Promotion of Waste Reduction and Recycling
Achieving and Maintaining Zero Emissions
With our zero emissions activities, we aim to reduce all forms of waste we generate to zero by doing things like reusing it wherever possible. We promote zero emissions activities through controlling the use of direct and indirect materials, emissions and final waste, and reusing and recycling.
The waste produced by our business activities includes metal scrap, oil and liquid waste, grinding sludge, packaging, and plastic waste. By thoroughly separating our waste, we reuse or transform waste into usable materials, such as by turning steel scrap into steel-making material, sludge with grinding wheel dust into cement material, and oil and plastic waste into fuel.
Reducing plastic waste has garnered particular attention in recent years. THK is making steady strides in reducing the amount of plastic waste we generate by reusing and recycling plastics used in our production process as well as reducing plastics used by employees in our cafeterias (by transitioning to wooden spoons, for example).
THK Japan aims for an annual emissions rate (volume of waste disposed/total discharged) of less than 0.50%. Continuing from the successful achievement of this goal in 2022, we met this goal again in 2023 with a rate of 0.12%.
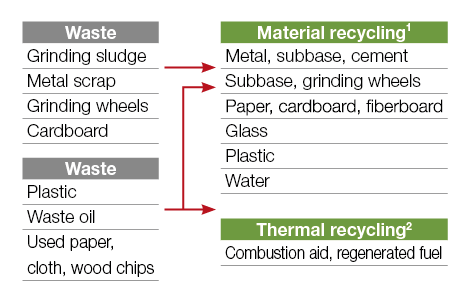
*2 Thermal recycling: Using waste as combustion material
Activities and Results Related to Plastic Waste
Efforts at Each Production Facility
Wuxi Plant (China)
In April, automatic waste oil recovery equipment was installed onto grinding machines to more fully recycle the waste oil coming from them.
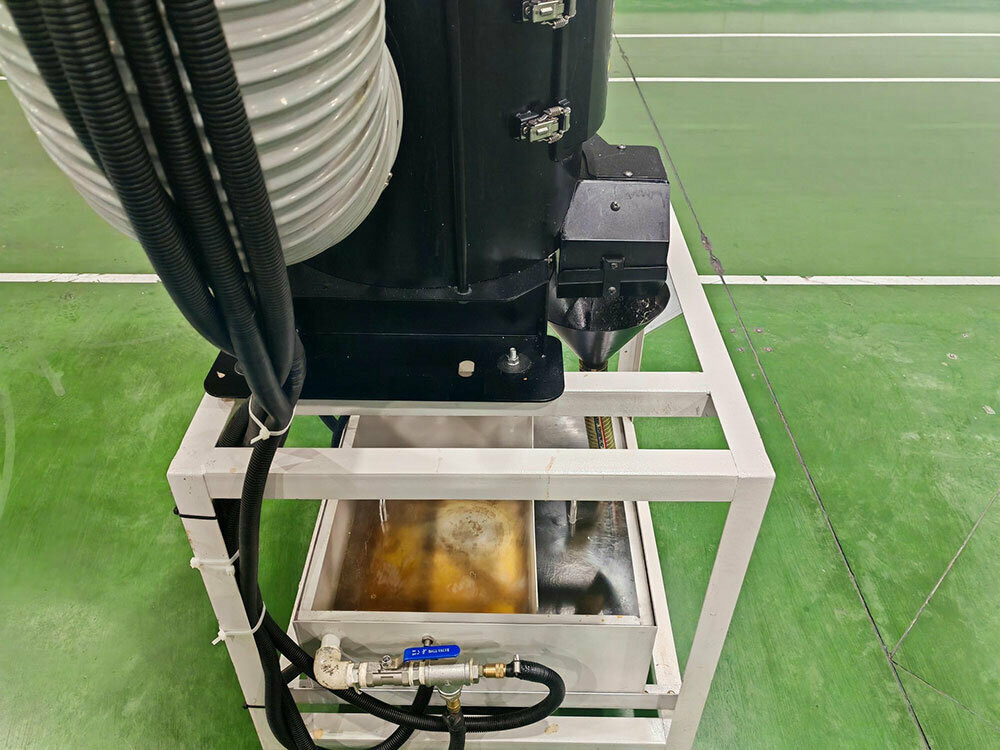
Cleaner Exhaust
In July, the five standard-specification compressors at the third-phase plant were replaced with oil-free screw models. This made it possible to become rated at the highest quality class for oil content in compressed air, Class 0 (compressed air purity management standard “Class 0” defined by ISO 8573-1 (2010) and JIS B 8392-1 (2012)).
Changzhou Plant (China)
Cooling Tower Upgrade
There are two lithium bromide air conditioning systems at the first-phase plant, but the facility was able to consolidate the work they were doing into a single high-efficiency cooling tower. This has reduced the amount of municipal water used by about 4,680 m3 per year.
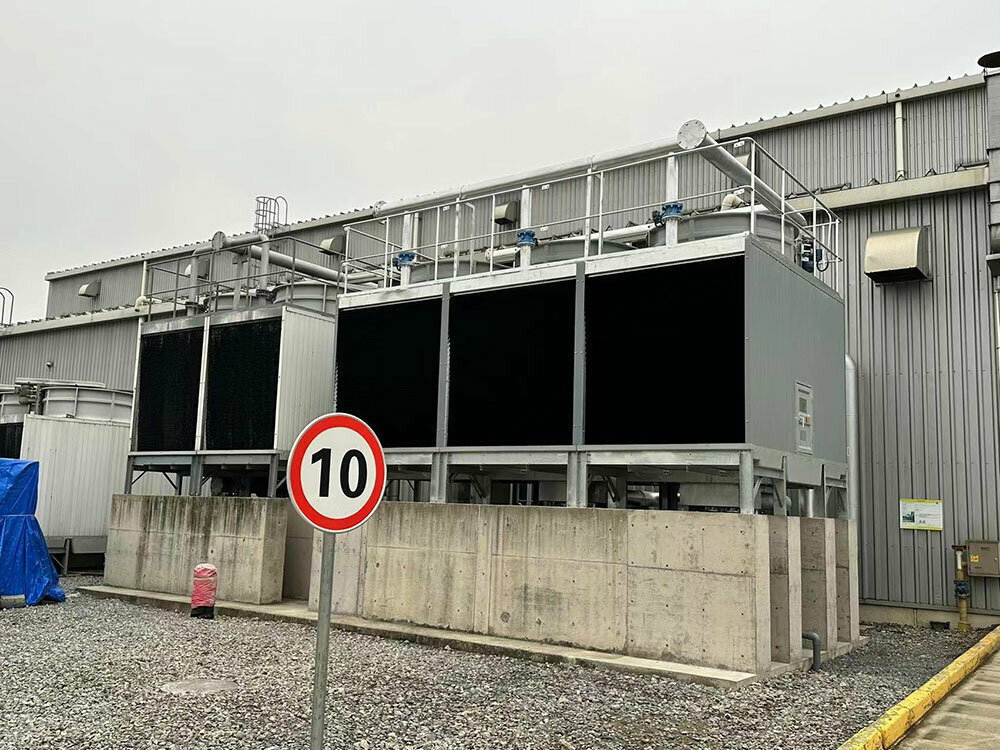