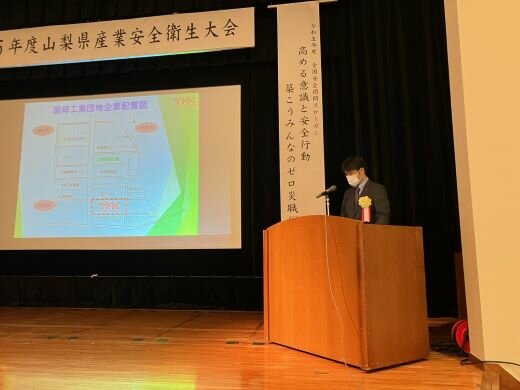
Gifu Plant
The plant participated in the 2023 Seino STOP! Falling Accidents Project and received an award from the Ogaki Labor Standards Inspection Office in December for being a company that took proactive measures to prevent falling accidents and avoided labor accidents that would have resulted in four or more days of lost time.
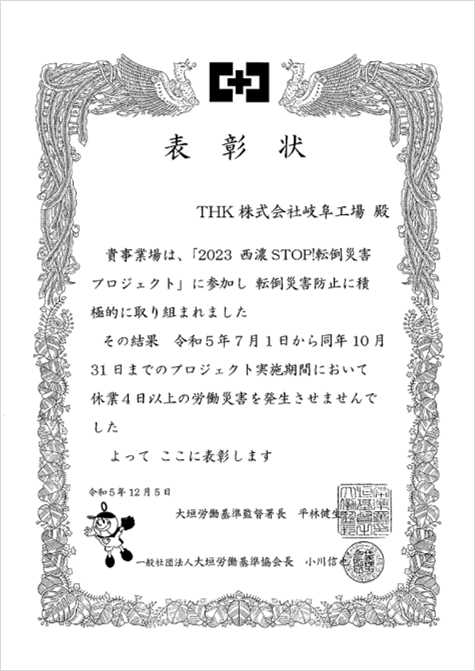
THK NIIGATA
VR Training Implemented
In September, training for fatal forklift accidents, tripping accidents, accidents caused by distracted driving due to cellphone use, and night-time right-turn accidents was performed using VR devices brought in by an external partner for forklift operator safety training. Because the content of the VR training included automotive traffic accidents, the scope of participants was expanded to include management and new employees in a training held in October, bringing the total number of participants to 38.
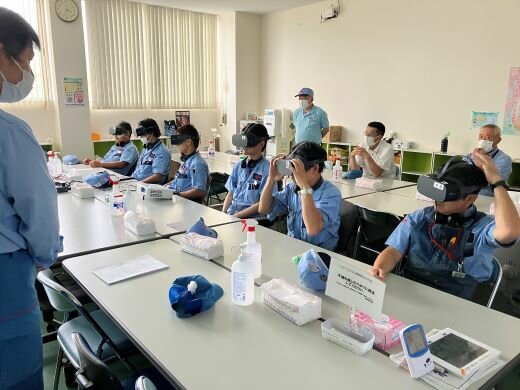
Wuxi Plant (China)
Training
An external consultant was invited to conduct a safety-related seminar for 65 members in September that covered (1) an overview of China's Production Safety Law, (2) the intent of the production safety standards, (3) self-evaluation items, (4) evaluation methods, (5) steps to certification, and other requirements for obtaining Class 3 production safety standard certification. As a result, the plant was able to obtain certification as a Class 3 production safety standard-compliant company.
Two traffic safety seminars were also conducted by an outside consultant for 43 members in April and September, covering (1) danger spotting methods, (2) traffic accident examples, (3) safety precautions for electric bikes, (4) safety precautions for drivers, and other topics.
TMA (USA)
A Safety Dojo was created in August to increase safety consciousness and keep cases of work-related injuries at zero. About 130 employees involved in LM Guide and link ball production were given explanations of actual work-related injuries to bring a new awareness of the importance of things like protective equipment.
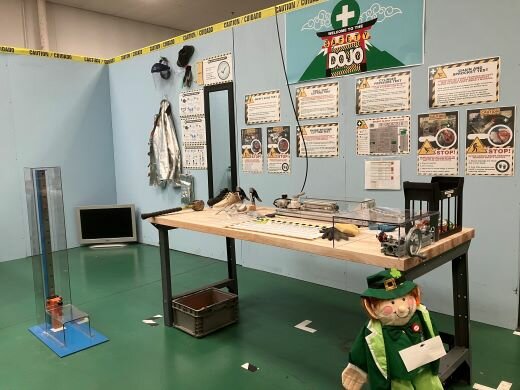
TRA CZECH (Czech Republic)
Awards
In October, TRA CZECH's various activities concerned with employee health (such as inviting a physical therapist to do a lecture, reducing noise on the production floor, proactively participating in the Health Days held by the city of Dačice, and offering a health-conscious menu in the company cafeteria) were evaluated by the Ministry of Health of the Czech Republic, and the company was awarded the highest ranking for the third time.
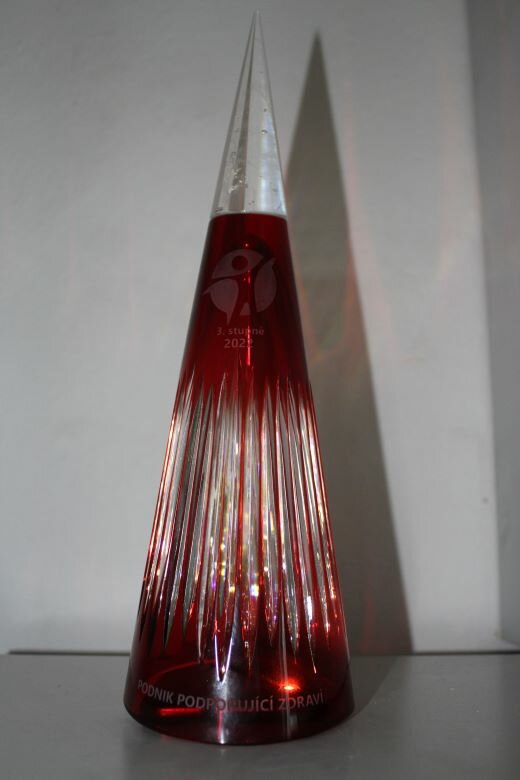